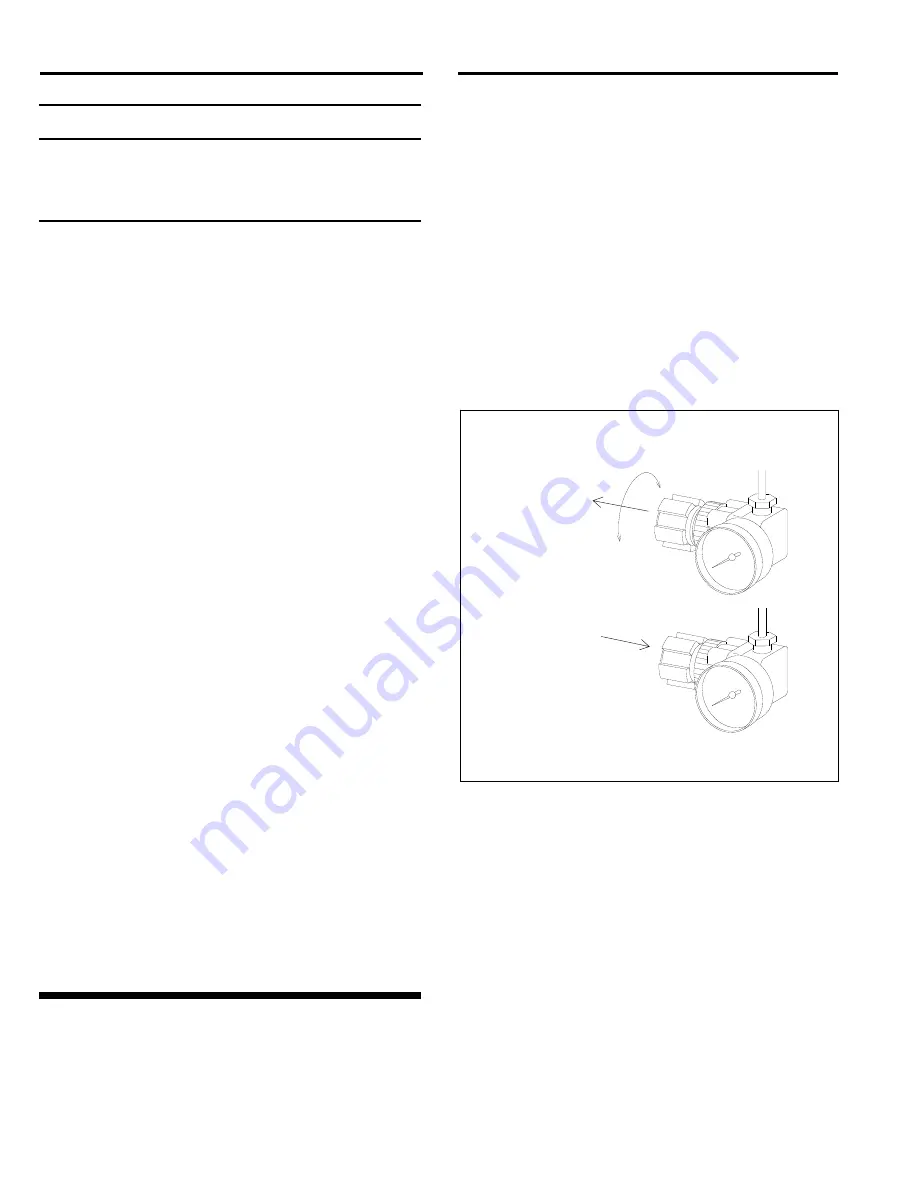
BNP
®
6012 and 7212 SUCTION BLAST CABINETS
Page 14
© 2019 CLEMCO INDUSTRIES CORP.
www.clemcoindustries.com
Manual No. 27723, Rev. B 04/19
NOTICE
To prevent rapid frosting of the view window,
avoid pointing the blast nozzle toward the
window and install a view-window cover lens,
per Section 7.3.
4.4.8
When holding parts off the grate, use a solid
conductive backrest to support the part. Without this
assist, especially with longer blasting operations, the
operator will tire easily from resisting blast pressure, and
static electricity could build up in the ungrounded part
and cause static shocks. Whenever possible avoid
holding small parts that require blasting into the glove.
4.4.9
If an object should fall through the grate, stop
blasting immediately and retrieve it.
4.5
Blasting Technique
4.5.1
Blasting technique is similar to spray painting
technique. Smooth continuous strokes are most
effective. The distance from the part affects size of blast
pattern. Under normal conditions, hold the nozzle
approximately 3" to 6" from the surface of the part.
4.6
Stop Blasting
4.6.1
To stop blasting, remove foot pressure from the
top of the foot pedal.
4.6.2
Use the blow-off nozzle to blow media off
cleaned parts.
4.6.3
Keep door closed and exhauster running until
the cabinet is clear of all airborne dust.
4.6.4
Unload parts.
4.7
Shutdown
4.7.1
Shut off the air-supply valve, bleed the air-
supply line, and drain the compressed-air filter and dust-
collector pulse reservoir.
4.7.2
Switch OFF the lights and exhauster.
5.0
ADJUSTMENTS
5.1
Blasting Pressure (pilot regulator) ‒ Figure 18
5.1.1
The pilot regulator, located on the top-left side of
the cabinet, enables the user to adjust blasting pressure
while blasting to suit the application. The suitable
pressure for most purposes is about 80 psi. Lower
pressures may be required on delicate substrates and
will reduce media breakdown. Higher pressure may be
required for difficult blasting jobs on durable substrates,
but will increase media breakdown. If pressure is too
high, suction in media hose will decrease, and if high
enough, cause blowback in the hose. Optimal production
can only be achieved when pressure is carefully
monitored.
Figure 18
5.1.2
To adjust pressure, unlock the knob by pulling it
out, as shown in Figure 18, and turn it clockwise to
increase pressure or counterclockwise to decrease
pressure. Pressure may drop slightly from closed-line
pressure when blasting starts. Once operating pressure
is set, push the knob in to lock it to maintain the setting.
5.2
Air Jet Adjustment ‒ Figure 19
5.2.1
Thread the air jet 4-1/2 to 5 full turns into the
gun body. Doing so will leave 3-1/2 to 4 threads exposed
past the lock nut. Tighten the lock nut to maintain the
setting. Refer to Section 9.3 for optional adjusting tool,
which correctly positions the jet. Instructions are
provided with the tool.
Pressure regulator is located
on left side of view window.
Increase pressure
When viewed from the knob end,
turn clockwise to increase pressure
turn counterclockwise to decrease pressure.
Decrease pressure
Pull knob out to
unlock and adjust
pressure.
Push knob in to lock.