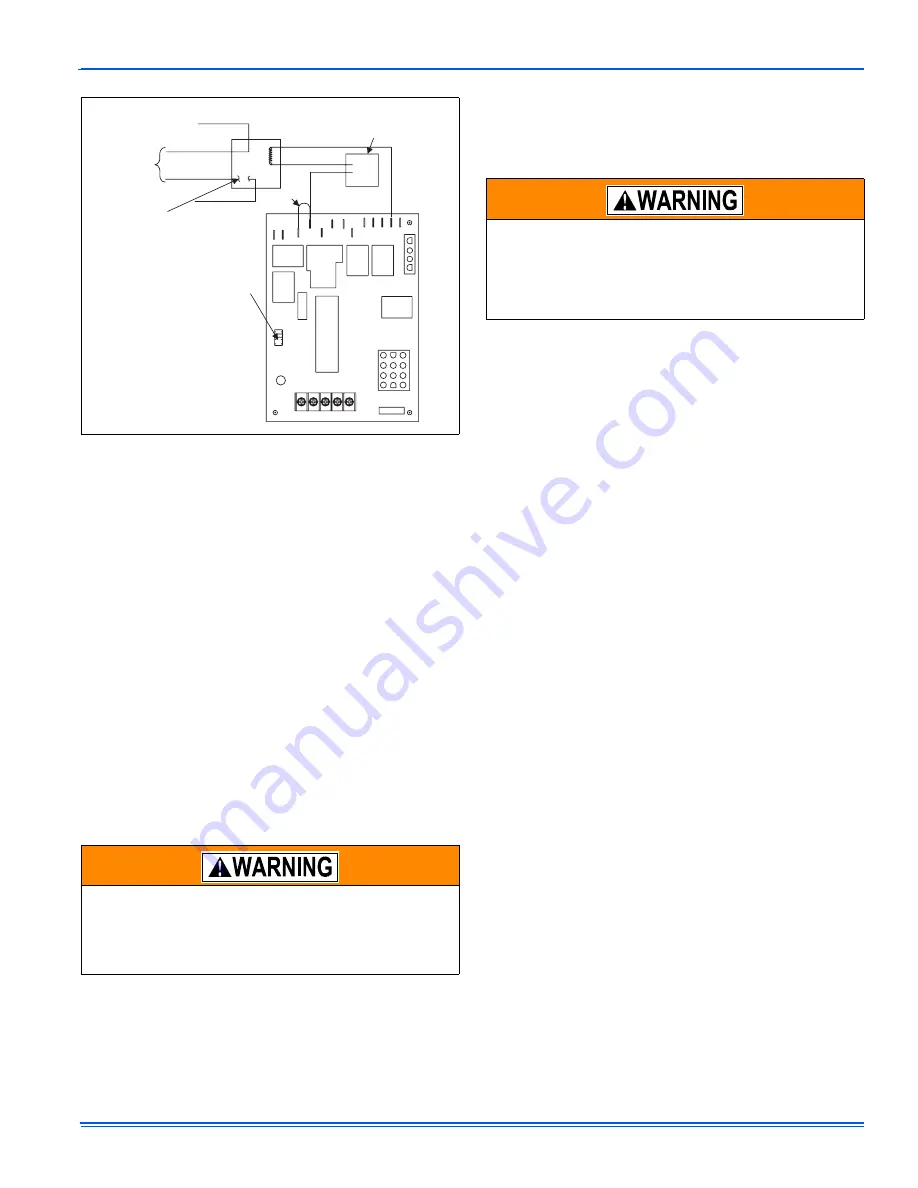
106306-UUM-A-0205
Unitary Products Group
7
If the flame is not detected within 7 seconds of the gas valve opening,
the gas valve is shut off and a retry operation begins. If the flame is lost
for 2 seconds during the 10-second stabilization period, the gas valve is
shut off and a retry operation begins. During a retry operation, the vent
motor starts a 15 second inter-purge and the igniter warm-up time is
extended to 27 seconds. If the flame is established for more than 10
seconds after ignition during a retry, the control will clear the ignition
attempt (retry) counter. If three retries occur during a call for heat, the
furnace will shut down for one hour. If at the end of the one hour shut
down there is a call for heat, the furnace will initiate a normal start cycle.
If the problem has not been corrected the furnace will again lockout
after three retries.
A momentary loss of gas supply, flame blowout, or a faulty flame probe
circuit will result in a disruption in the flame and be sensed within 1.0
seconds. The gas valve will de-energize and the control will begin a
recycle operation. A normal ignition sequence will begin after a 15 sec-
ond inter-purge. If during the five recycles the gas supply does not
return, or the fault condition is not corrected the ignition control will lock-
out for 60 minutes.
