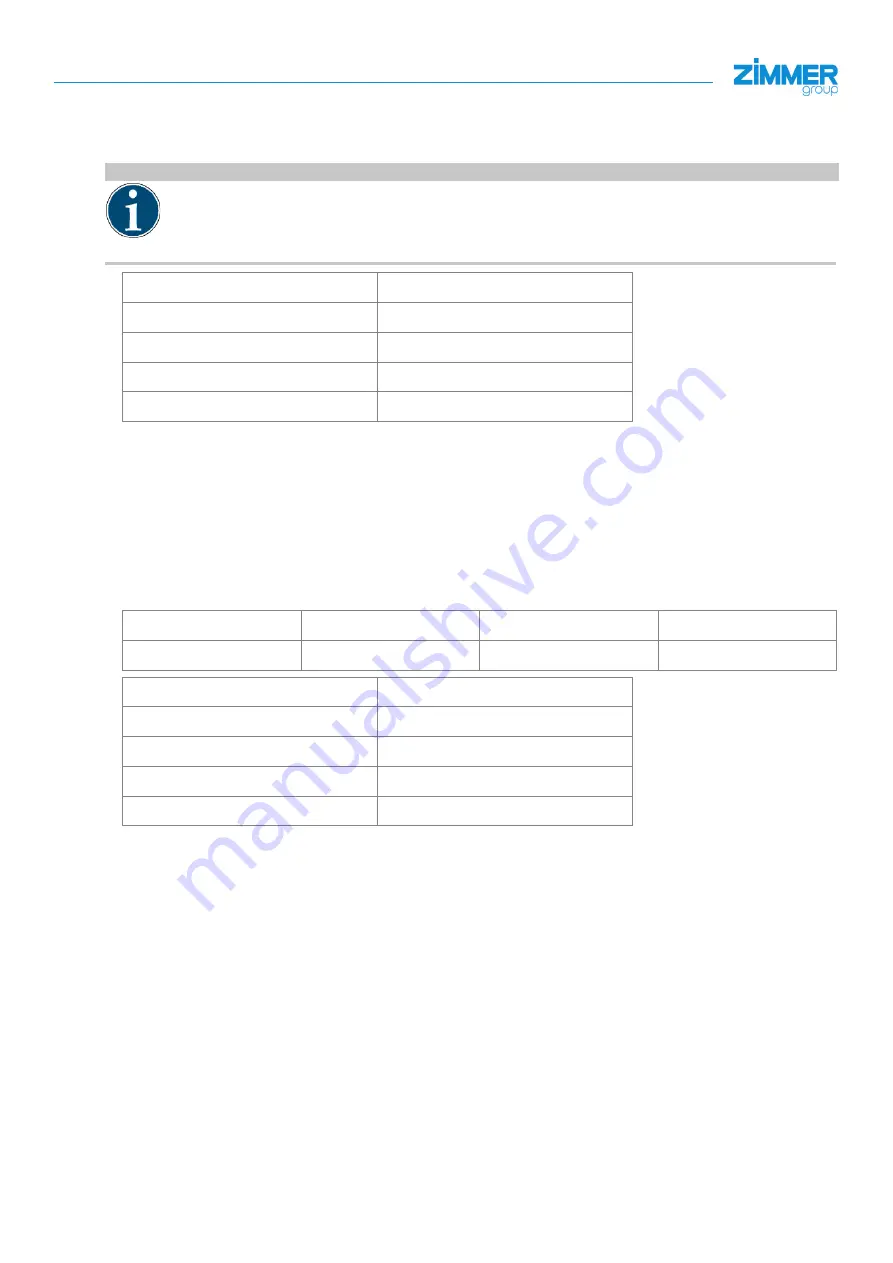
INSTALLATION AND OPERATING INSTRUCTIONS:
2-jaw parallel gripper, hybrid, HRC-04 series
21
Zimmer GmbH
●
Im Salmenkopf 5
●
77866 Rheinau, Germany
●
+49 7844 9138 0
●
+49 7844 9138 80
●
www.zimmer-group.com
DDOC00269 / d
EN / 3/31/2020
8.3.4 „PositionTolerance“ parameter
This parameter is used to configure the position tolerance with a resolution of 0.01 mm.
Thus the value range of 0 to 255 can be used to set a maximum tolerance of 2,55 mm in both directions.
INFORMATION:
Example:
If the „Teach position“ has a value of 1500 (i.e. 15.00 mm), a tolerance of 1.50 mm in both directions can
be set with a value of 150 in the „Position tolerance“ parameter.
By doing this, the TeachPosition window starts at 13.50 mm and goes all the way up to 16.50 mm.
Name
"PositionTolerance"
Data format
UINT8
Permission
Write
Transfer
Cyclical
Value range
0 to 255
8.3.5 „TeachPosition“ parameter
“TeachPosition” is used to tell the gripper at which position the workpiece is expected. The “PositionTolerance”
functions around this position. Thus the gripper can distinguish whether a correct or incorrect workpiece has
been gripped. Confirmation that the correct workpiece has been gripped is communicated to the control system
via the “StatusWord” parameter. If the detection is correct, the „Teach“ bit is set, thereby giving the user the opti-
on to monitor this work step.
By means of the position measuring system, it is possible to achieve a „TeachPosition“ accuracy of +/- 0.05 mm.
The following values are to be used:
Product
"BasePosition"
"WorkPosition"
"TeachPosition"
HRC-04-xxx
0
2000
0 to 2000
Name
"TeachPosition"
Data format
UINT16
Permission
Write
Transfer
Cyclical
Value range
0 to max. jaw stroke of the gripper