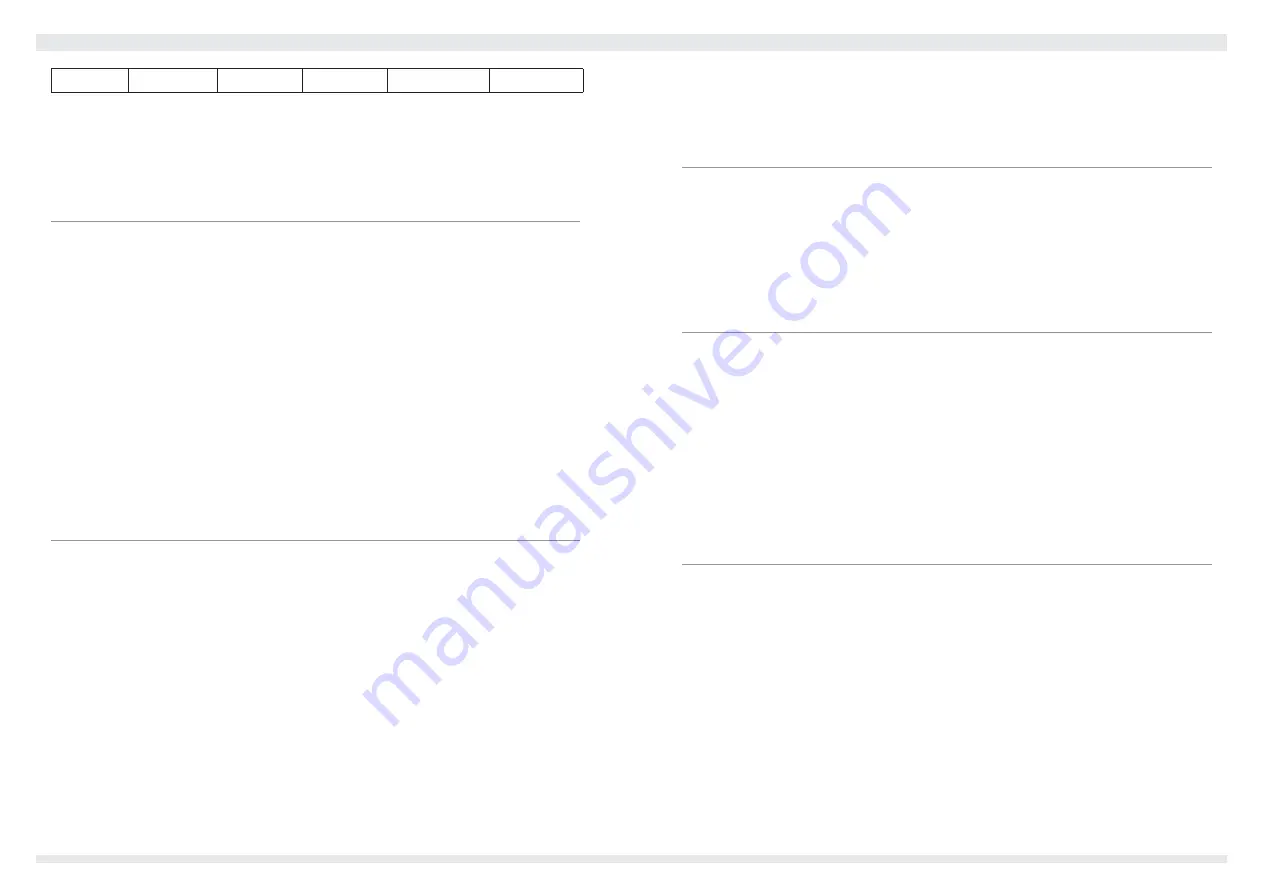
ELECTRIC VEHICLE MANAGEMENT SYSTEM V3
ZERO EMISSION VEHICLES AUSTRALIA
20
19
LTO
2.4V
1.6V
2.8V
2.7V
-30˚C – 60˚C
Quick tip: LiCo chemistry cells may be charged to 4.2V, but will achieve almost double the
cycle life if slightly undercharged to 4.1V instead – though at the loss of about 10% available
capacity. It also leaves some margin between peak charge voltage and maximum allowable
voltage, for tolerance of pack imbalance.