During burner operation, a momentary loss of power for 50 milliseconds
or longer will de-energize the gas valve. When the power is restored,
the gas valve will remain de-energized and the ignition sequence will
immediately restart.
Hot Surface Ignition System
TROUBLESHOOTING
The following visual checks should be made before troubleshooting:
1.
Check to see that the power to the furnace and the ignition control
module is ON.
2.
The manual shut-off valves in the gas line to the furnace must be
open.
3.
Make sure all wiring connections are secure.
4.
Review the sequence of operation. Start the system by setting the
thermostat above the room temperature. Observe the system’s
response. Then use the troubleshooting section in this manual to
check the system’s operation.
FURNACE CONTROL DIAGNOSTICS
The furnace has built-in, self-diagnostic capability. If a system problem
occurs, a blinking LED shows a fault code. The LED can flash red,
green or amber to indicate various conditions. It is located behind a
clear view port in the blower compartment door.
The control continuously monitors its own operation and the operation
of the system. If a failure occurs, the LED will indicate the failure code. If
the failure is internal to the control, the light will stay on continuously. In
this case, the entire control should be replaced, as the control is not
field repairable.
Flash sequence codes 1 through 10 are as follows: LED will turn “on”
for 1/4 second and “off” for 1/4 second. This pattern will be repeated the
number of times equal to the code. For example, six “on” flashes equals
a number 6 fault code. All flash code sequences are broken by a 2 sec-
ond “off” period.
SLOW GREEN FLASH:
Normal operation.
SLOW AMBER FLASH:
Normal operation with call for heat.
RAPID RED FLASH:
Twinning error, incorrect 24V phasing. Check
twinning wiring.
RAPID AMBER FLASH:
Flame sense current is below 1.5 microamps.
Check and clean flame sensor. Check for proper gas flow.
1 RED FLASH:
This indicates that flame was sensed when there was
not a call for heat. With this fault code the control will turn on both the
inducer motor and supply air blower. A gas valve that leaks through or
is slow closing would typically cause this fault.
2 RED FLASHES:
This indicates that the normally open pressure
switch contacts are stuck in the closed position. The control confirms
these contacts are open at the beginning of each heat cycle. This would
indicate a faulty pressure switch or miswiring.
3 RED FLASHES:
This indicates the normally open pressure switch
contact did not close after the inducer was energized. This could be
caused by a number of problems: faulty inducer, blocked vent pipe, bro-
ken pressure switch hose or faulty pressure switch.
4 RED FLASHES:
This indicates that a primary or auxiliary limit switch
has opened its normally closed contacts. With this fault code the control
will operate the supply air blower and inducer. This condition may be
caused by: dirty filter, improperly sized duct system, incorrect blower
speed setting, incorrect firing rate or faulty blower motor.
5 RED FLASHES:
This fault is indicated if the normally closed contacts
in the rollout switch opens. The rollout control is manually reset. If it has
opened, check for proper combustion air, proper inducer operation, and
primary heat exchanger failure or burner problem. Be sure to reset the
switch after correcting the failure condition.
6 RED FLASHES:
This indicates that after the unit was operating, the
pressure switch opened 4 times during the call for heat. If the main
blower is in a “Delay on” mode it will complete it, and any subsequent
delay off period. The furnace will lock out for one hour and then restart.
FIGURE 10:
Typical Heat/Cool Speed Tap Connections
HOT SURFACE IGNITION SYSTEM
Do not attempt to light this furnace by hand (with a
match or any other means). There may be a potential
shock hazard from the components of the hot surface
ignition system. The furnace can only be lit automatically
by its hot surface ignition system.
FAN OFF
ADJUSTMENT
JUMPER
P
ARK
P
ARK
HI
COOL
HEA
T
EAC
L1
XFMR
HUM
NEUTRALS
Y/Y2 W
R
G
C
208/230 VAC
LINE (Hot)
208/230 VAC
280/230 VAC
TO
INDOOR
FAN
MOTOR
208/230 VAC
LINE (Hot)
COIL
DELAY ON
TIMER RELAY
(Indoor fan motor)
JUMPER
INDOOR
FAN RELAY
Never bypass pressure switch to allow furnace opera-
tion. To do so will allow furnace to operate under poten-
tially hazardous conditions.
Do not try to repair controls. Replace defective controls
with UPG Source 1 Parts.
Never adjust pressure switch to allow furnace operation.