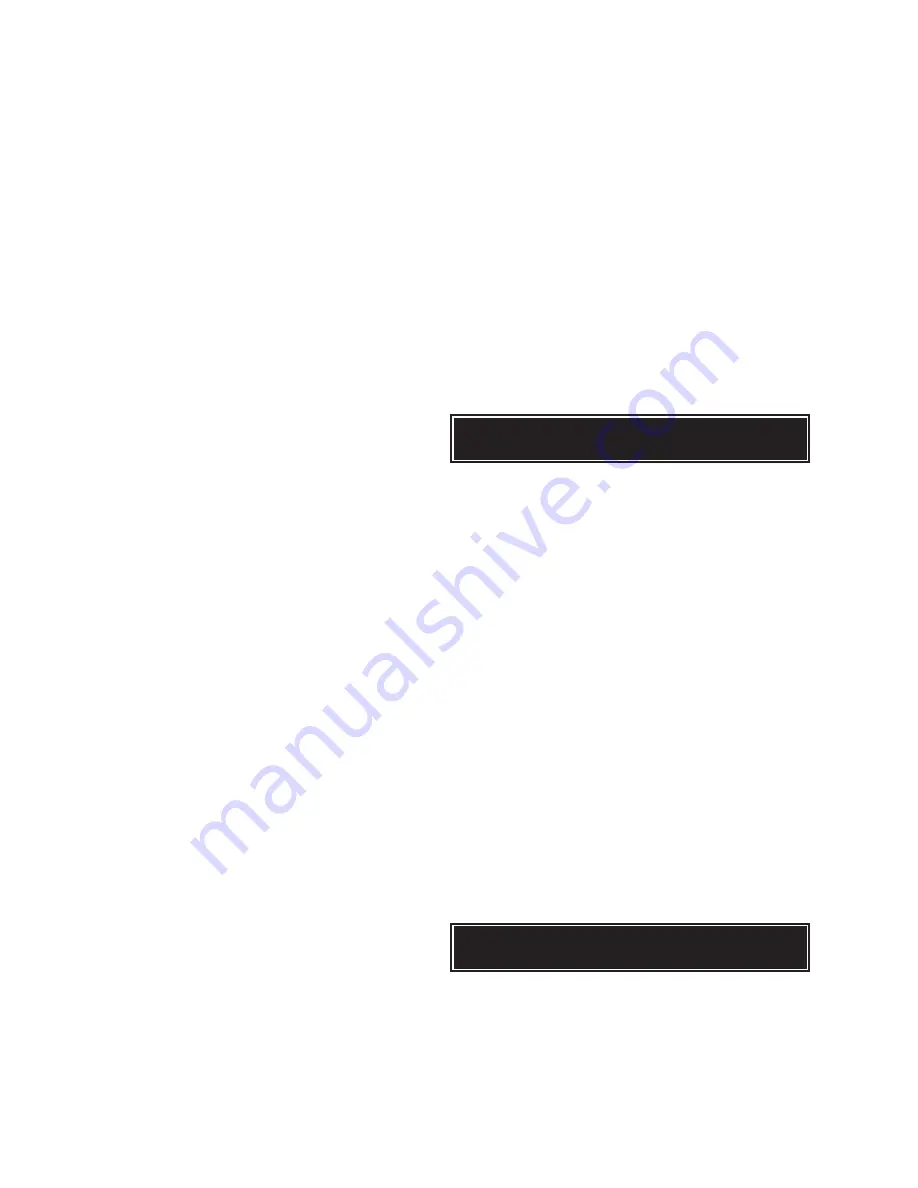
YORK INTERNATIONAL
64
operating requirements. In addition, the low battery mes-
sage which is displayed for this condition will disappear.
NOTE: If a power failure should again occur, the above
process will again need to be repeated to bring
the chiller back on line.
In the unlikely event the low battery message should
ever appear, it will require the RTC Chip U13 on the
Microprocessor Board (Fig. 12) to be replaced. Care
should be taken to assure that the chip is properly in-
stalled. Pin 1 (dimple in the top of the chip) must be
oriented as shown (Fig. 12). The part number for the
RTC Chip is 031-00955-000.
CRANKCASE HEATER
The crankcase heater for a compressor will be ON
whenever the compressor is not running. The heater is
interlocked into the compressor motor contactor and is
not controlled by the microprocessor.
The purpose of the crankcase heater is to prevent the
migration of refrigerant to the crankcase during shutdown
assuring proper lubrication of the compressor on start-up.
Anytime power is removed from the chiller for more
than an hour, the crankcase heater should be left on
for 24 hours prior to start. This can be accomplished
by applying 115VAC to the control panel.
EVAPORATOR HEATER
The evaporator heater prevents water standing in the
evaporator from freezing. Whenever outdoor ambient
temperature drops below 40°F, the microprocessor will
turn the evaporator ON. If temperature rises above 45°F,
the heater will be turned off.
METRIC DISPLAY
The control panel is capable of providing displays of
pressure and temperature in metric values. Tempera-
tures will be displayed in °C and pressures in kPa.
A Metric to English temperature conversion table is
provided on the rear cover of this manual. Pressure
can be converted from PSI to kPa using the formula
PSI x 6.89 = kPa.
To obtain panel displays in metric, Switch 5 of Dip
Switch S1 on the Microprocessor Board must be placed
in the OPEN position (Page 28). The positioning of this
switch can then be verified by pushing the OPTIONS
key and verifying that METRIC UNITS READOUT is
programmed (Page 26).
EMS/BAS CONTROLS
The microprocessor is capable of REMOTE START/
STOP, REMOTE UNLOADING (Pulidown demand lim-
iting), and REMOTE SETPOINT RESET. These func-
tions can be easily utilized by connecting use supplied
dry contacts to the Microprocessor Board.
REMOTE START/STOP BY A CYCLING DEVICE OR
TIME CLOCK
Remote START/STOP is accomplished by connecting
a time clock or other dry contact in series with the
flow switch on terminals 13 & 14. See Fig.11 for the
location of the terminals. The contact must be closed
to allow the chiller to run. Any time the contact opens,
the chiller will shut down and the following status mes-
sage will be displayed.
Wiring from these contacts should not exceed 25 ft.
and should be run in grounded conduit that does not
carry any wiring other than control wiring. Additionally,
if an inductive device (relay, contactor) is supplying
these contacts, the coil of the device must be sup-
pressed with a user supplied YORK P/N 031-00808
suppressor.
REMOTE SETPOINT RESET
(REMOTE RESET TEMP RANGE)
Remote Setpoint Reset allows resetting the setpoint
upward from the programmed value in memory. This is
accomplished by connecting a dry contact between
terminals 13 & 17. See Fig. 11 for the location of these
terminals. Closing the contact for a defined period of
time allows reset of the setpoint upward by up to 40°F
above the setpoint programmed in memory.
The maximum desired reset must be programmed into
memory and can be a value of 02 to 40°F. This value
will vary according to the users requirements. To pro-
gram the reset, press the REMOTE SETPOINT TEMP
RANGE key. The following message will appear.
The display will indicate the REM SETPOINT which is
always equal to the chilled liquid setpoint plus the off-
set from the reset signal. The display will also show
the REM RANGE which is the same as the maximum
reset required. Key in the maximum reset for the REM
S Y S # 1
N O
R U N
P E R M
S Y S # 2
N O
R U N
P E R M
R E M
S E T P O I N T
=
4 0 . 0
R E M
R A N G E
=
2 0
D E G F