State of Charge Synchronisation
The EVMS receives current data over CAN bus from either a hall effect sensor or a shunt
interface. By integrating current flow over time, it is able to calculate battery SoC. But
because this calculation is an integration over time, it is possible for small measurement
errors to accumulate, resulting in possible inaccuracy in the state of charge value.
To mitigate this, the EVMS includes a mechanism to automatically resynchronise the SoC at
the end of any full charge cycle, using the configurable Full voltage setting to tell the EVMS
what voltage the pack is when fully charged. Ideally, set this to a volt or two below the peak
charge voltage of your charger for a small tolerance. When this voltage is reached during
a charge cycle, a one hour timer is started to allow the Constant Voltage phase of charging
to complete. After one hour, the the SoC will be synchronised back to 100%, the charger
will be turned off, then after the programmed Sleep Delay time the system will go to sleep
to save power.
The SoC can also be manually reset to 100% via the Options menu of the EVMS Monitor.
Stationary Applications
The EVMS configuration includes a setting for Stationary Mode, intended for use in battery
backup and off-grid power applications. In this mode, the Key input enables both Main
Contactor and Charge Enable outputs concurrently. An undervoltage cell will disable the
Main Contactor output (to remove any loads on the battery) and an overvoltage cell will
disable the Charge Enable output (to disable any charging sources).
Outputs will automatically be re-enabled once the cell voltage has recovered by a
configurable margin, known as hysteresis. For example, if BMS Hysteresis is set to 0.20V, the
Main Ctr output will not turn off until a cell is 0.20V below the Min Voltage threshold, and
will reset when cell is 0.20V above the Min Voltage threshold.
Common settings for LiFePO4 cells are a Min Voltage setting of 2.80V, Max Voltage of 3.60V,
and Hysteresis of 0.20V, giving a 2.6V-3.0V band for the Main Ctr output and 3.4V-3.8V
band for the Charge Enable output. LiCo cells have a more linear charge curve so typically
need a smaller hysteresis band around 0.05V-0.10V, with a Min Voltage setting about 3.00V
and a Max Voltage setting about 4.1V.
In Stationary Mode, the Charge Sense input is no longer used, and precharging is not
supported. The Aux Ctr output will be on permanently whenever the system is in Running
mode.
Use With Batteries Over 350VDC
The EVMS’s internal voltage measurement and isolation monitoring circuit has an absolute
maximum voltage rating of 400VDC, making it suitable for nominal battery pack voltages
up to about 350VDC. The EVMS may be used with higher voltages, but the HV+, HV- and
Main Ctr- connections must be omitted. Precharging and isolation monitoring are no longer
supported, and system voltage can only be calculated from the sum of all cells connected
to BMS modules.
Isolation Fault Detection
The EVMS has an internal high resistance connection (200Kohm) between the traction
circuit and the vehicle chassis. By monitoring microamps of current flowing across this
resistor, the EVMS can detect if the isolation between traction circuit and the vehicle chassis
is compromised, such as from damaged wiring insulation, excessive carbon buildup in DC
motors, or even a human touching a HV terminal.
This is quantified as a 0-100% range, where 0% represents a very low resistance path between
the traction circuit and the chassis, and 100% represents no detectable leakage. The default
warning threshold for leakage is 50%, which is usually sensitive enough to detect if a human
touches any of the HV terminals. Ideally, you should see at least 90% at all times.
Technical Support and Warranty Information
All ZEVA products are covered by a 12 month warranty against manufacturing faults or
failures under normal operating conditions. The warranty does not cover misuse of the
product, including but not limited to: excessive voltage or reversed polarity on terminals,
short circuits on outputs, opening of housings and/or modification of internal electronics,
severe impact damage (e.g due to vehicle crashes), submersion in water.
We have taken great care to design a safe and reliable product, but faults can happen. If
you believe your product has a fault, please contact us via our website to discuss. If it is
determined that a hardware fault is the likely cause, we will provide RMA information and a
return address to proceed with repairs.
If you have any questions not covered by this manual, please contact us via our website:
http://www.zeva.com.au/Contact