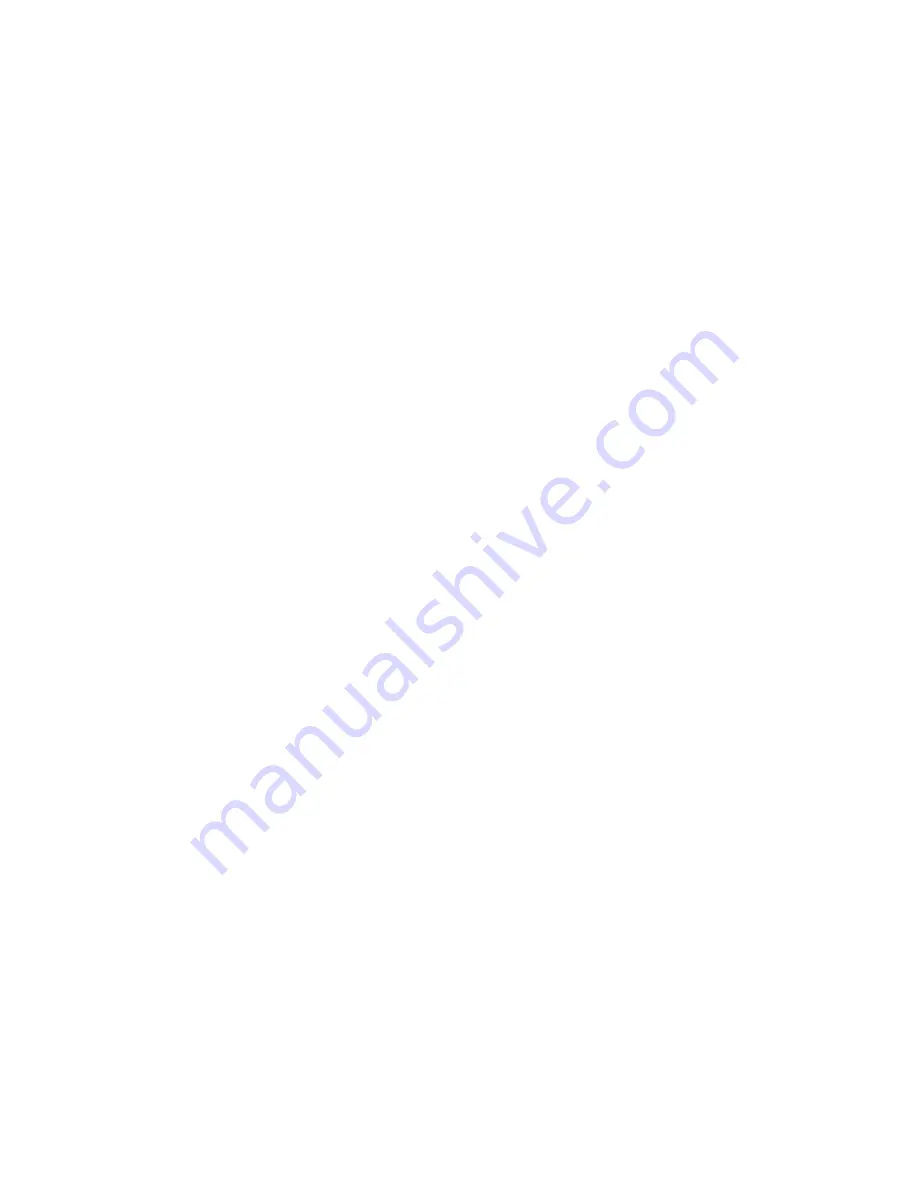
ZENA mobile welding system -- Operators Manual -- Series 150 & 200 Welders
24
24
defective connector terminal, or due to some surface corrosion that may have
formed on the connector surfaces.
If the problem is corrosion (which may be noticeable as a slight sandy
roughness/drag which can be felt as the connectors are connected and
disconnected), the male terminals can be cleaned by lightly dragging a sharp
pen knife or box cutter blade across the both sides of each “spade”. The
female connector’s surface can be then “cleaned” by inserting and reinserting
the male connector a number of times (until reliable operation is noted).
Corrosion can then be prevented by applying a good quality dielectric grease
(not a conductive grease) to the contact surfaces.
If the problem is not due to surface corrosion, or if the corrosion is so bad as to
cause continuing erratic operation, go to step 3a.4.
NOTE: If you are using a cable extension, or a quick disconnect system, of any
sort, with your welder, remove it temporarily to insure that the problem noted is
not caused by a wiring fault in the cable extension.
3a.4 You have a problem which requires the assistance of our tech support
department (877-ZENA INC or 615-897-2011).
4. Welding
Power
Boost
is
Not
Working
and
All
Other
Welding
Functions
are
OK
4.1
It is likely that your Control Handle is defective.
You have a problem which requires the assistance of our tech support
department (877-ZENA INC or 615-897-2011).
5. Welding
Power
is
“ON”
CONTINUOUSLY -- Control Models
WC.12 & WC.24
5.1
Temporarily disconnect the plug that is used to connect the Control
Handle/Control Cable Assembly to the Power Control Module. If welding
power is now “OFF”, go on to the next step.
If welding power is still “ON” continuously, go to step 5.3.
NOTE: If you are using a cable extension, or a quick disconnect system, of any
sort, with your welder, remove it temporarily to insure that the problem noted is
not caused by a wiring fault in the cable extension.
5.2
Reconnect the plug used to connect the Control Handle/Control Cable Assembly
to the Power Control Module.
With the engine OFF, open the Control Module cover, rotate the Power Control
Dial on the Control Handle/Control Cable Assembly to its full counter clock
wise position (CCW), turn on power to the Control Module and observe Lamp
#2. If Lamp #2
is
illuminated, go to step 5.6.
If Lamp #2
is not
illuminated, go on to the next step.
5.3
It is likely that either your Power Generator or your Control Module is defective.
You can easily check for a component failure in the Power Generator by
disconnecting the two Gray wires which are used to connect the Control Module
to the Power Generator’s control terminals, and check in the electrical
resistance between
either
of the terminals and the case of the Power
Generator. A normal reading is an “open” circuit (an infinite resistance).
If your meter shows
any
measurable resistance, your Power Generator has a
component failure, and must be returned for repair. Go to Step 5.5.
If your meter shows
no
measurable resistance, go to the next step.