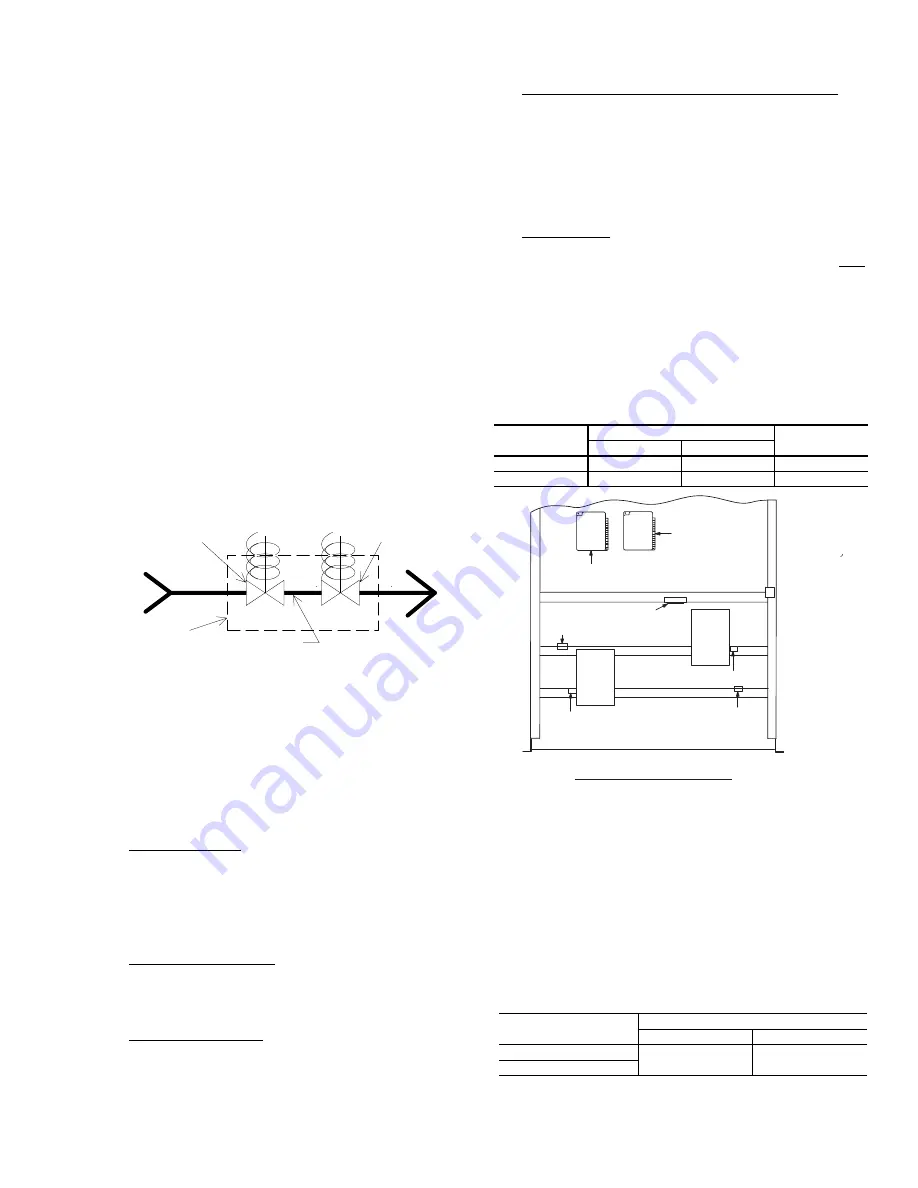
operation until 24V power is removed from the module either
at the unit or by resetting the room thermostat.
At the same time power was supplied to the “RW1”, a parallel
circuit activates “ETD” which closes the “ETD” contact after
approximately 35 seconds and energizes “K5" which closes
”K5-2" and starts the blower by energizing “3M”.
When “TH2" closes, heat relay ”RW2" is energized. The
“RW2-1" contact is closed energizing the second stage ignition
module ”IC2". “IC2" will immediately start the second stage
ignitor sparking and will open the redundant valve located
inside the second stage main gas valve ”GV2" to allow a flow
of gas to the second stage carryover tube. Only after the pilot
flame has been ignited and the presence of pilot flame detected
at “IC2" by a signal sent back through the flame sensor is
sparking terminated and the main gas valve opened.
