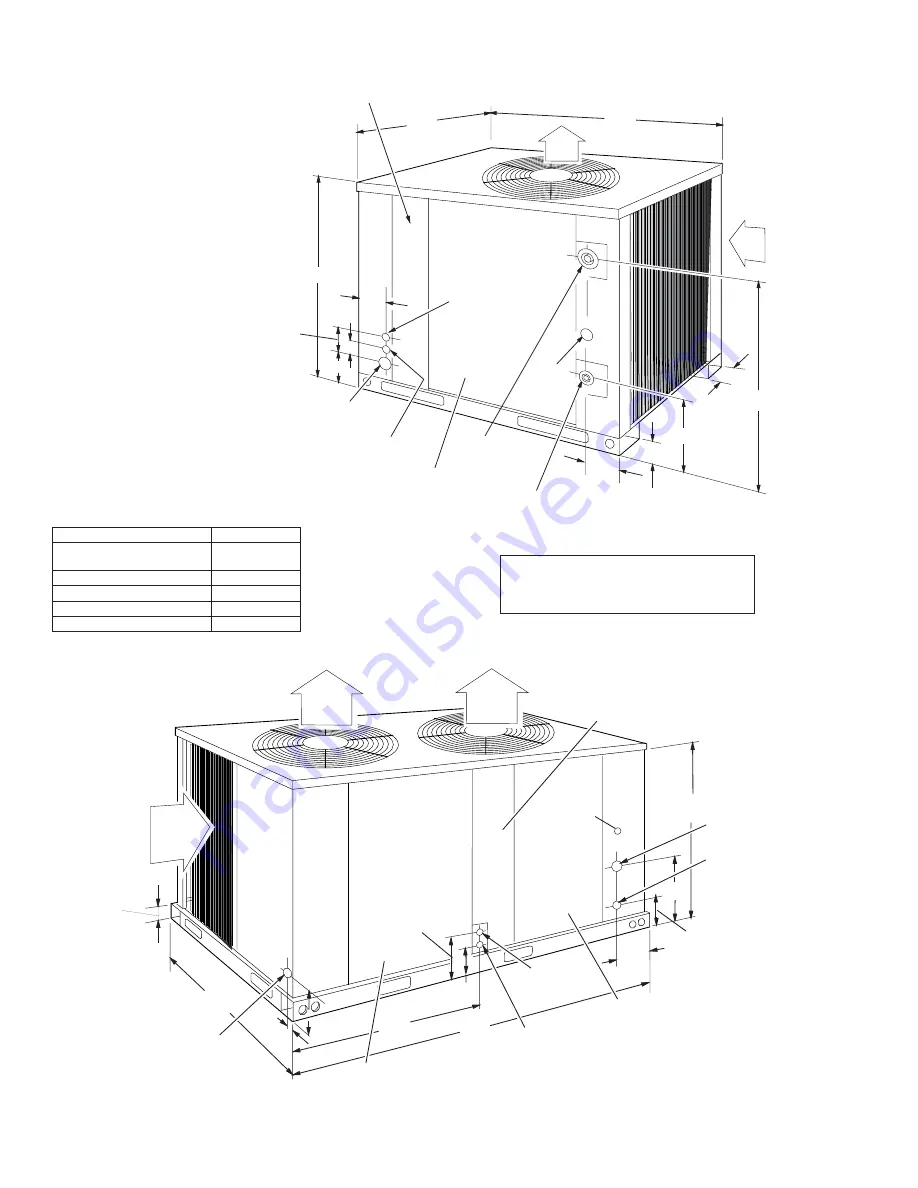
035-15406-002-A-0504
6
Unitary Products Group
FIG. 4 - UNIT DIMENSIONS AND CLEARANCES
All dimensions are in millimeters and inches,
unless otherwise specified. They are subject
to change without notice. Certified
dimensions will be provided upon request.
AIR
OUT
AIR
IN
(117)
25-3/4
10-1/8
2-1/2
4-1/2
GUAGE
LINE
ACCESS
(28.6) 1-1/8" OD
SUCTION LINE
(12.7) 1/2" OD
LIQUID LINE
COMPRESSOR AND
CONDENSER FAN MOTOR
ACCESS
(22.2) 7/8: KNOCKOUT
ACCESSORY WIRING
ENTRY
(35) 1-3/8" DIA.
POWER WIRING
ENTRY
(22.2) 7/8" DIA.
CONTROL WIRING
ENTRY
32-1/2
5
CONTROL BOX
ACCESS
31-3/4
(1086)
(806)
42-3/4
4-5/8
(654)
(257)
(64)
(114)
(127)5
(50)2
(105)
4-1/8
(127)
(826)
AIR
OUT
AIR
IN
AIR
OUT
(70)
2-3/4
(812)
32
(57)
2-1/4
(825)
32-1/2
(1781)
70-1/2
(222)
8-3/4
(136)
5-3/8
CONTROL
B
OX
ACCESS
GAUGE
LINE
ACCESS
(990)
39
(28.6)
1-1/8 O
D
SUCTION LINE
(15.8)
5/8 O
D
LIQUI
D
LINE
(400)
15-3/4
(22.2) 7/8
D
IA
CONTROL WIRING
ENTRY
COM
P
RESSOR AN
D
CON
D
ENSER FAN MOTOR
ACCESS
(34.9) 1-3/8
D
IA.
P
OWER WIRING
ENTRY
(171)
6-3/4
CON
D
ENSER FAN MOTOR
ACCES
(22.2) 7/8" KNOCKOUT
ACCESSORY WIRING
ENTRY
(197)
.7-3/4
CLEARANCES (in. / mm)
Overhead (Top)
1
120" / 3048
Front
(Piping and Access Panels)
30" / 762
Left Side
24" / 610
Right Side
24" / 610
Rear
24" / 610
Bottom
2
0" / 0
1
Units must be installed outdoors. Overhanging structures or
shrubs should not obstruct condenser air discharge.
2
Adequate snow clearance must be provided if winter
operation is expected.