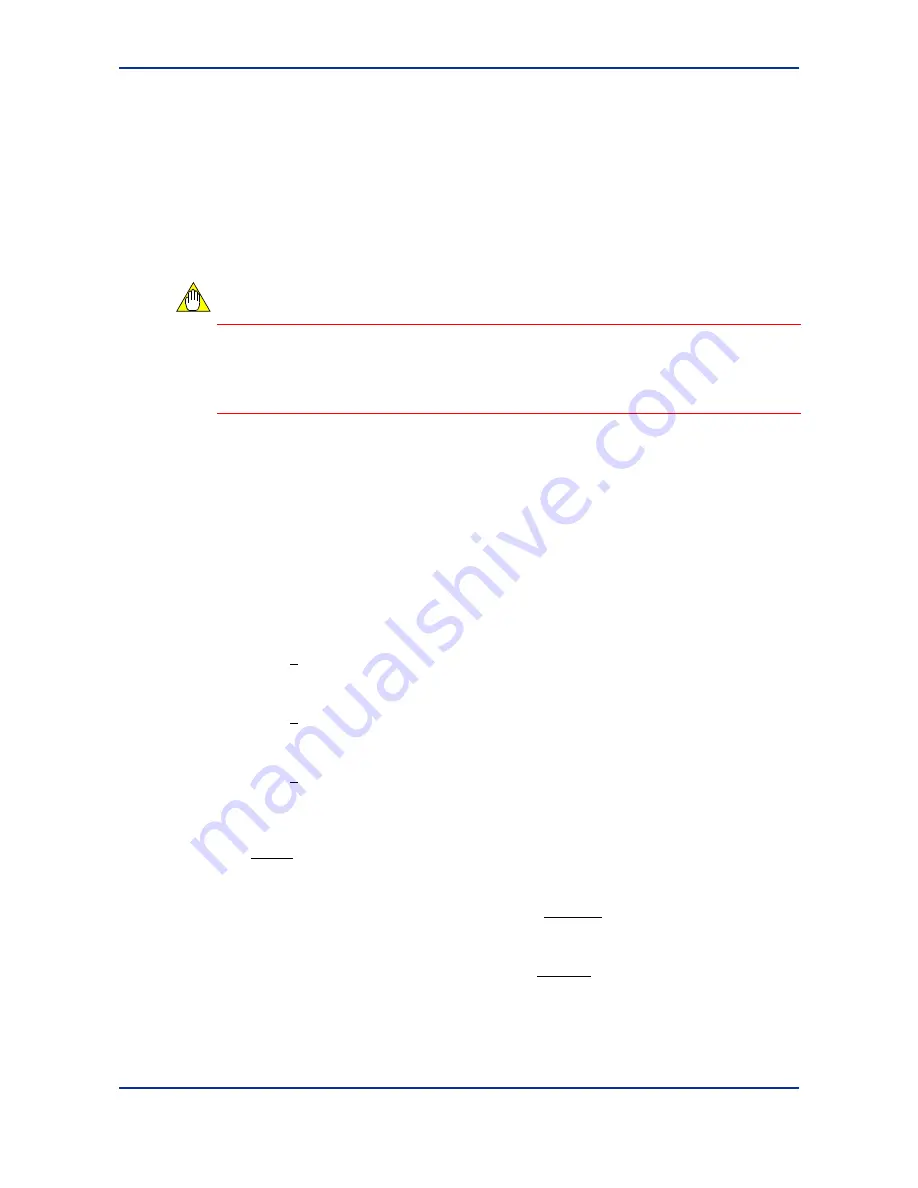
4-11
IM 34M6H55-02E
1st Edition : Apr 1, 2002-00
4.4 Example for Setting Entry Parameters
The following example shows a minimal set of entry parameters, which must be defined
for controlling a motor using the positioning module. The underlined values are to be
entered.
z
z
z
z
The motor used
Rated rotating speed: 3000 rpm
Encoder pulse count: 8000 pulses per rotation
CAUTION
Sometimes, you may need to set or change the command pulse/encoder pulse ratio on
the servo driver side; under such circumstances, always ensure that the parameters set
in the positioning module matches the setting of the servo driver. Always calculate the
values of the entry parameters after confirming the setting of the servo driver.
z
z
z
z
Mechanism
Direct shaft drive using a ball screw
Ball screw pitch: 5 mm/rot
Operation Range: -500 mm to +1000 mm
Maximum speed: 12000 mm/min [200 mm/s]
Contact Inputs: Positive/Negative-direction limit input (“b” contact), origin (“a” contact)
z
z
z
z
Calculation of entry parameters
–
Maximum speed selection (*01)
Set to 0 as the motor used is a servomotor rated at below 499,750 pps.
–
Pulse output mode (*02)
Set to 0 to use forward/reverse pulse output.
–
Rotating direction (*03)
Set to 0 so that positive data indicates forward pulse output.
–
Contact input polarity (*04)
Positive-direction limit value (b), Negative-direction limit input (b), Origin (a)
$0003
–
Positive-direction limit value (*05/*06)
1000 [mm] ÷ 5 [mm/rot] × 8000 [pulses/rot] = 1600000 [pulses]
–
Negative-direction limit value (*07/*08)
-500 [mm] ÷ 5 [mm/rot] × 8000 [pulses/rot] =-800000 [pulses]
Summary of Contents for F3YP14-0N
Page 13: ...Blank Page ...
Page 15: ...Blank Page ...
Page 23: ...Blank Page ...
Page 53: ...Blank Page ...
Page 60: ...7 5 IM 34M6H55 02E 1st Edition Apr 1 2002 00 Figure 7 2 Set Parameter Program ...
Page 65: ...7 10 IM 34M6H55 02E 1st Edition Apr 1 2002 00 Figure 7 6 Jog Stepping Program ...
Page 69: ...7 14 IM 34M6H55 02E 1st Edition Apr 1 2002 00 Figure 7 9 Origin Search Program ...
Page 77: ...7 22 IM 34M6H55 02E 1st Edition Apr 1 2002 00 Figure 7 15 Positioning Operation Program ...
Page 111: ...Blank Page ...
Page 127: ...Blank Page ...