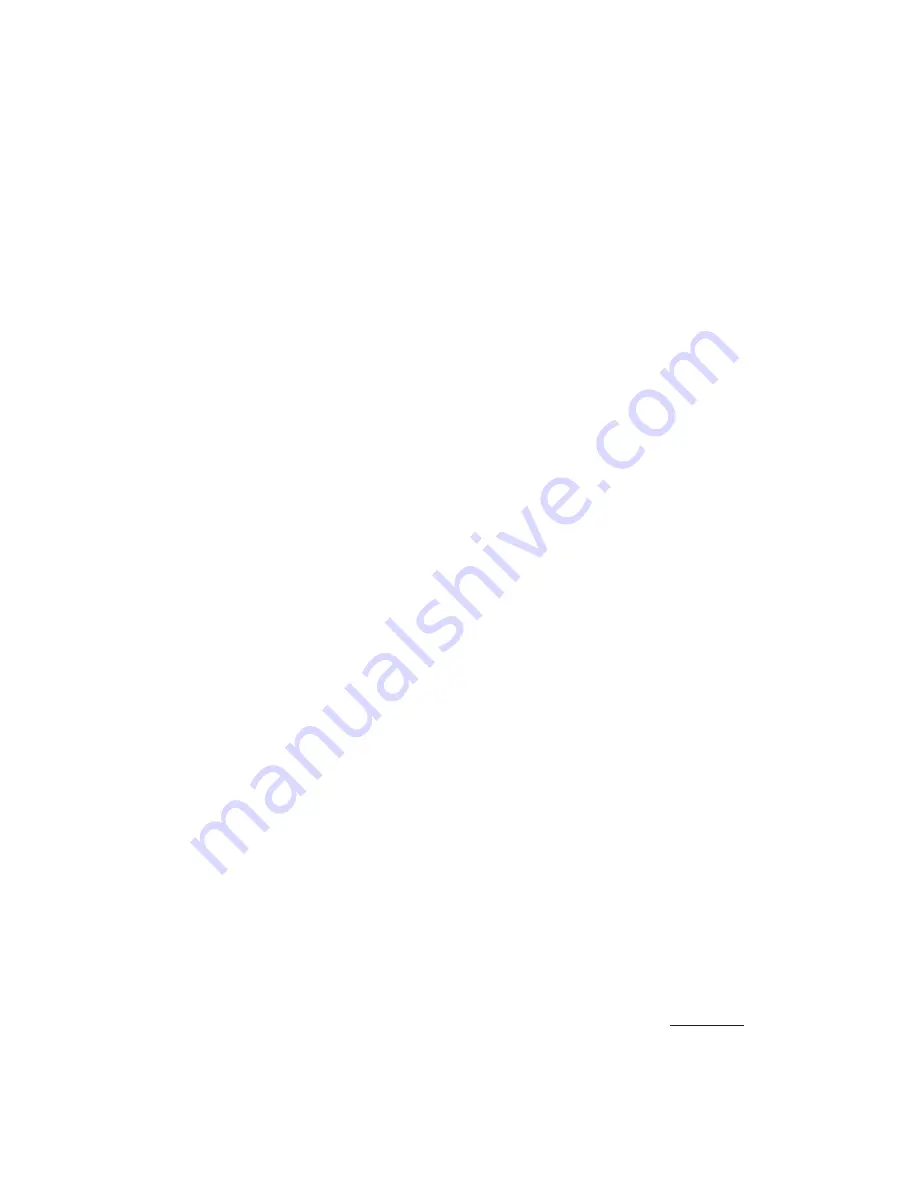
FORM 201.10-NM4
69
YORK INTERNATIONAL
Signals routed through the I/O Expansion Board include
Discharge Temperature, Current Transformer outputs, and
Oil Temperature. Mixed Water Temperature Sensor Out-
puts on YDAS models also are routed through this board.
Relay Output Boards
One Relay Output Board per system is used to operate
the motor contactors/starters, solenoid valves and heat-
ers which control system operation.
