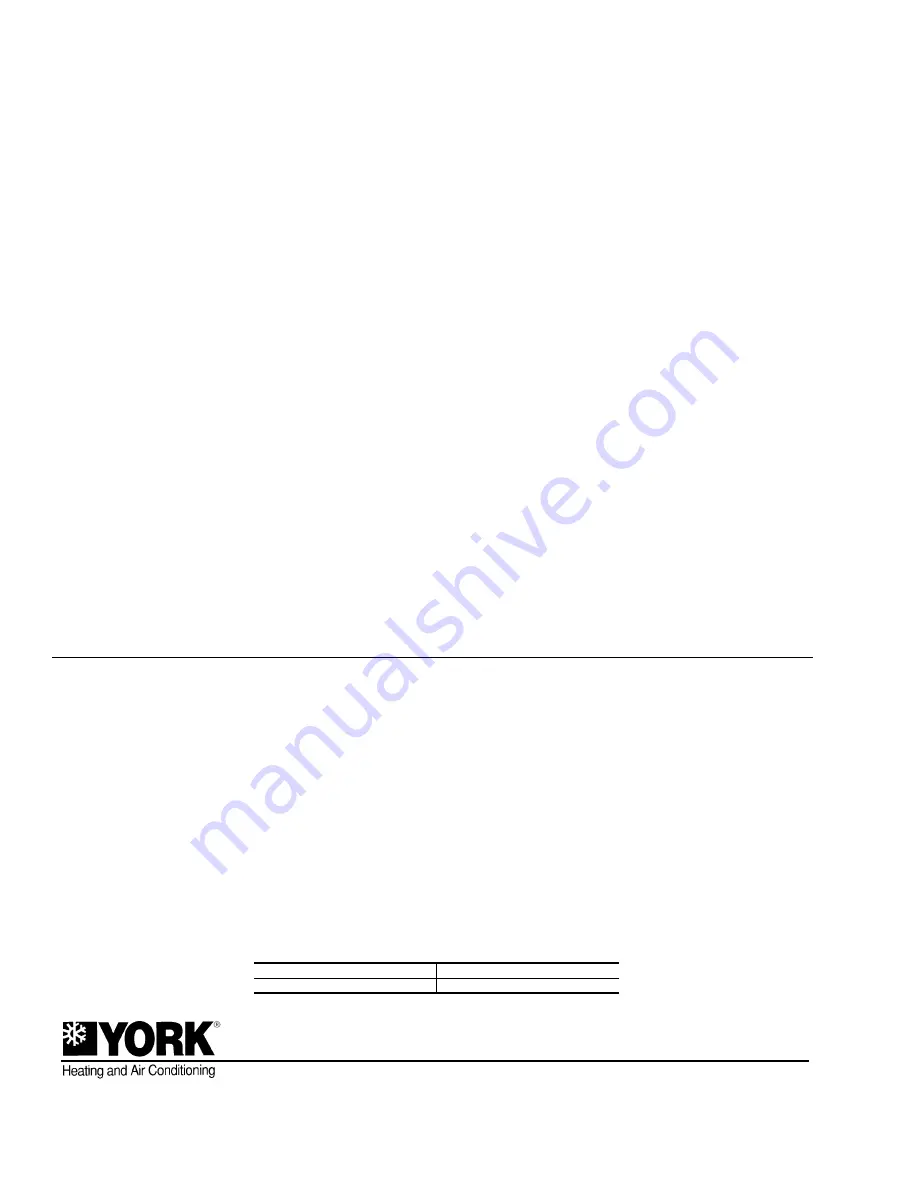
to the compressor so that eventually the oil pressure switch
opens. This requires re-setting manually at the unit.
PRE-START CHECK
Before starting the unit, the following check list should be
completed.
1. Make sure the proper clearances were considered.
2. Make sure all foreign matter has been removed from the
interior of the unit (tools, construction or shipping
materials).
3. Rotate all fans and blower wheels manually to check for free
rotation.
4. Check belt tensions and alignment.
5. Make sure all wiring connections are tight.
6. Make sure the available power supply and unit nameplate
data agree.
7. Make sure the fuse sizes and the power wire are properly
sized.
8. Make sure all controls are set at their proper set points.
9. Make sure condensate drain line is trapped per instructions
as indicated with Figure 4.
10 For shipping, the compressor hold-down nuts are
tightened, drawing the mounting feet down to the shipping
stops. After the unit is in its final position, the four hold-down
nuts must be removed to insert the rubber grommets found
in the small parts bag. Replace the hold-down nuts and
tighten until they start to compress the isolator springs and
then give them an additional half turn.
INITIAL START-UP
1. Supply power to the unit through the disconnect switch at
least 8 hours prior to starting the compressors.
2. Move the system switch on the thermostat or the status
panel to the AUTO position.
3. The proper supply air CFM should be established at this
time with an inclined manometer as outlined in this
instruction. This is an important part of the start-up
procedure since it directly affects nuisance trip-outs on unit
safety controls, condensate water blow-off from the
evaporator coil, bearing and shaft damage, noise and
vibration.
4. Lower the room thermostat to energize compressor No. 1.
5. With an ammeter, check the compressor and the supply air
blower amps to make sure they agree with the unit data
plate.
6. Lower the room thermostat to energize compressor No. 2
or load the compressor.
7. Check the compressor amps with the unit data plate.
8. After approximately 15 minutes of operation, check the
liquid line sight glasses for a proper liquid refrigerant seal
in each of the refrigerant circuit(s).
9. Next increase the setting of the room thermostat until the
heating contacts are energized.
10. Refer to the proper heating installation and operation
instruction for the correct heating sequence of operation.
11. After the unit has been operating for several minutes,
de-energize the main power and inspect all factory wiring
connections and bolted surfaces for tightness.
POST-START CHECK LIST
After the entire control circuit has been energized, check the
following:
1. Cooling system start-up.
2. Rotation of blower wheels. Adjust the air system if
necessary per the procedures as outlined in this instruction.
NOTE: If the supply air blower rotates in the wrong direction,
reverse two of the motor leads at blower motor contac-
tor 3M.
3. Operation of the outside and return air dampers as
explained under “Damper Linkage Adjustment” in this
instruction.
Code: SBY
530.25-N3Y
Unitary Products Group
P.O. Box 1592, York, Pennsylvania USA 17405-1592
Subject to change without notice. Printed in U.S.A
Copyright
•
by York International Corporation 1994. All Rights Reserved.
CAUTION: Prior to any of the following maintenance proce-
dures, shut off all electircal power to the unit to
prevent personal injury.
FILTERS
The filters must be replaced as often as necessary to assure
good air flow and filtering action.
Refer to Figure 1 for filter access location.
COILS
Do not allow dirt to accumulate on the evaporator and condenser
coil or other parts of the evaporator and condenser circuit. Clean
as often as necessary to assure good system performance. Use
a brush, vacuum cleaner attachment or other suitable means.
DRAIN PAN
The drain pan should be inspected regularly to assure proper
drainage.
LUBRICATION
The bearings for the blower shaft and the blower motor are
permanently lubricated and should not require any additional
lubrication.
BELTS
Maintain belt tension to extend belt life. Replace when signs of
failure begin to appear.
DSC360
DSC480
40 lbs. 8 oz.
29 lbs. 8 oz. each system
REFRIGERANT CHARGE R-22
MAINTENANCE