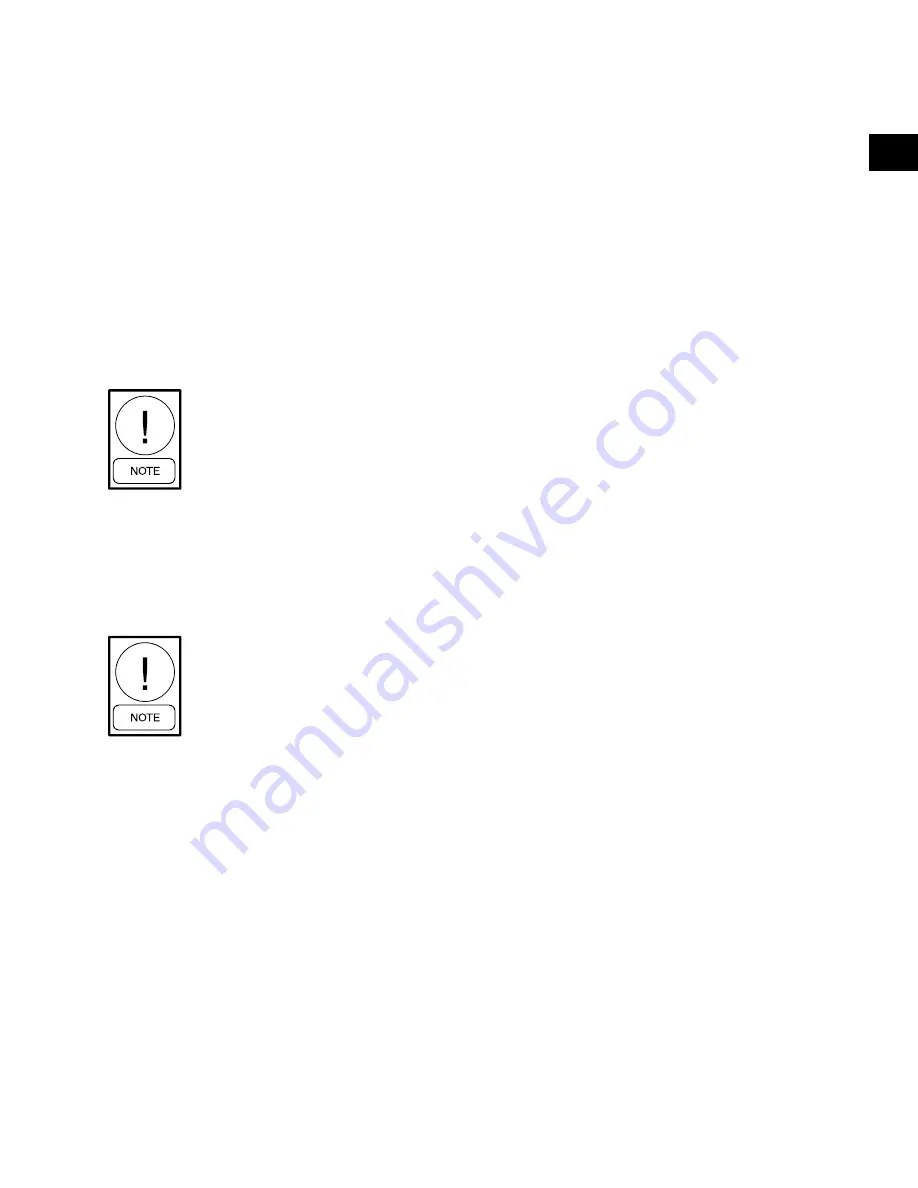
133
JOHNSON CONTROLS
FORM 201.18-NM7
control power is applied to the panel, if no fault condi-
tions are present. When a fault occurs which locks out
a system the respective contacts open. If chiller power
is lost or a unit fault occurs, such as a Low Water Temp
fault, contacts for all systems will open.
Contacts for SYS 1 are located on the bottom right of
the microprocessor panel, terminals 23 and 24. SYS 2
contacts are located on terminals 27 and 28. See Fig. 12,
Page 39 for the location of these terminals.
A 28VDC or 120VAC (60 Hz models) or up to 240VAC
(50 Hz models) external alarm circuit (supplied by oth-
ers) may be connected to these contacts. The contacts
are rated at 125VA.
