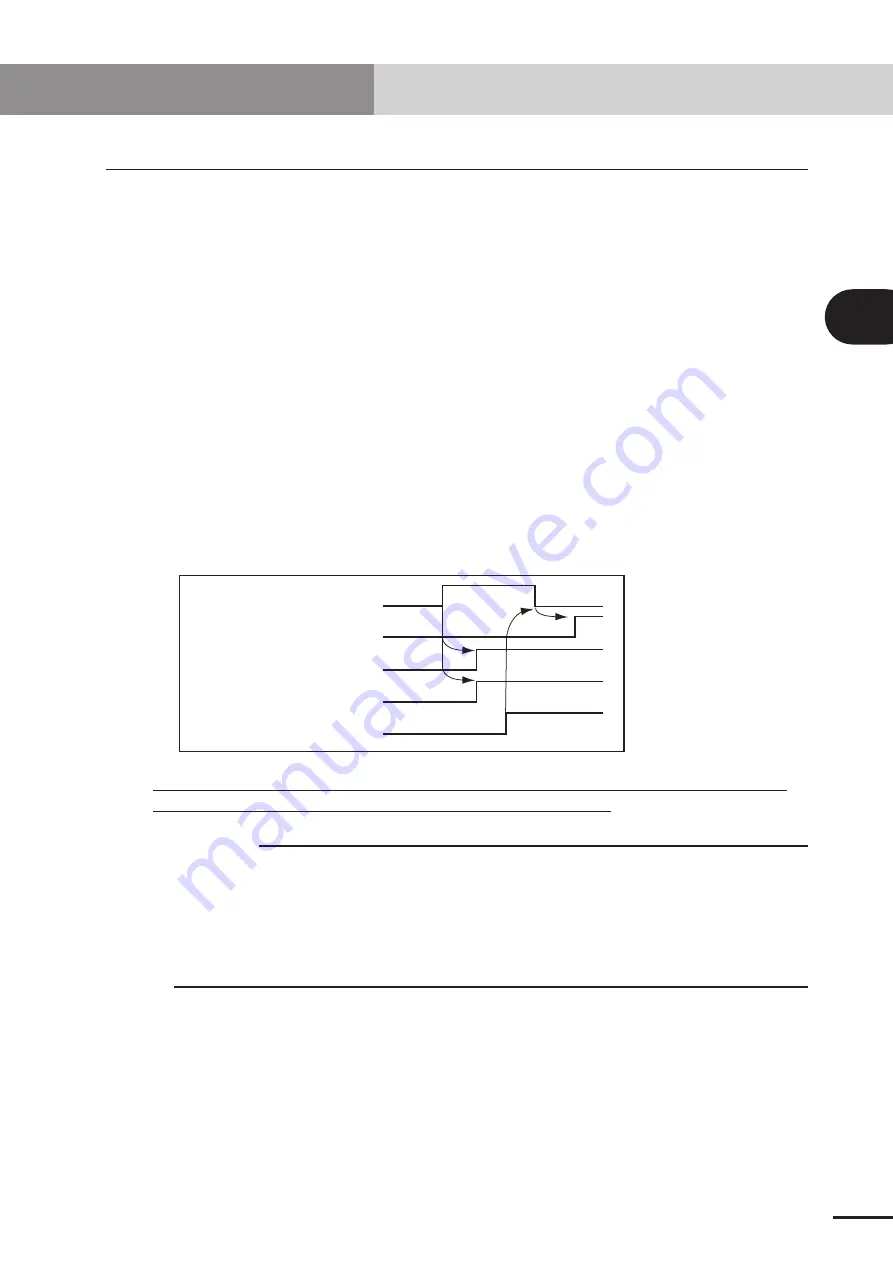
3-3
Chapter
3
COMMUNICA
TION
2. Initial process for connecting to CC-Link system
The initial data process must be carried out to correctly connect to the CC-Link system.
2.1 Initial
data
process
The initial data process is carried out to confirm that the robot controller is correctly
connected to the CC-Link system. Prepare the process on the master station PLC side so
that the following type of process is always carried out before data is exchanged.
Initial data process (master station PLC side)
q
Confirm that RX(n+7)8 (initial data process request flag) is ON.
w
Turn RYn0 (emergency stop input) and RYn9 (interlock input) ON.
e
Turn RY(n+7)8 (initial data process completion flag) ON.
r
Confirm that RX(n+7)8 (initial data process request flag) is OFF.
t
Confirm that RX(n+7)B (remote Ready) is ON.
RX (n+7) 8
on
off
on
off
on
off
on
off
on
off
RYn0
RYn9
RY (n+7) 8
RX (n+7) B
The robot controller internal process will automatically start when the power is
turned ON and the system is returned from an error state.
c
CAUTION
• RX(n+7) B (remote Ready) must always be used on the master station PLC
side as the fl ag to indicate whether the robot controller is operating correctly.
• When starting up the system in the emergency stop state using RYn0
(emergency stop input), carry out the initial data process fi rst, and then turn
RYn0 (emergency stop input) OFF. The robot controller will start up in the
servo OFF state when the power is turned ON.
2. Initial process for connecting to CC-Link system
Summary of Contents for RCX series
Page 1: ...User s Manual ENGLISH E E78 Ver 1 08 CC Link YAMAHA NETWORK BOARD RCX series ...
Page 2: ......
Page 12: ......
Page 22: ......
Page 34: ...2 12 MEMO ...
Page 36: ......
Page 50: ......
Page 60: ......
Page 81: ...Chapter 6 APPENDIX Contents 1 Term definition 6 1 ...
Page 82: ......