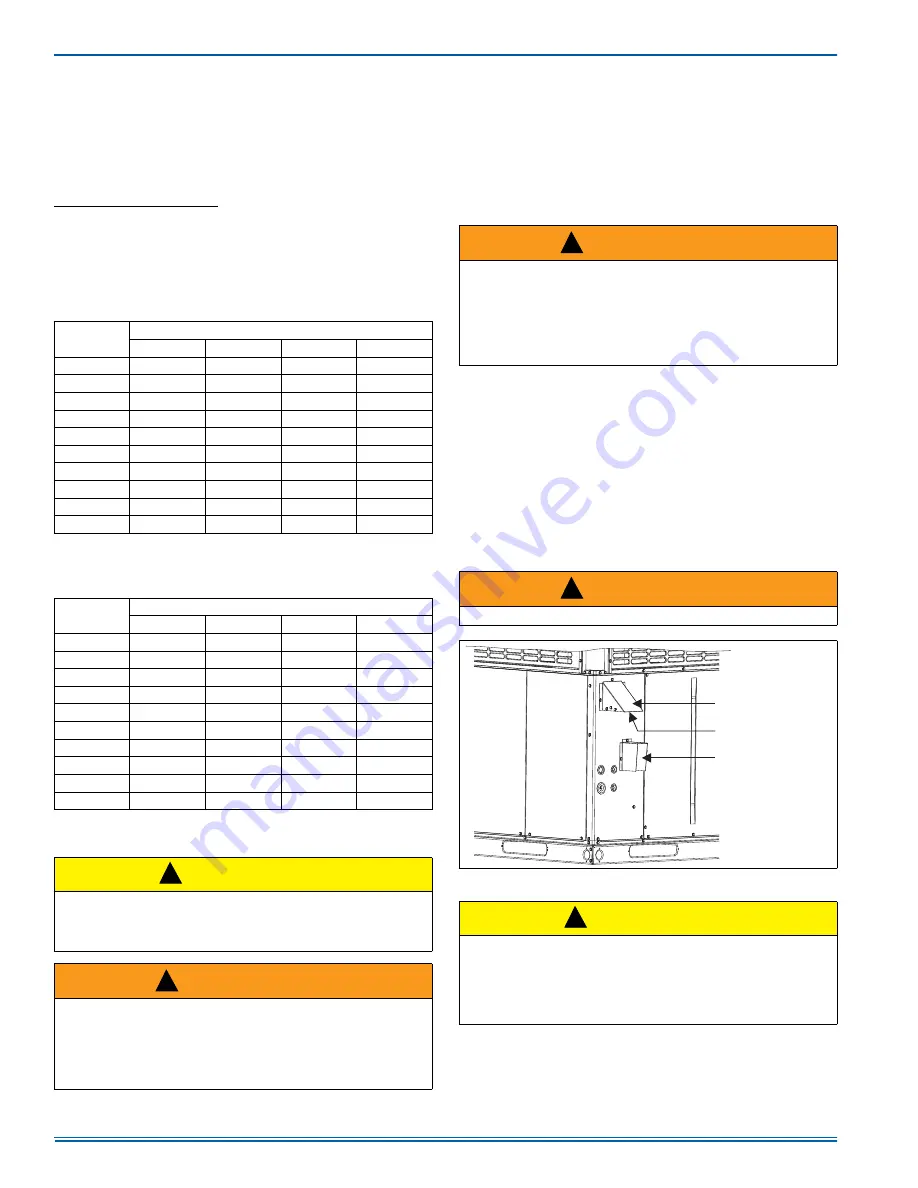
5285473-UIM-E-1217
10
Johnson Controls Unitary Products
GAS CONNECTION
The gas supply line should be routed through the 1-5/8” hole located on
the right side of the unit. See Figure 3 for the location. The unit is sup-
plied with a rubber grommet that fits in this hole and is used to seal
around the gas pipe. THIS GROMMET MUST BE INSTALLED IN
ORDER TO PREVENT LEAKAGE OF AIR AND WATER INTO THE
HEATING/CONTROLS COMPARTMENT.
