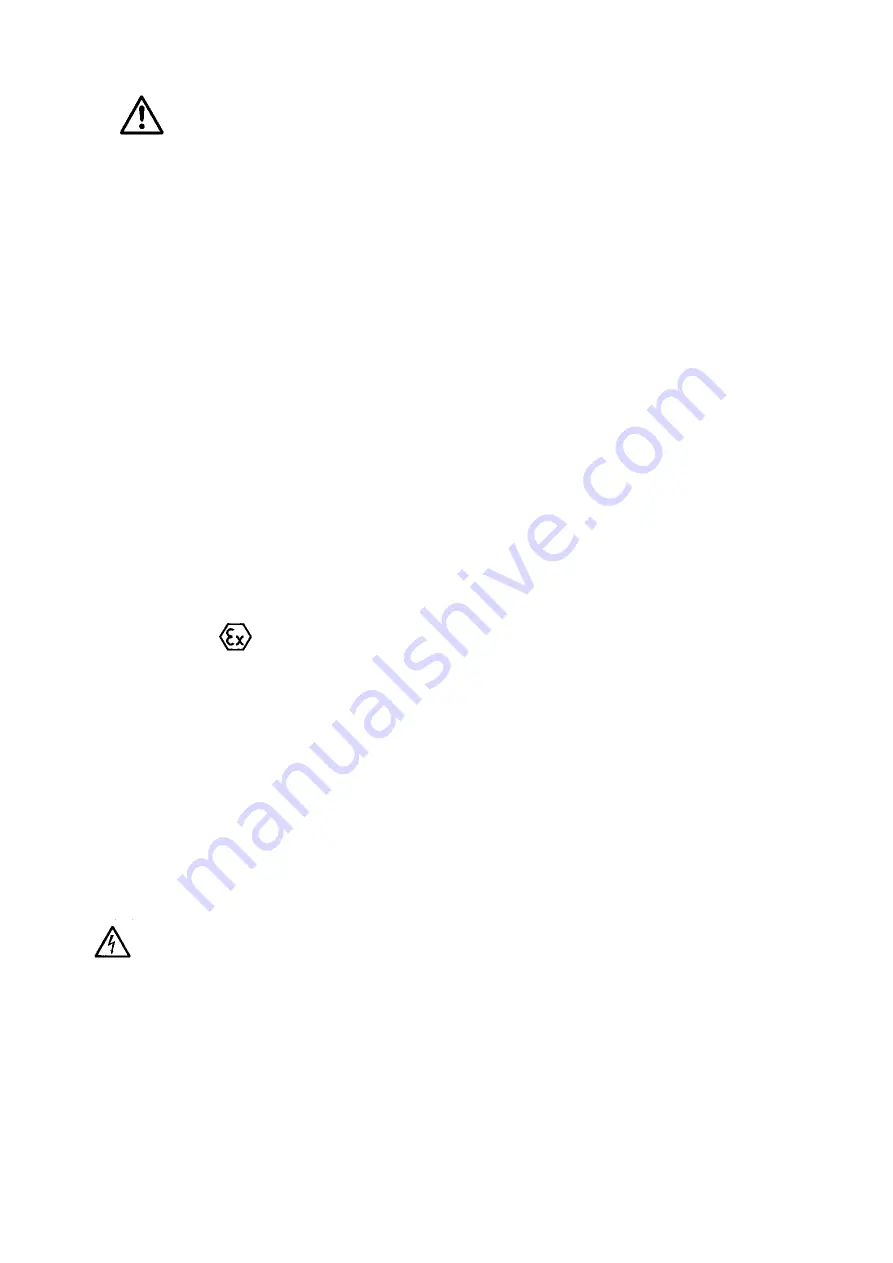
26
5.2 Hydraulic system
These pumps are not to be mounted in dry installation, since a minimum water level up to the bottom
edge of the motor housing is prescribed by the guideline on protection against explosion.
Installation with supporting ring:-Mount supporting ring to intake flange of the pump and install pump.
Ensure stability of the pump.
- Optionally connect pressure side by means of flange DN 50 or thread.
(The pump is equipped with a female thread G2 and a flange DN 50.)
-If a hose is to be laid on the pressure side, kinks
are to be avoided
.
- Avoid kinks during the laying of the supply cable.
Lay supply cable without tensile loading and without causing
chafe marks.
Installation for shaft fitting: - Position pipe clamp on inner rim of the shaft and loosely fix it
with two screws.
- Sound out position of guide pipe frame for coupling pedestal,
adjust coupling pedestal on shaft bottom and mount it with the heavy-duty
dowels which are included in the delivery.
- Install pressure pipe and valves in a tension-free manner.
- Slip the guide pipe on the coupling pedestal, shorten it to correct
length, slip on pipe clamp and tighten it for good.
- Mount coupling element and lowering chain to the pump, lower pump with the
chain (insert guide pipe into coupling element) and couple it, hang the chain up
on the pipe clamp so that it is ready to hand.
-
Lay supply cable. Avoid kinks and lay supply cable without tensile
loading and without causing chafe marks.
5.3 Level control system
The pumps ZFS 71 have to be controlled by means of a level control in such a way, that a decline of the water
level beneath the minimum allowable level (bottom line of motor housing) is avoided at all costs.
The level control can be effected by means of a floating switch, electropneumatically (press switch) or by means of
other applicable methods. The switching point of the pump should be set in such a way, that the pump is entirely
submersed under water.
If the level control is effected via a floating switch, the signal of the floaters has to be transmitted via intrinsically safe
Ex i –relays.
6. Commissioning
Check all connections for proper assembly, set gate valve on passage and check level control system for proper
operation.
During the conduction of the test run, check pipes for tightness and reseal them, if necessary.
7.
Maintenance and repair
- Disconnect the power supply before carrying out any kind of work on the plant!
After an operation time of six to twelve months, the oil storage inside the seal carrier always has to be controlled as
follows: Put the pump on side on a clean surface and position it in such a way that the oil filling screw faces upwards.
Take out the screw and check the oil level. If only a small quantity of oil is lacking, the oil storage can be filled up
without any problems. If a considerable quantity of oil is lacking, or if the oil is mingled with water, the customer
service has to be informed.
All other maintenance works on the pump and on the electrical equipment should be carried out by the manufacturer
or an authorised qualified company in intervals of six to twelve months (or also in shorter intervals, according to case
of operation) as well. Please immediately inform the customer service in case of damages to the pump and/or the
electrical equipment.