Gas flows into each of the second stage main burners and is
ignited from the carryover tube flame.
If “IC2" fails to detect a pilot flame, it will continue to try for a
maximum of 85 seconds to ignite the pilot tube. If the pilot flame
is not detected, then ”IC2" will lock out first stage furnace
operation until 24V power is removed from the module either
at the unit or by resetting the room thermostat. Note that the
second stage furnace can operate even if first stage has locked
out.
W he n the heating cycle is complete, “TH2" opens
de-energizing the ”RW2" then “TH1" opens de-energizing
”RW1" and “ETD”, thus closing all gas valves. The blower motor
will continue to run (approximately 45 seconds after the furnace
is shut down) until “ETD” opens, de-energizing the “K5" relay
and ”3M" contactor.
SAFETY CONTROLS
The control circuit includes the following safety controls:
1. Limit Control (LS). This control is located inside the heat
exchanger compartment and is set to open at the tempera-
ture indicated in the Limit Control Setting Table. It resets
automatically. The limit switch operates when a high tem-
perature condition, caused by inadequate supply air flow
occurs, thus shutting down the ignition control and closing
the main gas valves and energizing the blower.
2. Centrifugal Switch (CS). If the draft motor should fail, the
centrifugal switch attached to the shaft of the motor
prevents the ignition controls and gas valves from being
energized.
3. Redundant Gas Valve. There are two separate gas valves
in the furnace. Each valve contains a main and a redundant
valve. The redundant valves are located upstream of the
main gas valves. Should either or both of the main gas
valves fail in the open position the redundant valves serve
as back-ups and shuts off the flow of gas.
4. Flame Sensor Rod / 100% Ignition Control Lock-Out. The
flame rods and controls are located per Proper Flame Adjust-
ment figure. If an ignition control fails to detect a signal from
the flame sensor indicating the pilot flame is properly ignited,
then the main gas valve will not open. It will continue to try and
ignite the pilot for a maximum of 85 seconds, then if the pilot
flame is not detected, the ignition control will lock out furnace
operation until 24V power is removed from the module either
at the unit or by resetting the room thermostat.
5. Rollout Switch. This switch is located above the main burn-
ers in the control compartment which in the event of a
sustained main burner rollout shuts off and locks out both
ignition controls closing both gas valves. The ignition con-
trols lock out furnace operation until 24V power is removed
from the controls either at the unit or by resetting the room
thermostat. Note the auto reset rollout switch must reset
before allowing furnace operation.
6. Auxiliary limit switch (AUX) - This control is located inside
the heat exchanger compartment and is set to open at
190
°
F. It is a manual reset switch. If AUX trips, then the
primary limit has not functioned correctly. Replace the
primary limit.
HEAT ANTICIPATOR SETPOINTS
It is important that the anticipator setpoint be correct. Too high
of a setting will result in longer heat cycles and a greater
temperature swing in the conditioned space. Reducing the
value below the correct setpoint will give shorter “ON” cycles
and may result in the lowering of the temperture within the
conditioned space.
Units
(Tons)
Capacity, MBH
Limit Control
Opens,
°
F
Input
Output
15 & 20
300
240
195
15 & 20
400
320
195
TABLE 13 - LIMIT CONTROL SETTING
GAS
VALVE
GAS MAIN
MAIN VALVE
TO MAIN
BURNER
REDUNDANT
VALVE
TO PILOT BURNER
FIG. 12 - GAS VALVE PIPING
Gas Valve
Anticipator Setpoint
1st Stage
2nd Stage
Honeywell VR8440
0.30 amp
0.11 amp
White-Rodgers 36C68
I G N . C O N T R O L # 1
I G N . C O N T R O L # 2
I G N I T O R # 1
G V 1
G A S
V A L V E
G V 2
G A S
V A L V E
I G N I T O R # 2
S E N S O R # 2
S E N S O R # 1
R O L L O U T S W
.
B U R N E R C O M P A R T M E N T
FIG 13-GAS VALVE AND CONTROLS
530.18-N6Y
Unitary Products Group
17