Gas piping requirements:
1.
Install a drip leg and a ground joint union in the gas piping.
2.
Install a manual shut-off valve outside of the unit if required by local
codes.
3.
Use wrought iron or steel pipe for all gas lines. Apply pipe thread
sealant sparingly to male threads only.
4.
Clean all piping of dirt and scale by hammering on the outside of
the pipe and blowing out the loose dirt and scale. Before initial start-
up, be sure that all of the gas lines external to the unit have been
purged of air.
5.
Ensure that the gas supply is a separate line and is installed in
accordance with all applicable safety codes. After the gas connec-
tions have been completed, open the main shut-off valve admitting
normal gas pressure to the gas valve. Check all joints for leaks with
soap solution or other material suitable for the purpose. NEVER
USE AN OPEN FLAME to check for leaks.
6.
Pressure tests in excess of 1/2 psi (3.48 kPa): During the gas sup-
ply piping system pressure test, ensure that the unit and its equip-
ment shutoff valve is disconnected from the gas supply system.
7.
Pressure tests equal to or less than 1/2 psig (3.48 kPa): During the
gas supply piping system pressure test, verify that the unit is iso-
lated from the gas supply piping system by closing its individual
manual shut-off valve.
FLUE VENT AND AIR INTAKE HOOD
The flue vent hood and air intake hoods are shipped loose. These hoods
must be installed to assure proper unit operation. The hoods must be fas-
tened to the outside of the side gas control/electrical compartment with
the screws provided. See Figure 8.
Table 7:
Natural Gas Pipe Sizing Chart
1
1. Maximum capacity of pipe in cubic feet of gas per hour (based upon a pres-
sure drop of 0.3 inch water column and 0.6 specific gravity gas).
Length
In Feet
Nominal Inches Iron Pipe Size
1/2”
3/4”
1”
1-1/4”
10
132
278
520
1,050
20
92
190
350
730
30
73
152
285
590
40
63
130
245
500
50
56
115
215
440
60
50
105
195
400
70
46
96
180
370
80
43
90
170
350
90
40
84
160
320
100
38
79
150
305
Table 8:
Propane (LP) Gas Pipe Sizing Chart
1
1. Maximum capacity of pipe in thousands of BTU per hour (based upon a
pressure drop of 0.5 inch water column).
Length
In Feet
Nominal Inches Iron Pipe Size
1/2”
3/4”
1”
1-1/4”
10
275
567
1071
2,205
20
189
393
732
1496
30
152
315
590
1212
40
129
267
504
1039
50
114
237
448
913
60
103
217
409
834
70
96
196
378
771
80
89
185
346
724
90
83
173
322
677
100
78
162
307
630
CAUTION
If flexible stainless steel tubing is allowed by the authority having
jurisdiction, wrought iron or steel pipe must be installed at the gas
valve and extend a minimum of two (2) inches outside of the unit cas-
ing.
WARNING
Natural gas may contain some propane. Propane being an excellent
solvent, will quickly dissolve white lead or most standard commercial
compounds. Therefore, a special pipe thread sealant must be
applied when wrought iron or steel pipe is used. Shellac base com-
pounds such as gaskoloc or stalastic, and compounds such as Rec-
torseal # 5, Clyde’s or John Crane may be used.
!
!
WARNING
FIRE OR EXPLOSION HAZARD
Failure to follow the safety warning exactly could result in serious
injury, death or property damage.
Never test for gas leaks with an open flame. Use a commercially
available soap solution made specifically for the detection of leaks to
check all connections. A fire or explosion may result causing property
damage, personal injury or loss of life.
WARNING
Flue hood surfaces may be hot.
FIGURE 8:
Flue Vent Outlet Air Hood
CAUTION
The flue exhaust hood must be properly installed within the recom-
mended clearances. Further communications and action must be
given to the home or building owner(s) to eliminate any unauthorized
human contact around this area during the heating cycle. Flue hood
surfaces and the immediate area reach high temperatures during the
heating cycle.
!
!
AIR INTAKE HOOD
AIR INTAKE SCREEN
EXHAUST HOOD
A0284-001
!