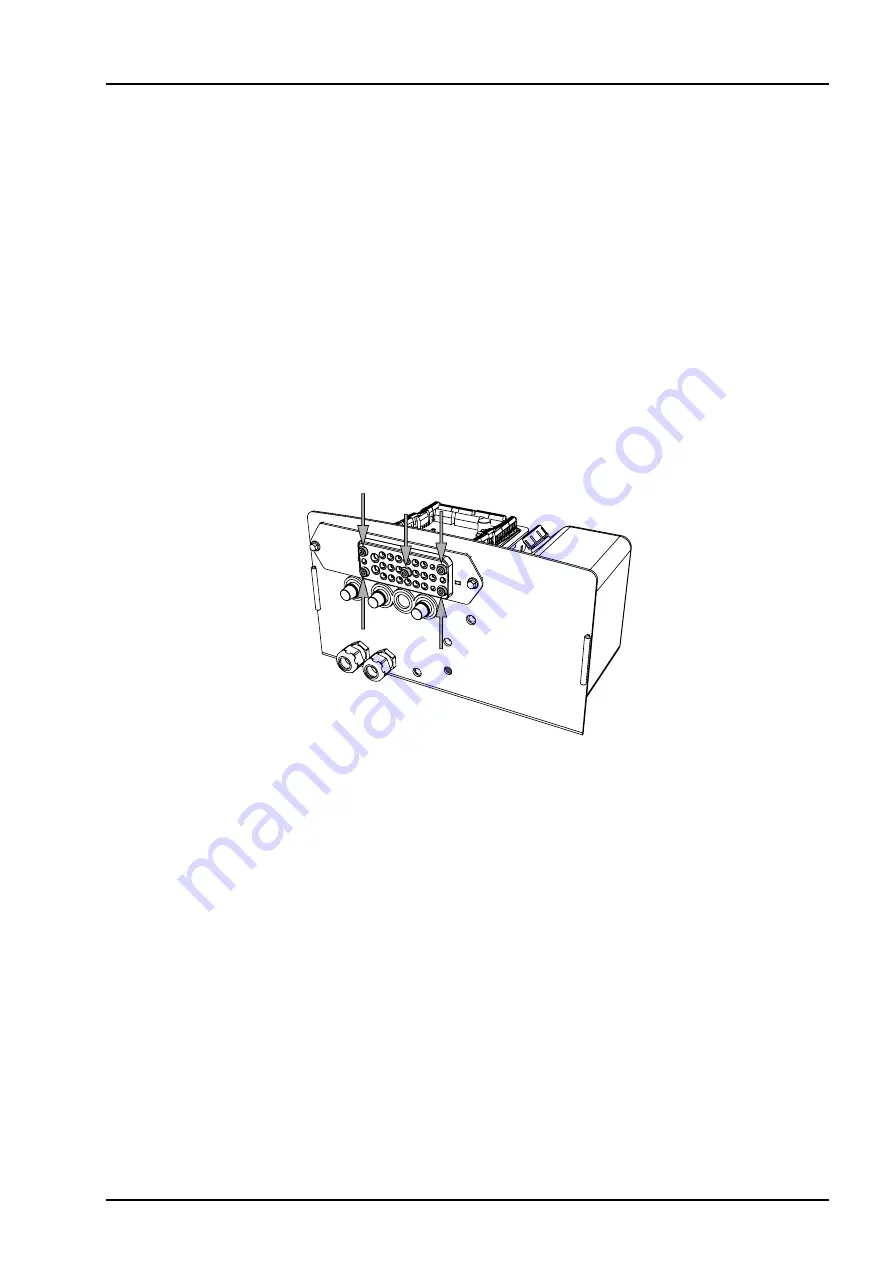
Z 45/75-90/110
Connection
45
www.zepro.com
6
Connection
6.1
Cable grommet
6.1.1
Before cable connection
To be able to install/remove/adjust the cables in the cable grommet, the five screws must be loosened.
1.
Loosen the five screws on the cable grommet, see
Image 66. Cables can now be installed/removed/adjusted
in the grommet. The cable should be installed together with existing cabling using cable ties.
Image 66. The cable grommet's five screws
Hydraulic unit 5915
6.2
Connection
1. Run the cabling through the grommet.
2. Connect the relevant controller. See Section 6.4 - 6.5.
3. Where applicable, connect the warning lights. See Section 6.6 - 6.7.
4. Where appropriate, plug in cab switch (CS) and open platform alarm. See Section 6.8 - 6.9.
6.3
After connection
1.
When all cables are suitably located in the cable grommet, tighten the five screws; see
Image 66.
Tightening torque: 5 Nm.
Summary of Contents for Z 45-90
Page 2: ......