The relay boards are located in the logic section of the
control panel(s). The boards convert 0-12VDC logic lev-
els outputs from the Microprocessor Board to 115VAC
levels used by the contactors, valves, etc.
The common side of all relays on the Relay Output
Board is connected to +12VDC REG. The open collec-
tor outputs of the Microprocessor Board energize the
DC relays or triacs by pulling the other side of the relay
coil to 0VDC. When not energized, both sides of the
relay coils or triacs will be at +12VDC potential. Triacs
are used to control load and unload slide valve sole-
noids as well as liquid line solenoid valves.
1.6 CURRENT TRANSFORMERS (C.T.)
C.T.s on each of the 3 phases of the power wiring of
each compressor motor send AC signals proportional
to motor current to the Power Supply Board which rec-
tifies and filters the signals to variable DC Voltage (ana-
log). These analog levels are then fed to the Micropro-
cessor Board via the I/O Expansion Board to allow it to
monitor motor currents for low current, high current,
unbalanced current, and single phasing.
1.7 EMS/BAS CONNECTIONS
The Microprocessor system can accept remote signals
to Start/Stop the chiller, adjust maximum allowable run-
ning current for each compressor, and adjust the chilled
liquid leaving temperature setpoint. These functions can
easily be controlled by connecting user supplied dry
contacts to the customer terminals in the control panel.
In addition, Alarm Contacts are provided to remotely
signal a fault with the chiller.
Remote Start/Stop
Remote Start/Stop can be accomplished using a time
clock, manual contact or other dry contact in series with
the flow switch (Terminals 13 & 14 of TB4) connected to
terminals in the logic section of the control panel. The con-
tacts must be closed to allow the chiller to run. Any time
the contact opens, the chiller will shut down and the NO
RUN PERM message will be displayed. The location of
the flow switch (Start/Stop) connections is shown in Sec-
tion 1.9.
NOTE: Never bypass a flow switch. This will cause
damage to the chiller and void any warranties.
NOTE: Wiring from remote dry contacts (for stop/start
reset functions) should not exceed 25 ft. and
should be run in grounded conduit that does
not carry any wiring other than control wiring or
in screened cable. If an inductive device (relay,
contactor) is supplying these contacts, the coil
of the device must be suppressed with a sup-
pressor YORK Part Number 031-00808-000 (60
Hz models) or a standard RC suppressor (50
Hz models) across the inductive coil.
Remote Current Reset
The maximum allowable running current for each com-
pressor can be adjusted remotely to a lower value us-
ing repeated timed closure of dry contacts connected
to Terminals 13 & 16 of TB4 (see Section 1.9) in the
logic section of the control panel. The duration of the
contact closure will determine the amount of adjustment.
Generally, this input is used for purposes of demand
limiting and operates as follows:
Closing the input contact for a defined period of time al-
lows reset of the % Current Limit downward. Contact clo-
sure of 1-18 seconds will allow % Current Limiting to be
adjusted downward from 115% by a maximum of 85%,
i.e. to a minimum value of 30% FLA. EMS Current Limit-
ing operates independently of the Programmable Current
Limiting (See Section 8.2,). The micro will always look at
the two Current Limit Setpoints and choose the lower as
the controlling value, whenever Remote Current Limiting
is utilized. Contact closures of less than 1 second will be
ignored. A closure of 18 seconds is the maximum allow-
able closure and provides a Current Limit reduction of 85%.
The required contact closure can be calculated as follows:
1. Subtract the desired Current Limit % FLA from 115%
to calculate the required Offset %.
2. Convert the Offset % to a decimal equivalent by di-
viding by 100%.
3. Calculate the Pulse Width (PW) in seconds required
using the formula: PW seconds = (Offset x 20) + 1
For example, if 75% FLA is the Desired Current Limit %:
1. Offset % = 115% 75% = 40%
2. Offset = 40% / 100% = 0.4
3. PW = (0.4 x 20) + 1 =
9 seconds
To maintain a given offset, the contact closure signal must
be regularly repeated at not more than 30 minute intervals
but not less than 30 seconds from the end of each PWM
signal. After 30 minutes, if no refresh is provided, the
setpoint will change back to its original value.