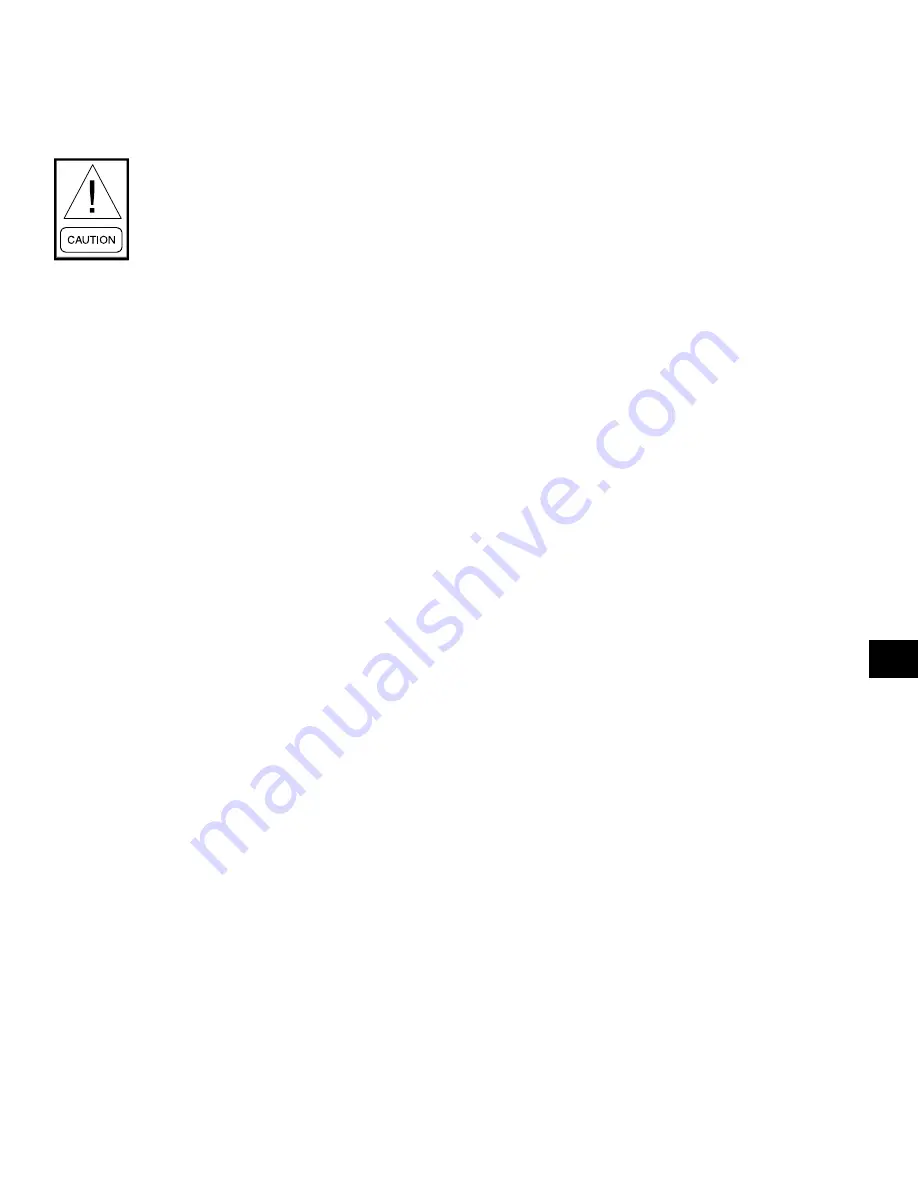
42
JOHNSON CONTROLS
or copper line, but do not tighten the flare nut. Using
clean oil of the correct type (“L” oil), pump oil until all
air has been purged from the hose then tighten the nut.
Stroke the oil pump to add oil to the oil system. The oil
level should be between the middle of the lower and
middle of the upper sight glasses of the oil separator.
Approximately 5 gallons is present in the entire chiller
system, with 1-2 gallons in the oil separator.
Fans
Check that all fans are free to rotate and are not dam-
aged. Ensure blades are at the same height when rotated.
Ensure fan guard is securely fixed.
