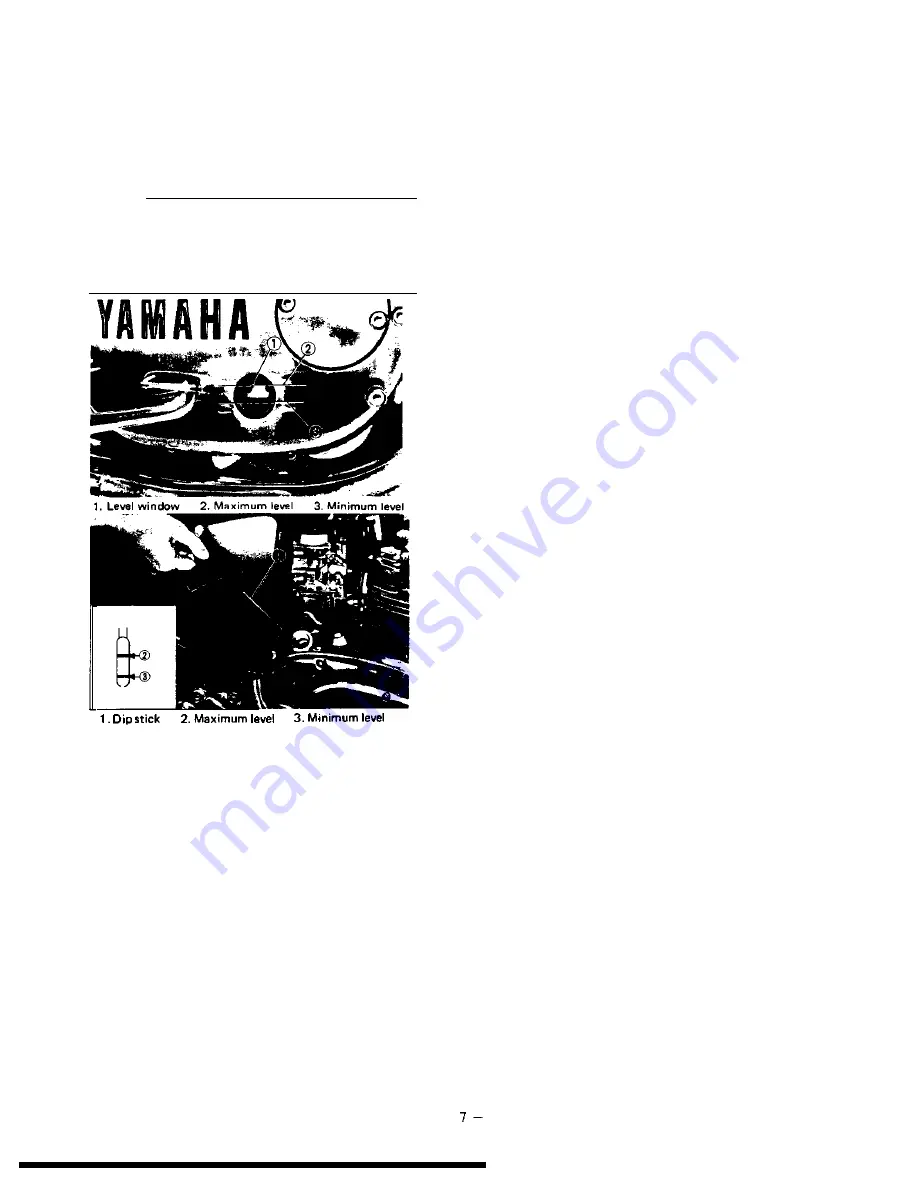
2 With the engine stopped, check the oil
level through the level window located at
the lower part of the right side crankcase
cover, or screw the dip stick completely
out and then the stick in the hole.
NOTE:
Wait a few minutes until the oil level settles
before checking. When checking engine oil
level with the dip stick, let the unscrewed dip
stick rest on the case threads.
3. The oil level should be between maxi-
mum and minimum levels. If the level
is lower, add sufficient oil to raise it to
the proper level.
Summary of Contents for XS650 Series
Page 1: ......
Page 4: ...CHAPTER 1 GENERAL INFORMATION l l MACHINE IDENTIFICATION a 1 l 2 SPECIAL TOOLS ...
Page 39: ......
Page 45: ......
Page 55: ......
Page 76: ......
Page 77: ......
Page 78: ......
Page 79: ...XS650E Supplementary FOR XS650E MODELS AFTER ENGINE SERIAL NO 2FO 006501 ...
Page 84: ... _ _ _I __ l i _ _ I l R ...
Page 108: ......
Page 109: ......
Page 110: ......
Page 111: ......
Page 112: ......
Page 116: ...MAINTENANCE AND LUBRICATION CHART PERIODIC MAINTENANCE EMISSION CONTROL SYSTEM 3 ...
Page 117: ...t c c ...
Page 140: ......
Page 141: ...Supplementary ...
Page 149: ...2 Troubleshooting inspection ...
Page 150: ...LOW BEAM DOES NOT LlGHT WHEN HIGH BEAM IS DEFECTIVE ...
Page 161: ......
Page 162: ......
Page 163: ......
Page 164: ......
Page 165: ...Supplementary FOR XS650SE MODELS AFTER ENGINE SERIAL NUMBER 2FO 114241 ...
Page 174: ... R W wire to 118 ...
Page 175: ... 119 ...
Page 186: ......
Page 187: ......
Page 188: ......
Page 189: ......
Page 190: ......
Page 200: ...1 ...
Page 202: ...Torque Specifications A Nut ...
Page 212: ......
Page 213: ......
Page 214: ......
Page 215: ......