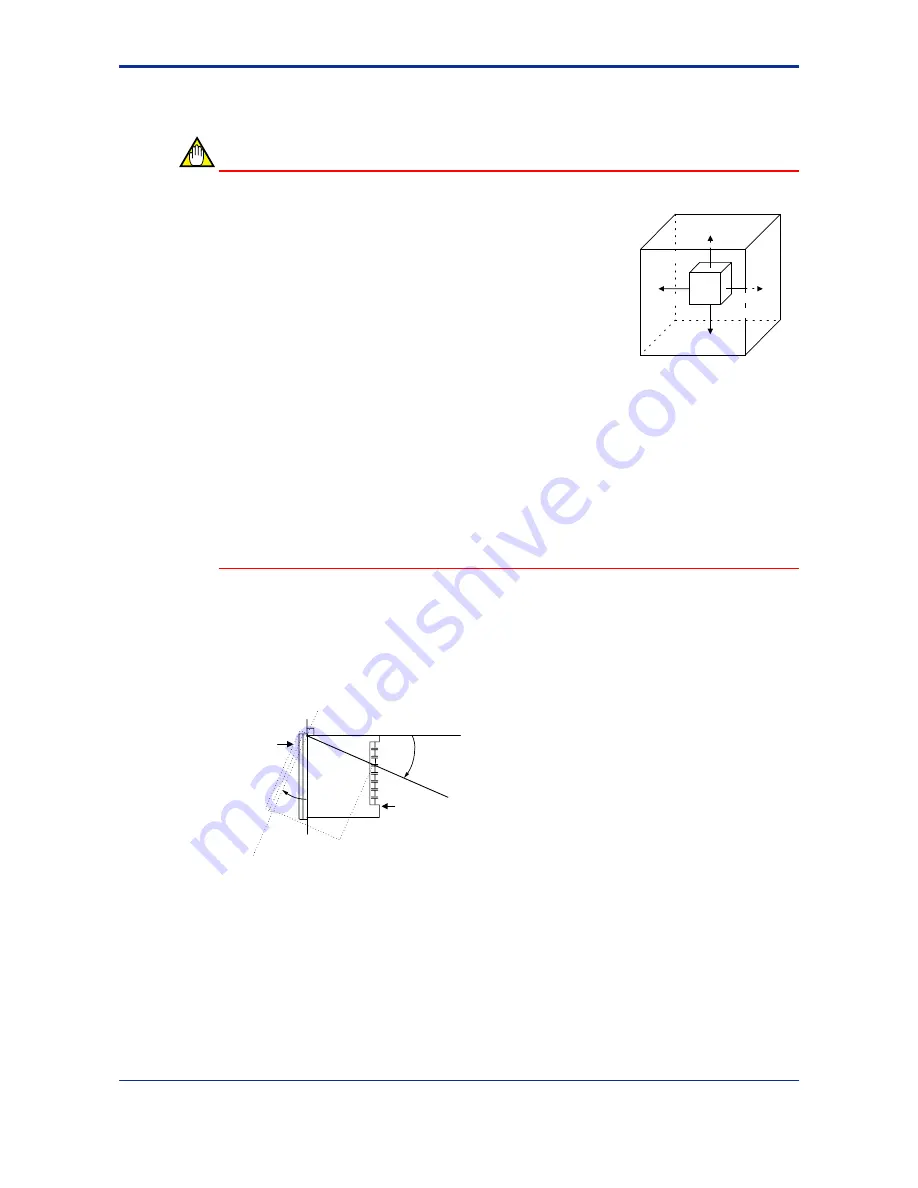
1-2
<Toc>
<1. Installation>
IM 05D01B02-41E
1.2
How to Install
NOTE
To install the controller, select a location where:
1.
no one may accidentally touch the terminals,
150mm
150mm
150mm
150mm
2.
mechanical vibrations are minimal,
3.
corrosive gas is minimal,
4.
temperature can be maintained at about 23
C and
the fluctuation is minimal,
5.
no direct radiant heat is present,
6.
no magnetic disturbances are caused,
7.
no wind blows against the terminal board (reference junction compensation element),
8.
no water is splashed,
9.
no flammable materials are around,
Never place the controller directly on flammable items or equipment.
If the controller has to be installed close to flammable items or equipment, be sure to
provide shielding panels all around the controller, at least 150 mm away from every side;
the panels should be made of either 1.43 mm-thick metal-plated steel plates or 1.6 mm-
thick uncoated steel plates.
●
Installation Position
Install the controller at an angle within 30
from horizontal with the front panel facing up-
ward. Do not install it facing downward. The position of right and left sides should be hori-
zontal.
Front panel
of controller
Must not
exceed 30
°
30
°
Rear of
controller
1st Edition : May 31,2000-00
Summary of Contents for UT750
Page 2: ...Blank Page...
Page 42: ...Blank Page...
Page 96: ...Blank Page...
Page 106: ...Blank Page...
Page 108: ...Blank Page...