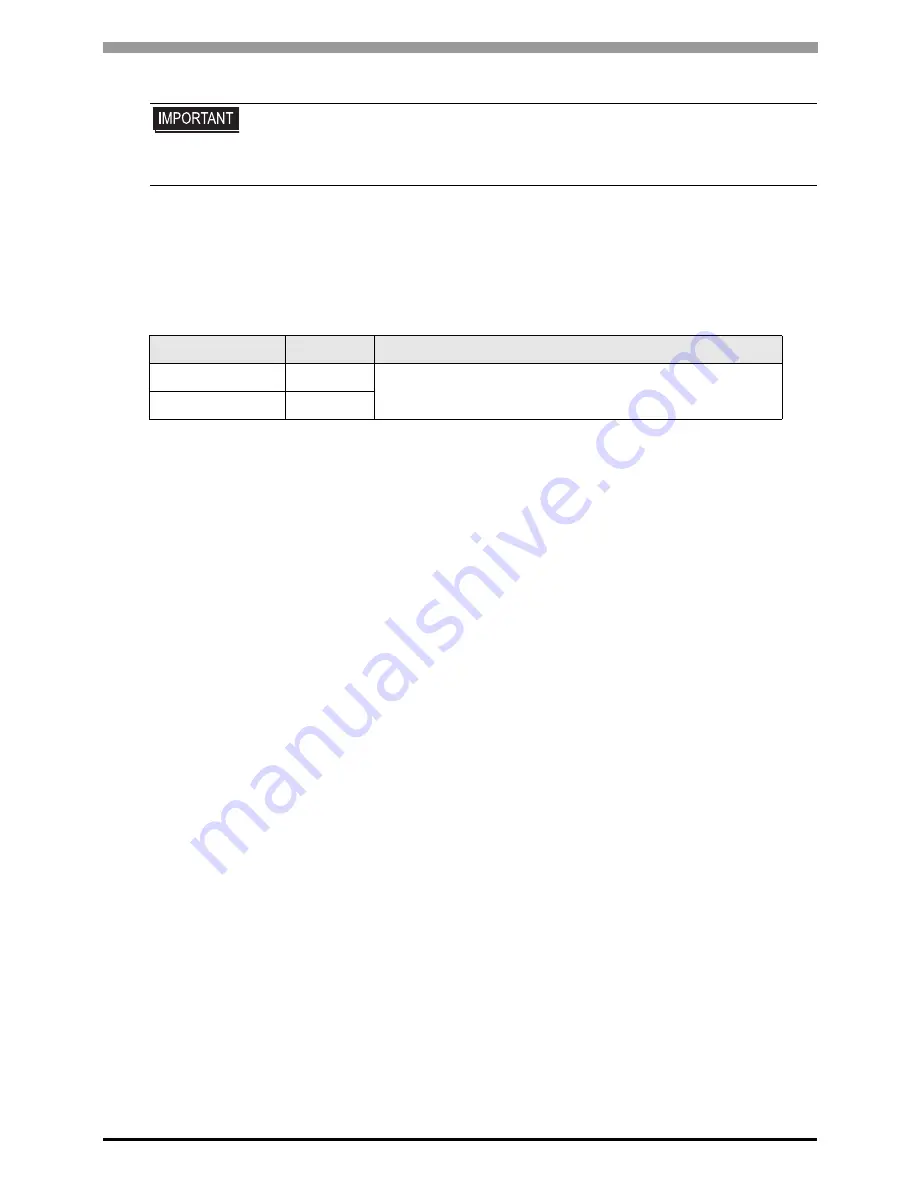
MP/INVERTER/SERVO Ethernet Driver
GP-Pro EX Device/PLC Connection Manual
58
8
Write the settings to the Sub CPU.
-V Series Setting
Set up communication settings with rotary switches (S1 and S2).
For details on communication settings, please refer to the manual of the External Device.
Notes
•
Check with a network administrator about IP address. Do not set the duplicate IP address.
• To write the settings, select the [Save to flash after transferring to the controller] check
box.
If the data is transferred without selecting the check box, the transferred data is
deleted when restarting the External Device.
Rotary Switch
Settings
Setup Description
S1 (x16)
0
Station address
S2 (x1)
3