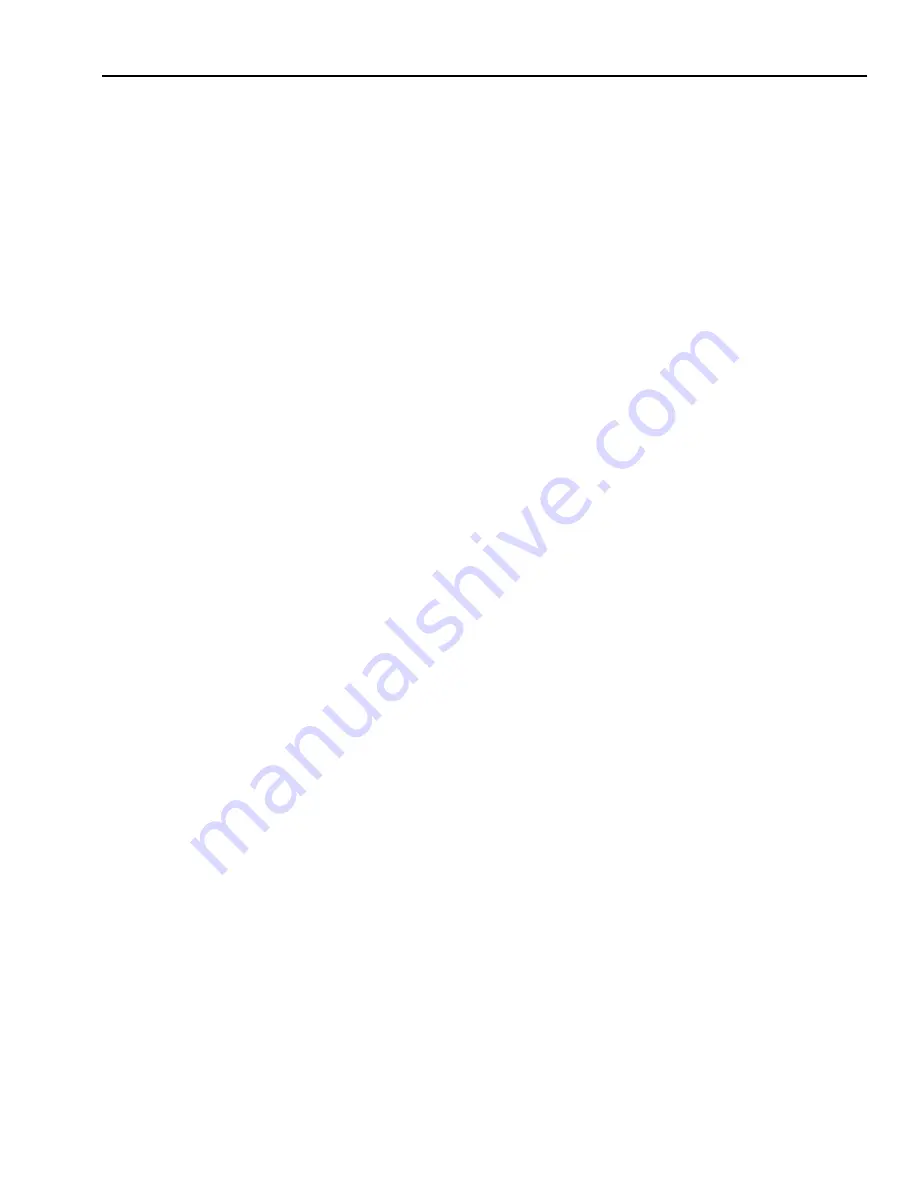
7800 SERIES EC7890A,B/RM7890A,B RELAY MODULE
65-0204–1
11
Mounting Wiring Subbase
NOTE:
For installation dimensions, see Fig. 1 or 2.
1
Mount the subbase in any position except horizontally
with the bifurcated contacts pointing down. The standard
vertical position is recommended. Any other position
decreases the maximum ambient temperature rating.
2
Select a location on a wall, burner or electrical panel.
The Q7800 can be mounted directly in the control
cabinet. Be sure to allow adequate clearance for
servicing, installation, access and removal of the 7890,
dust cover, flame amplifier, flame amplifier signal
voltage probes, electrical signal voltage probes and
electrical field connections.
3
For surface mounting, use the back of the subbase as
a template to mark the four screw locations. Drill the
pilot holes.
4
Securely mount the subbase using four no. 6 screws.
WIRING
1
a. For proper subbase wiring, refer to Fig. 7.
b.
For proper remote wiring of the Keyboard Display
Module; refer to the Specifications for the
Keyboard Display Module (65-0090),
Communication Interface Base Unit (63-2278),
DATA CONTROLBUS MODULE™ (65-0091) or
Extension Cable Assembly (65-0131).
2
Disconnect the power supply from the main disconnect
before beginning installation to prevent electrical shock
and equipment damage. More than one disconnect
may be involved.
3
All wiring must comply with all appropriate electrical
codes, ordinances and regulations. Wiring, where
required, must comply with NEC Class 1 (Line
Voltage) wiring.
4
Recommended wire size and type: Use no. 14, 16, or 18
copper conductor (TTW60C or THW75C or THHN90C)
600 volt insulation wire for all line voltage terminals. For
high temperature installations, use wire selected for a
temperature rating above the maximum operating
temperature. All leadwires must be moisture resistant.
5
Recommended grounding practices:
a.
Use the earth ground to provide a connection
between the subbase and the control panel or the
equipment. The earth ground wire must be
capable of conducting the current to blow the 20A
fuse (or breaker) in event of an internal short
circuit. The 7890 needs a low impedance ground
connection to the equipment frame which, in turn,
needs a low impedance connection to earth
ground. For a ground path to be low impedance
at RF frequencies, the connection must be made
with minimum length conductors that have a
maximum surface area. Wide straps or brackets
are preferred rather than leadwires. Be careful to
verify that mechanically tightened joints along the
ground path, such as pipe or conduit threads or
surfaces held together with fasteners, are free of
nonconductive coatings and are protected
against mating surface corrosion.
b.
The earth ground terminal for each 7890 must be
grounded to the metal control panel with wire as
short as practical. Each ground wire must be
capable of carrying a fault current equal to the
rating of the protective fuse (20A). A number 14
copper conductor is adequate but wide straps or
brackets are preferred rather than leadwires.
6
Recommended wire routing for flame detector
leadwires:
•
Do not run high voltage ignition transformer
wires in the same conduit with the flame
detection wiring.
•
Do not route scanner wires in a conduit with line
voltage circuits.
•
Enclose scanner wires without armor cable in
metal cable or conduit.
•
Follow directions given in the flame detector
Instructions.
7
Maximum wire lengths:
a.
For the 7890, the maximum length of leadwire to
the control terminal input is 300 feet.
b.
For the flame detector leadwires, the maximum
flame sensor leadwire length is limited by the
flame signal strength.
8
Make sure loads do not exceed the terminal ratings.
Refer to the label on the 7890 or to the ratings in the
Specifications, see Table 1A or 1B.
9
Check the power supply circuit. The voltage and
frequency tolerance must match those of the 7890. A
separate power supply circuit may be required for the
7890 with the required disconnect means and overload
protection added.
J
Check all wiring circuits and complete the Static
Checkout, see Table 4, before installing the 7890 on the
subbase.
K
Install all electrical connectors.
L
Restore power to the panel.