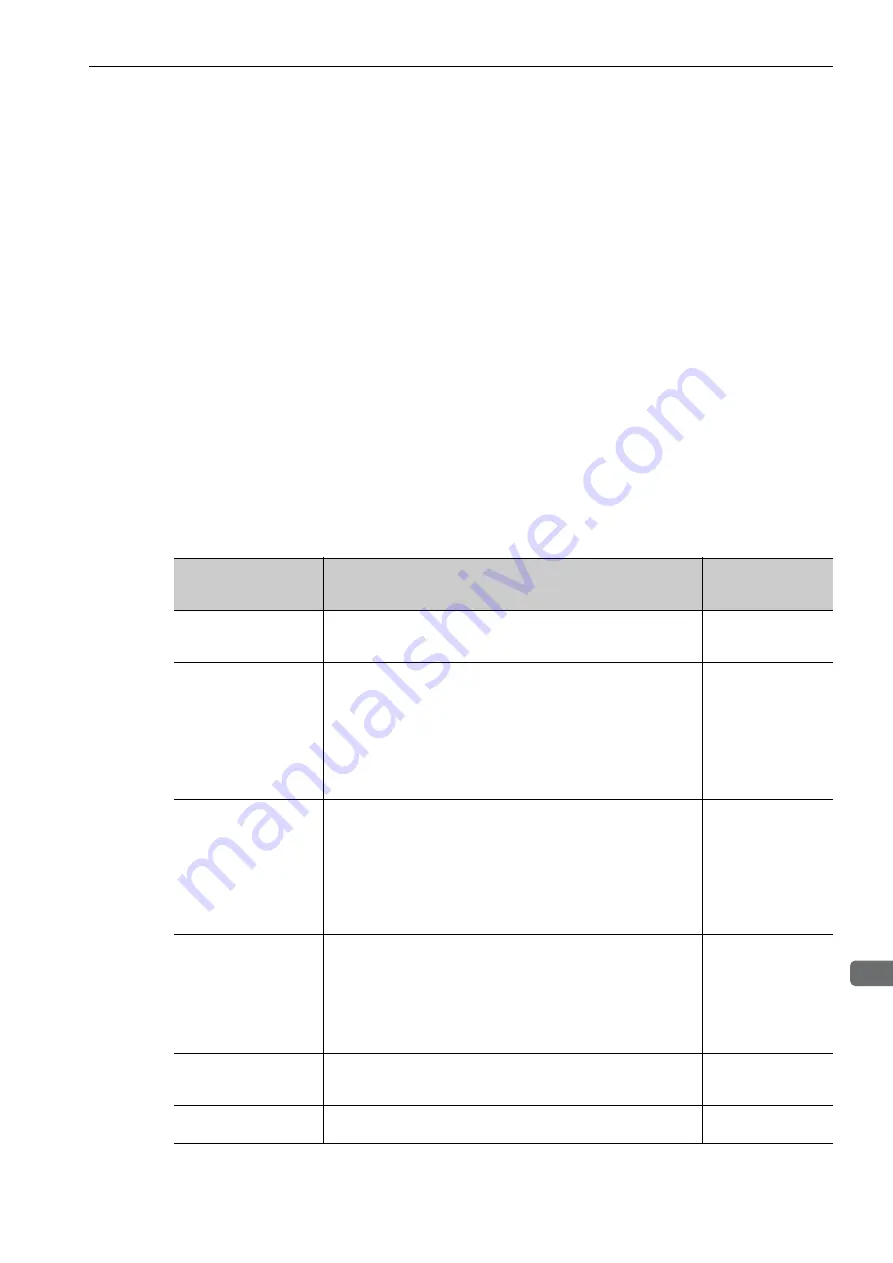
5.1 Type of Adjustments and Basic Adjustment Procedure
5-3
5
Adjustments
5.1
Type of Adjustments and Basic Adjustment Procedure
This section describes type of adjustments and the basic adjustment procedure.
5.1.1
Adjustments
Adjustments (tuning) are performed to optimize the responsiveness of the SERVOPACK.
The responsiveness is determined by the servo gain that is set in the SERVOPACK.
The servo gain is set using a combination of parameters, such as speed loop gain, position loop gain, filters,
friction compensation, and moment of inertia ratio. These parameters influence each other. Therefore, the
servo gain must be set considering the balance between the set values.
Generally, the responsiveness of a machine with high rigidity can be improved by increasing the servo gain. If
the servo gain of a machine with low rigidity is increased, however, the machine will vibrate and the respon-
siveness may not be improved. In such case, it is possible to suppress the vibration with a variety of vibration
suppression functions in the SERVOPACK.
The servo gains are factory-set to appropriate values for stable operation. The following utility function can be
used to adjust the servo gain to increase the responsiveness of the machine in accordance with the actual con-
ditions. With this function, parameters related to adjustment above will be adjusted automatically and the need
to adjust them individually will be eliminated.
This section describes the following utility adjustment functions.
Utility
Function for Adjust-
ment
Outline
Applicable Control
Method
Tuning-less
Levels Setting
(Fn200)
This function is enabled when the factory settings are used. This
function can be used to obtain a stable response regardless of the
type of machine or changes in the load.
Speed and Position
Advanced Autotuning
(Fn201)
The following parameters are automatically adjusted using internal
references in the SERVOPACK during automatic operation.
• Moment of inertia ratio
• Gains (position loop gain, speed loop gain, etc.)
• Filters (torque reference filter, notch filter)
• Friction compensation
• Anti-resonance control adjustment function
• Vibration suppression function
Speed and Position
Advanced Autotuning
by Reference (Fn202)
The following parameters are automatically adjusted with the posi-
tion reference input from the host controller while the machine is in
operation.
• Gains (position loop gain, speed loop gain, etc.)
• Filters (torque reference filter, notch filter)
• Friction compensation
• Anti-resonance control adjustment function
• Vibration suppression function
Position
One-parameter Tuning
(Fn203)
The following parameters are manually adjusted with the position or
speed reference input from the host controller while the machine is
in operation.
• Gains (position loop gain, speed loop gain, etc.)
• Filters (torque reference filter, notch filter)
• Friction compensation
• Anti-resonance control adjustment function
Speed and Position
Anti-Resonance
Control Adjustment
Function (Fn204)
This function effectively suppresses continuous vibration.
Speed and Position
Vibration Suppression
Function (Fn205)
This function effectively suppresses residual vibration if it occurs
when positioning.
Position