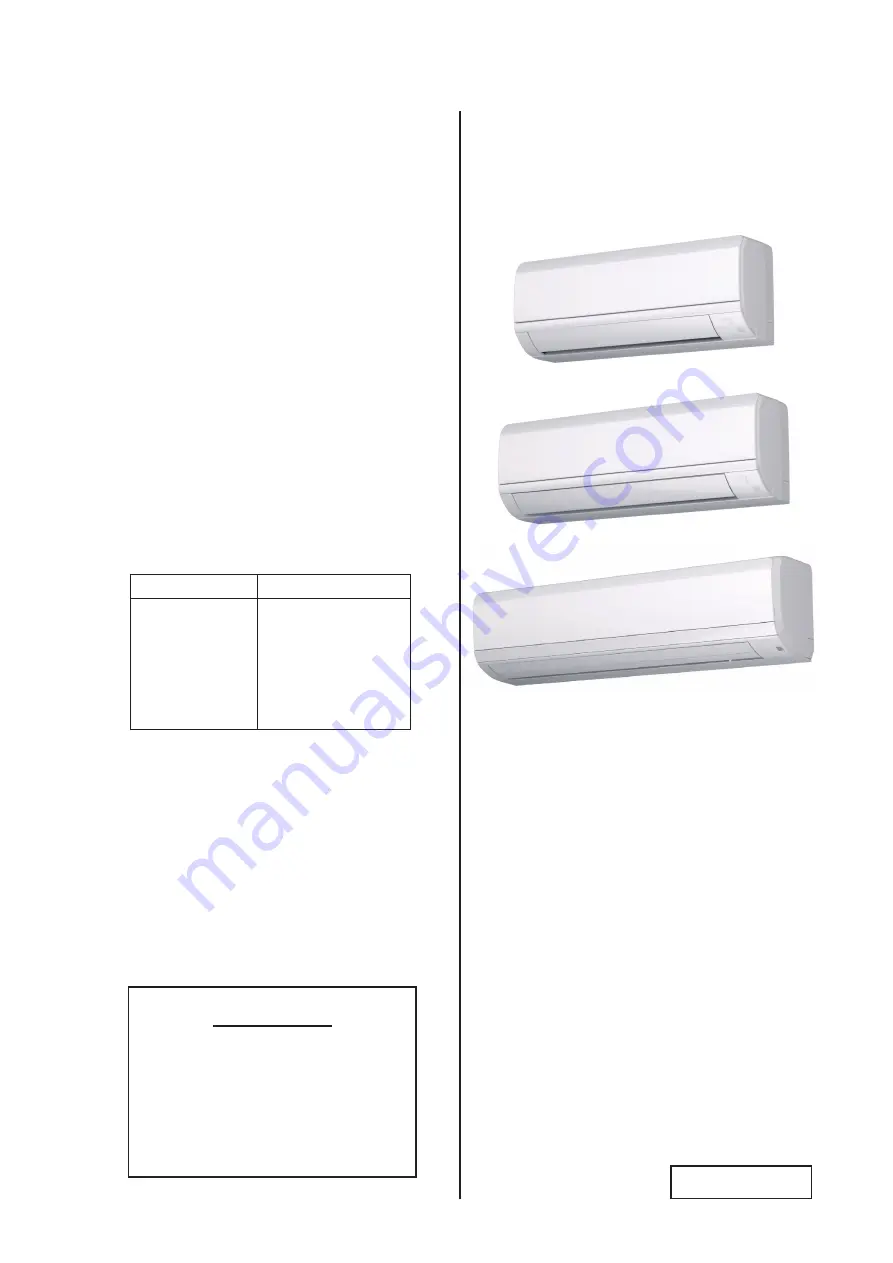
P5417090
Installation
and
Maintenance
Manual
INVERTER-DRIVEN
MULTI-SPLIT SYSTEM
HEAT PUMP
AIR CONDITIONERS
Type
Model
Wall Mount
TIWM006B22S
TIWM008B22S
TIWM012B22S
TIWM015B22S
TIWM018B22S
TIWM024B22S
TIWM030B22S
IMPORTANT:
READ AND UNDERSTAND
THIS MANUAL BEFORE
INSTALLING THIS HEAT
PUMP AIR CONDITIONER.
KEEP THIS MANUAL FOR
FUTURE REFERENCE.
Summary of Contents for TIWM006B22S
Page 2: ......
Page 49: ......
Page 50: ...2018 Johnson Controls Inc P5417090 Code No LIT 12013130 Issued September 2018...