If any inductive load devices (relay or
contactor) supplied by the user are in
the electrical circuit connected to the
dry alarm contacts, the device must
be suppressed at the load with a RC
suppressor YORK Part Number 031‑
00808‑000 across the inductive coil.
(Typically, several are supplied loose
with the panel). Failure to install sup‑
pressors will result in nuisance faults
and possible damage to the chiller.
If the alarm circuit is applied in an
application used for critical duty (such
as process duty or cooling other criti‑
cal equipment) and the alarm circuit
should fail to function, YORK will not
be liable for damages.
1.20 RUN STATUS (CHILLER)
Chiller Run Status contacts between Terminal 28 and
29 close whenever one of the systems is running. These
contacts are located on the bottom right of the Micro-
processor Board and are rated (voltage and current) the
same as the alarm contacts (Section 1.19). Also use a
suppressor, same as alarm contacts (Section 1.19). In-
dividual system “Run Status” is not available.
1.21 LEAD / LAG COMPRESSOR SELECTION
The chiller may be set up for AUTO or MANUAL Lead/
Lag. This is accomplished by programming the option
under the Program Key. Details for programming the
Manual/Auto Lead/Lag Selection are discussed in Pro-
gram Key Section 8, page 163.
When AUTO Lead/Lag is utilized, the micro attempts
to balance run time between the two compressors. A
number of conditions can occur which will prevent this
from happening. Factors determining lead/lag selection
and the resulting lead/lag determination are:
1. The micro automatically defaults the lead to SYS 1
and the lag to SYS 2 if both compressors are ready
to start (Anti-recycle Timers timed out) and com-
pressors have equal run time.
2. If all compressors are ready to start (Anti-recycle
timers timed out), the compressor with the lowest
run hours will start first.
3. If all compressors are waiting to start (Anti-recycle
timers have not timed out), the micro will assign the
lead to the compressor with the shortest anti-recycle
time in a an effort to provide cooling quickly.
4. If the lead compressor is locked out, faulted and
waiting to restart, SYS switch on the microboard
is off, or a run permissive is keeping an individual
system from running, the lag compressor is swapped
to the lead. This is true regardless of whether the
lag compressor is ON or OFF.
MANUAL Lead/Lag selection will be automatically
overridden by the micro to allow the lag compressor to
automatically become the lead anytime the selected lead
compressor shuts down due to a lock-out, lead system
faults and is waiting to restart, lead switch on the micro
board is in the OFF position, or if a run permissive is
keeping the lead of the system off. Automatic switchover
in MANUAL mode is provided to try to maintain chilled
liquid temperature as close to setpoint as possible.
8
Summary of Contents for YCAS 0138EB
Page 50: ...50 JOHNSON CONTROLS This page intentionally left blank...
Page 61: ...61 JOHNSON CONTROLS FORM 201 18 NM7 This page intentionally left blank 7...
Page 70: ...70 JOHNSON CONTROLS Technical Data FIG 22A CONTROL PANEL COMPONENT LOCATIONS...
Page 71: ...71 JOHNSON CONTROLS FORM 201 18 NM7 LD03280 FIG 22B POWER PANEL COMPONENT LOCATION 7...
Page 72: ...72 JOHNSON CONTROLS Technical Data LEGEND LD03281...
Page 73: ...73 JOHNSON CONTROLS FORM 201 18 NM7 LD03282 LD03283 LD03284 7...
Page 74: ...74 JOHNSON CONTROLS Technical Data CONNECTION DIAGRAM SYSTEM WIRING LD06256 LD03231 LD03232...
Page 75: ...75 JOHNSON CONTROLS FORM 201 18 NM7 COMPRESSOR TERMINAL BOX LD03233 7...
Page 76: ...76 JOHNSON CONTROLS LD03285 Technical Data...
Page 77: ...77 JOHNSON CONTROLS FORM 201 18 NM7 3 4 5 6 3 4 5 6 7 8 5 6 3 4 7 8 9 10 LD06840A 7...
Page 181: ...181 JOHNSON CONTROLS FORM 201 18 NM7 NOTES...
Page 182: ...182 JOHNSON CONTROLS This page intentionally left blank...
Page 183: ...183 JOHNSON CONTROLS FORM 201 18 NM7 This page intentionally left blank...