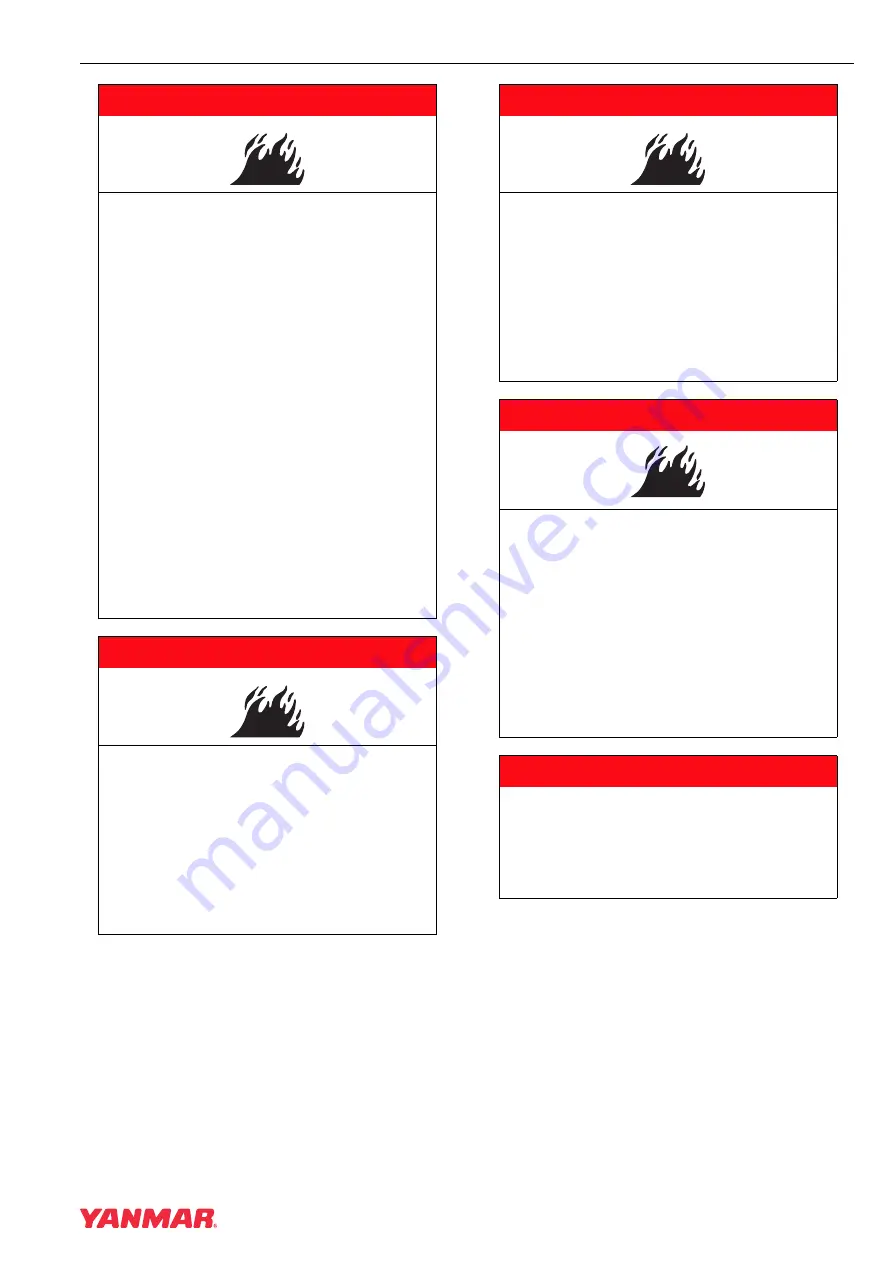
PERIODIC MAINTENANCE
BY Service Manual
4-3
Before You Begin Servicing
A
DANGER
FIRE AND EXPLOSION HAZARD!
• Diesel fuel is flammable and explosive
under certain conditions.
• When you remove any fuel system
component to perform maintenance
(such as changing the fuel filter) place
an approved container under the
opening to catch the fuel.
• NEVER use a shop rag to catch the
fuel. Vapors from the rag are
flammable and explosive.
• Wipe up any spills immediately.
• Wear eye protection. The fuel system
is under pressure and fuel could spray
out when you remove any fuel system
component.
• Failure to comply will result in death or
serious injury.
0000009en
A
DANGER
FIRE AND EXPLOSION HAZARD!
• Diesel fuel is flammable and explosive
under certain conditions.
• NEVER use diesel fuel as a cleaning
agent.
• Failure to comply will result in death or
serious injury.
0000012en
A
DANGER
FIRE AND EXPLOSION HAZARD!
• Diesel fuel is flammable and explosive
under certain conditions.
• NEVER remove the fuel cap with the
engine running.
• Failure to comply will result in death or
serious injury.
0000011en
A
DANGER
FIRE AND EXPLOSION HAZARD!
• Only use the key switch to start the
engine.
• NEVER jump-start the engine. Sparks
caused by shorting the battery to the
starter terminals may cause a fire or
explosion.
• Failure to comply will result in death or
serious injury.
0000004en
A
DANGER
NEVER start the engine unless the air
filter is installed.
Failure to comply will result in death or
serious injury.
0000025en
Summary of Contents for BY series
Page 1: ...BY series 4BY 6BY SERVICE MANUAL...
Page 2: ...BY Service Manual BY series SERVICE MANUAL 4BY 6BY P N 0BBY0 G00100 MARINE ENGINES...
Page 5: ...TABLE OF CONTENTS iv 4BY 6BY Service Manual This Page Intentionally Left Blank...
Page 7: ...INTRODUCTION 1 2 BY Service Manual This Page Intentionally Left Blank...
Page 21: ...SAFETY 2 14 BY Service Manual Safety Precautions This Page Intentionally Left Blank...
Page 131: ...FUEL SYSTEM 6 2 BY Service Manual This Page Intentionally Left Blank...
Page 159: ...FUEL SYSTEM 6 30 BY Service Manual Repair This Page Intentionally Left Blank...
Page 161: ...COOLING SYSTEM 7 2 BY Service Manual This Page Intentionally Left Blank...
Page 181: ...COOLING SYSTEM 7 22 BY Service Manual Repair This Page Intentionally Left Blank...
Page 183: ...LUBRICATION 8 2 BY Service Manual This Page Intentionally Left Blank...
Page 199: ...LUBRICATION 8 18 BY Service Manual Repair This Page Intentionally Left Blank...
Page 201: ...TURBOCHARGER 9 2 BY Service Manual This Page Intentionally Left Blank...
Page 211: ...TURBOCHARGER 9 12 BY Service Manual Repair This Page Intentionally Left Blank...
Page 213: ...STARTER MOTOR 10 2 BY Service Manual This Page Intentionally Left Blank...
Page 221: ...ALTERNATOR 11 2 BY Service Manual This Page Intentionally Left Blank...
Page 261: ...ELECTRICAL AND ECU 12 34 BY Service Manual Repair This Page Intentionally Left Blank...
Page 263: ...TROUBLESHOOTING 13 2 BY Service Manual This Page Intentionally Left Blank...