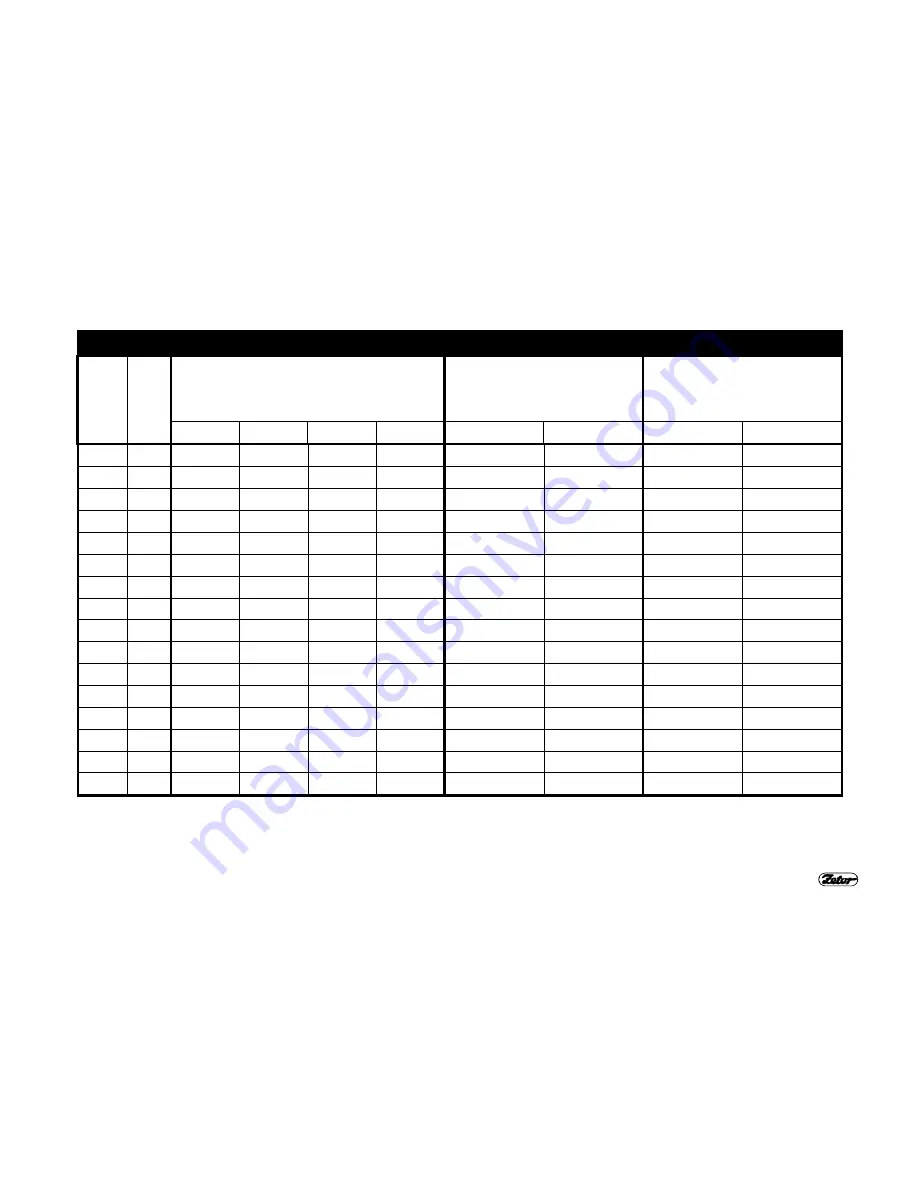
211
MAIN SPECIFICATIONS
FORWARD TRACTOR TRAVELLING SPEED - 40 KM/H
Tractor speed in km/h at rated engine
speed (2200 rpm) and below mentioned
size of rear tires
Dependent rear PTO shaft
540/1000
speed at rated
engine speed (2200 rpm)
Dependent rear PTO shaft
540/540E
speed at rated
engine speed (2200 rpm)
Gear
Stage
of multiplier
16,9 - 34 18,4 -34 18,4 - 30 13,6 - 36
540 rpm
1000 rpm
540 rpm
540E rpm
4
Hi
H 36,0 37,2 34,8 34,6 712,5 1344,4 1061,9 1344,4
L 27,7 28,6 26,8 26,6 712,5 1344,4 1061,9 1344,4
3
Hi
H 24,8 25,6 24,0 23,8 490,5 925,5 731,0 925,5
L 19,1 19,7 18,5 18,3 490,5 925,5 731,0 925,5
2
Hi
H 15,5 16,0 15,0 14,9 306,7 578,7 457,1 578,7
L 11,9 12,3 11,5 11,4 306,7 578,7 457,1 578,7
1 Hi
H
10,7
11,06
10,34
10,27
211,7 399,4 315,4 399,4
L 8,23 8,51 7,95 7,90 211,7 399,4 315,4 399,4
4
Lo
H 9,11 9,42 8,80 8,74 180,5 340,7 269,1 340,7
L 7,02 7,26 6,78 6,74 180,5 340,7 269,1 340,7
3
Lo
H 6,27 6,48 6,06 6,02 124,3 234,5 185,2 234,5
L 4,83 4,99 4,67 4,64 124,3 234,5 185,2 234,5
2
Lo
H 3,92 4,05 3,79 3,76
77,7 146,6 115,8 146,6
L 3,02 3,12 2,92 2,90
77,7 146,6 115,8 146,6
1
Lo
H 2,71 2,80 2,62 2,60
52,3 98,7 77,9 98,7
L 2,08 2,15 2,01 2,00
52,3 98,7 77,9 98,7
Hi – road gears
Lo – reduced gears
H – multiplier high gear
L – multiplier low gear
Summary of Contents for PROXIMA PLUS 10541
Page 1: ......
Page 2: ......
Page 18: ...18 NOTES...
Page 19: ...19 NOTES...
Page 20: ...20 NOTES...
Page 34: ...34 ACQUAINTANCE WITH TRACTOR E131...
Page 36: ...36 ACQUAINTANCE WITH TRACTOR E132...
Page 48: ...48 NOTES...
Page 49: ...49 NOTES...
Page 50: ...50 NOTES...
Page 67: ...67 NOTES...
Page 68: ...68 NOTES...
Page 73: ...73 NOTES...
Page 74: ...74 NOTES...
Page 83: ...83 NOTES...
Page 84: ...84 NOTES...
Page 90: ...90 NOTES...
Page 91: ...91 NOTES...
Page 92: ...92 NOTES...
Page 104: ...104 NOTES...
Page 105: ...105 NOTES...
Page 106: ...106 NOTES...
Page 115: ...115 NOTES...
Page 116: ...116 NOTES...
Page 123: ...123 NOTES...
Page 124: ...124 NOTES...
Page 130: ...130 NOTES...
Page 131: ...131 NOTES...
Page 132: ...132 NOTES...
Page 142: ...142 NOTES...
Page 143: ...143 NOTES...
Page 144: ...144 NOTES...
Page 151: ...151 TRACTOR MAINTENANCE LUBRICATION CHART E651...
Page 162: ...162 NOTES...
Page 163: ...163 NOTES...
Page 164: ...164 NOTES...
Page 183: ...183 NOTES...
Page 184: ...184 NOTES...
Page 198: ...198 NOTES...
Page 215: ...215 NOTES...
Page 216: ...216 NOTES...
Page 223: ......