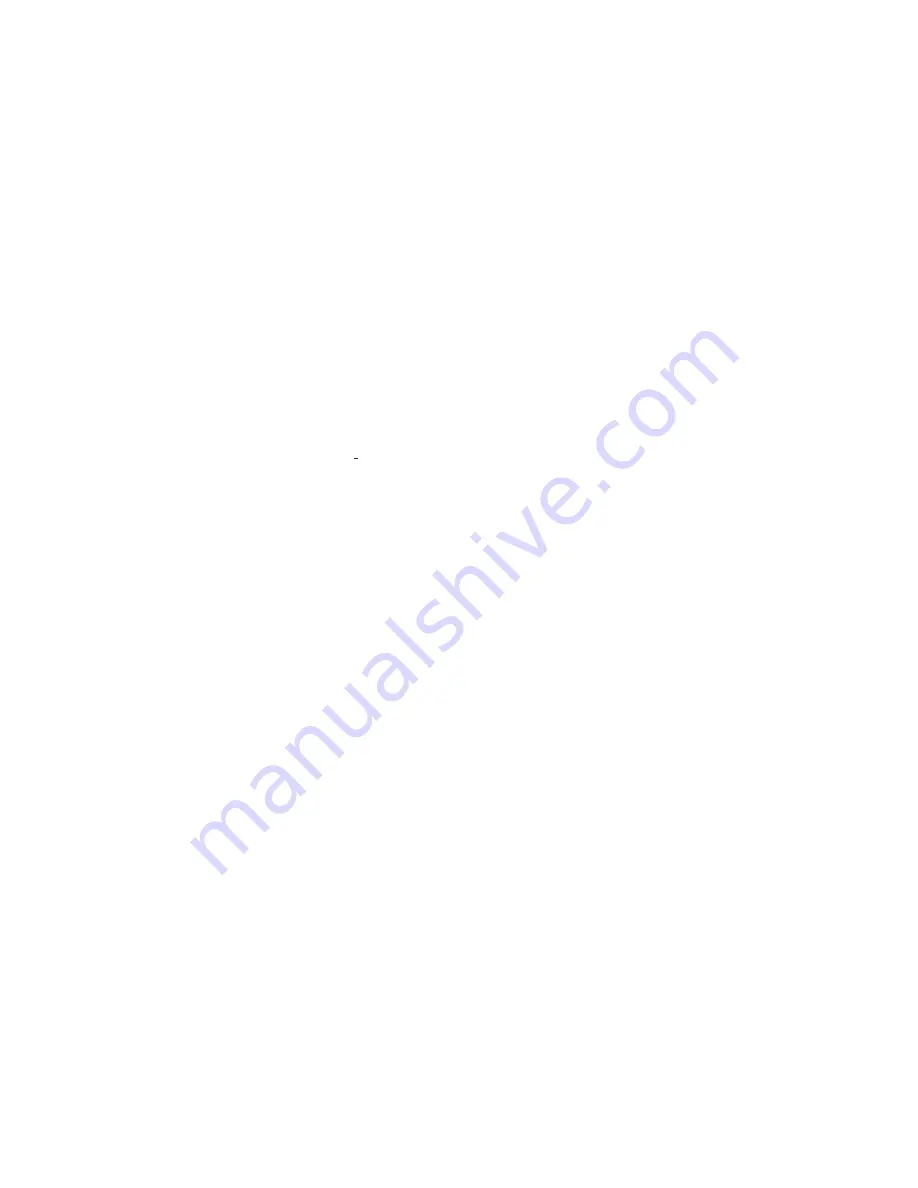
REFRIGERANT PIPING
GENERAL GUIDELINES
Many service problems can be avoided by taking adequate
precautions to provide an internally clean and dry system and
by using procedures and materials that conform with estab-
lished standards.
Use hard drawn copper tubing where no appreciable amount of
bending around pipes or other obstructions is necessary. Use
long radius ells wherever possible with one exception—short
radius ells for the traps in all suction risers. If soft copper is
used, care should be taken to avoid sharp bends which may
cause a restriction.
Pack fiber glass insulation and a sealing material such as Per-
magum around refrigerant lines where they penetrate a wall to
reduce vibrations and to retain some flexibility.
Support all refrigerant lines at minimum intervals with suitable
hangers, brackets or clamps.
Braze all copper to copper joints with Silfos-5 or equivalent
brazing material. Do not use soft solder.
Insulate all suction lines with a minimum of 1/2" (12mm) AR-
MAFLEX or equal. Liquid lines exposed to direct sunlight
and/or high temperatures must also be insulated.
Never solder suction and liquid lines together. They can be
taped together for convenience and support purposes, but they
must be completely insulated from each other.
A filter-drier MUST be installed in the liquid line of every system
to prevent dirt and moisture from damaging the system. A
properly-sized filter-drier is shipped with each condensing unit
for field installation near the evaporator coil.
NOTE: Installing a filter-drier does not eliminate the need for
the proper evacuation of a system before it is
charged.
A moisture indicating sight-glass may be field installed in the
liquid line(s) between the filter-drier and the evaporator coil.
The moisture indicating sight-glass can be used to check for
excess moisture in the system or used as a visual means to
verify refrigerant charge.
The filter-drier and is taped to the top of the compressor.
LINE SIZING
When sizing refrigerant lines for a split-system air conditioner,
check the following:
1. Suction line pressure drop due to friction,
2. Liquid line pressure drop due to friction,
3. Suction line velocity for oil return, and
4. Liquid line pressure drop due to static head.
NOTE: Never base refrigerant line sizes on the OD of the suc-
tion and liquid connections on the unit.
Tables 4 and 5 list friction losses for both the suction and liquid
lines on the system. Table 6 shows the amount of refrigerant
charge required per foot of refrigerant line.
When the evaporator coil is below the condensing unit, the suc-
tion line must be sized for both pressure drop and for oil return.
For certain piping arrangements, different suction line sizes
may have to be used. The velocity of the suction gas must al-
ways be great enough to carry oil back to the compressor.
When the condensing unit is below the evaporator coil, the liq-
uid line must be designed for the pressure drop due to both fric-
tion loss and vertical rise. If the total pressure drop exceeds 40
psig (278 kPa), some refrigerant may flash before it reaches
the thermal expansion valve. This flashing will not only cause
erratic valve operation and poor system performance, but
could also damage the expansion valve.
SERVICE VALVES
These condensing units have service valves on both the com-
pressor suction connection and the liquid line leaving the con-
denser coil.
The liquid and suction line service valves are shipped from the
factory front-seated and closed with the valve stem in the maxi-
mum clockwise position.
Both of the service valves have a 1/4" (6mm) male flare access
port for evacuating, charging and pressure checking the sys-
tem.
WARNING: Never remove a cap from an access port unless
the valve is fully back-seated with its valve stem in
the maximum counter-clockwise position because
the refrigerant charge will be lost. ALWAYS USE
A REFRIGERATION VALVE WRENCH TO OPEN
AND CLOSE THESE SERVICE VALVES.
035-15406-002-A-0504
Unitary Products Group
7