Isolation/Protection
Verify that all sources of electrical supply to the unit
are taken from a single point of isolation. Check that
the maximum recommended fuse sizes given in the
Technical Data Section have not been exceeded.
Control Panel
Check the panel to see that it is free of foreign materials
(wire, metal chips, etc.) and clean out if required.
Power Connections
Check the customer power cables are connected correct-
ly. Ensure that connections of power cables within the
panels to the circuit breakers, terminal blocks or switch
disconnectors are tight.
Grounding
Verify that the unit’s protective terminal(s) are properly
connected to a suitable grounding point. Ensure that all
unit internal ground connections are tight.
Overloads
Ensure that the fan overloads settings are correct for the
type of fan fitted.
Supply Voltage
Verify that the site voltage supply corresponds to the
unit requirement and is within the limits given in the
Technical Data Section.
Control Transformer
The 3-wire control transformer is mounted in the options
panel. It is important to check that the correct primary
tapping has been used:
With the supply to the unit isolated remove the lid to
the transformer box.
COMMISSIONING
PREPARATION
Commissioning of this unit should
only be carried out by YORK Autho‑
rized personnel.
The
Millennium
Microcomputer Control System
Operating Instructions must be read in conjunction
with this section.
PREPARATION – POWER OFF
The following checks should be made with the customer
supply/supplies to the unit switched OFF.
Inspection
Inspect unit for installation damage. If found take action
and/or repair as appropriate.
Refrigerant Charge
Units are normally shipped as standard with a full
refrigerant operating charge. Check that refrigerant
pressure is present in both systems and that no leaks
are apparent. If no pressure is present a leak test
must be undertaken, the leak(s) located and repaired.
Repaired systems and units supplied with a nitrogen
holding charge must be evacuated with a suitable vac-
uum pump/recovery unit as appropriate to below 100
microns.
Do not liquid charge with static water in the cooler.
Care must also be taken to liquid charge slowly to avoid
excessive thermal stress at the charging point. Once the
vacuum is broken, charge into the condenser coils with
the full operating charge as given in the Technical Data
Section.
Valves
Open each compressor suction, economizer, and dis-
charge valves fully (counter-clockwise) then close one
turn of the stem to ensure operating pressure is fed to
the pressure transducers. Open the liquid line service
valve fully and ensure the oil return line ball valve is
open in each system.
Compressor Oil
To add oil to a circuit - connect a YORK hand oil pump
(Part No. 470-10654-000) to the 1/4” oil charging valve
on the oil separator piping with a length of clean hose
5
Summary of Contents for YCAS 0138EB
Page 50: ...50 JOHNSON CONTROLS This page intentionally left blank...
Page 61: ...61 JOHNSON CONTROLS FORM 201 18 NM7 This page intentionally left blank 7...
Page 70: ...70 JOHNSON CONTROLS Technical Data FIG 22A CONTROL PANEL COMPONENT LOCATIONS...
Page 71: ...71 JOHNSON CONTROLS FORM 201 18 NM7 LD03280 FIG 22B POWER PANEL COMPONENT LOCATION 7...
Page 72: ...72 JOHNSON CONTROLS Technical Data LEGEND LD03281...
Page 73: ...73 JOHNSON CONTROLS FORM 201 18 NM7 LD03282 LD03283 LD03284 7...
Page 74: ...74 JOHNSON CONTROLS Technical Data CONNECTION DIAGRAM SYSTEM WIRING LD06256 LD03231 LD03232...
Page 75: ...75 JOHNSON CONTROLS FORM 201 18 NM7 COMPRESSOR TERMINAL BOX LD03233 7...
Page 76: ...76 JOHNSON CONTROLS LD03285 Technical Data...
Page 77: ...77 JOHNSON CONTROLS FORM 201 18 NM7 3 4 5 6 3 4 5 6 7 8 5 6 3 4 7 8 9 10 LD06840A 7...
Page 181: ...181 JOHNSON CONTROLS FORM 201 18 NM7 NOTES...
Page 182: ...182 JOHNSON CONTROLS This page intentionally left blank...
Page 183: ...183 JOHNSON CONTROLS FORM 201 18 NM7 This page intentionally left blank...