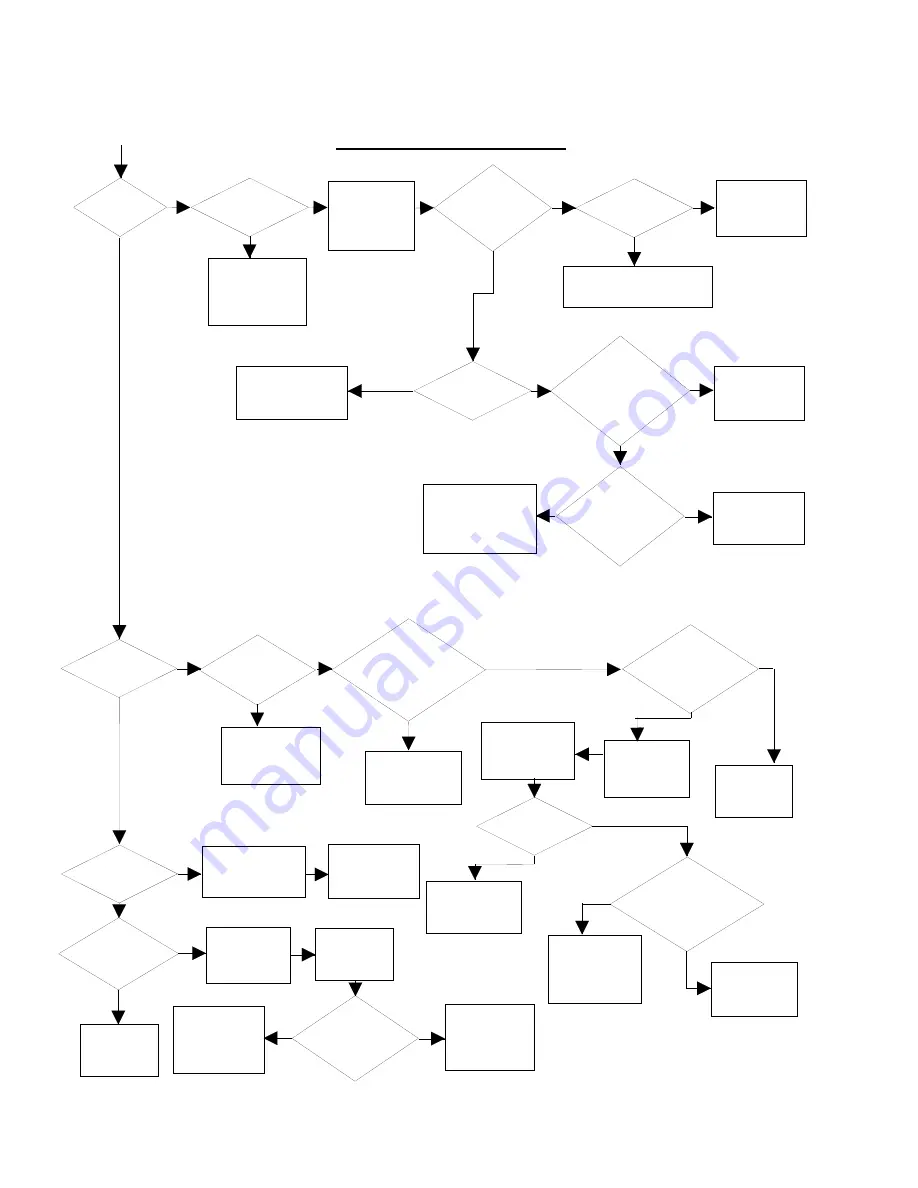
Disconnect
sensor. Deenergize system.
Connect ohmmeter across sensor
and ground. Is resistance
less than 50
ohms?
No
Yes
Turn manual knob
on gas valve to OFF
position. Connect
manometer to outlet
pressure tap.
Does main
burner light?
Restore gas supply at
source. Energize system
and check for proper
operation.
Turn manual knob on
gas valve to ON
position. Energize
system and check for
proper operation.
No
knob on gas valve
in ON position?
Purge system of air.
Energize system and
check for proper
operation.
No
Correct supply pressure. Energize
system and check for proper
operation.
No
Yes
Yes
Yes
Replace gas valve.
Energize system and
check for proper
operation.
Replace leads.
Energize system and
check for proper
operation.
Reset rollout switch.
Check wiring. If OK,
replace module. Energize
system and check for
proper operation.
NOTE: Diagnostic indicator may
indicate one flash for "no
flame" condition. Inducer
and circulator blower will
be on continuously.
NOTE: Reset rollout switich.
No
Yes
Yes
Yes
No
No
No
Yes
No
No
Yes
NOTE: Diagnostic indicator may
indicate one flash for "no
flame" condition. Inducer
and circulator blower will
be on continuously.
No
Yes
Yes
Yes
No
No
Yes
No
Yes
No
Yes
Reconnect sensor
Disconnect electric
power to system at
main fuse or circuit
breaker.
Connect voltmeter
from control 120 volt
hot line terminal
to ground.
Reposition flame
probe to achieve
1.0 m amp or make
flame current.
Check wiring. If OK,
replace module.
Energize system and
check for proper
operation.
Igniter remains heated
(bright red) with main
burner flame present.
Check wiring. If OK,
replace module.
Energize and check
for proper operation.
Reverse 120 V hot
and neutral line wires.
Less than 30 V
Unplug circulator
blower wires and
connect voltmeter
across terminals.
Disconnect electric
power to system at
main fuse or circuit
breaker.
System is
functioning
properly.
Check wiring. If OK,
replace module.
Energize the system
and check for proper
operation.
Replace circulator
blower connection.
Energize system at
main fuse or circuit
breaker.
NOTE:
To measure flame current,
disconnect sensor lead.
Connect microamp meter
in series with lead and sensor.
NOTE:
Flame probe
must be in flame
to sense.
Remove flame sensor.
Clean surface of flame
rod with fine steel wool
then reinstall.
Replace sensor.
Energize system and
check for proper
operation.
Continued
Is manual
MAIN BURNER IGNITION
Is gas
available at source?
Is outlet
pressure at nameplate
rating?
Disconnect
leads at gas valve.
Energize system. Is 25 V
present across MV & MV
module terminals after
warmup?
igniter
Turn
manual knob
on gas valve to ON.
Energize system. Is
outlet pressure
detected?
With
system energized
is 25 V present across
MV & MV terminals of
module after igniter
warm-up?
Does flame
sense probe have
carbon or dust
build-up?
Is
ground wire
connected to furnace &
control box GND term.
wired to burner
ground?
Does
main burner
remain lit?
Correct ground
wiring.
Energize
the module and
check for 120 v.
Igniter
turns off with
main burner flame
present?
Is
flame probe
located properly in flame?
Proper location will provide
adequate flame
current.
Energize
the module and
check for 120 v across
terminals circulator
heat & Cir
neutral?
Does
the circulator
blower energize at heat
speed within 1 min?
Main burner
on.
650.69-N3
18
Unitary Products Group