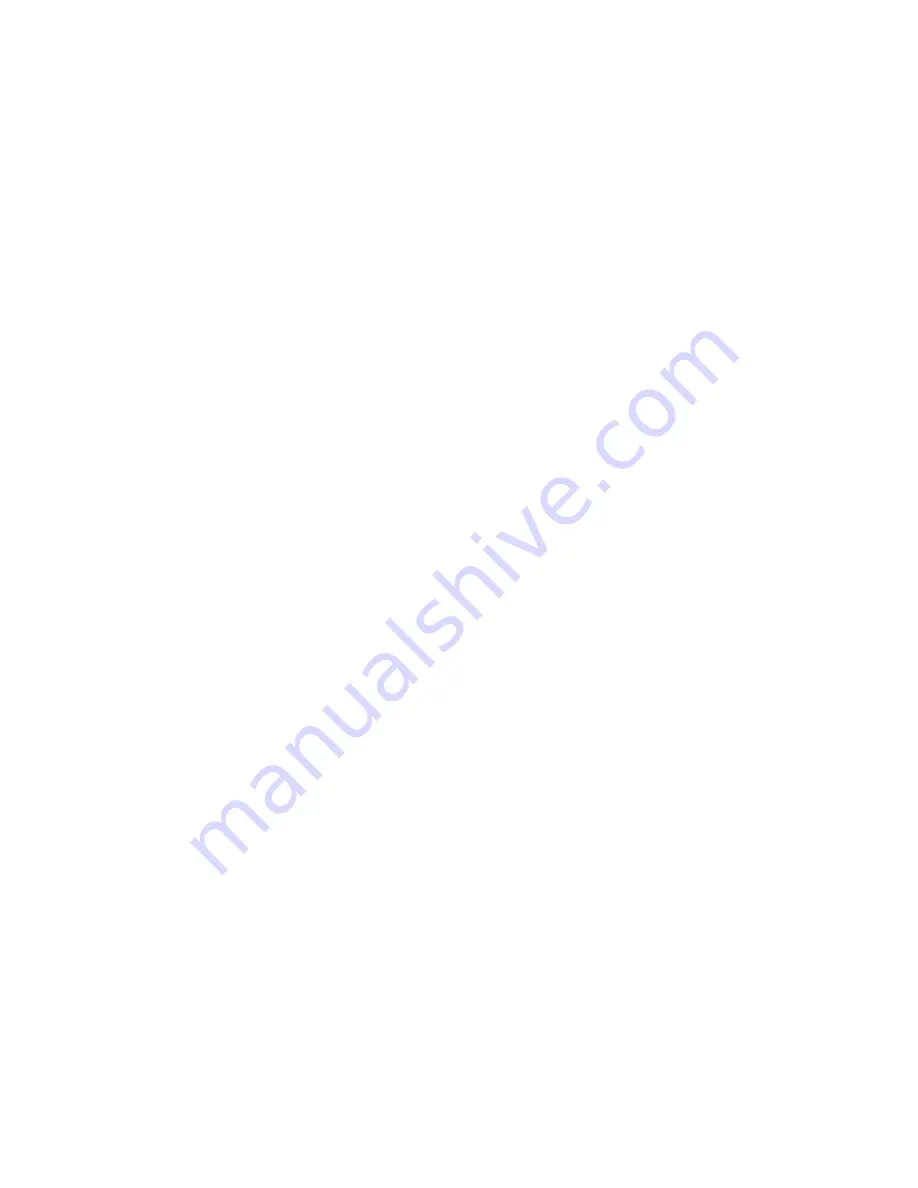
Description of Operation
See Figure 2 for the logic diagram.
This section includes information on the following
components:
•
Control handle switches (ON/OFF and propor-
tional)
•
Hall effect directional/speed control
•
Control handle card
•
ZAPI™ motor controller
•
Traction motor
•
Main contactor
•
Brake coil
•
Lift pump motor
•
Lift time-out
•
Batteries
ON/OFF switches are used for:
•
Single speed lift and lower functions
•
Half speed lift and lower functions
•
Horn
•
Traction reversing
•
Creep (Turtle) speed
•
Throttle neutral signal
MSW020/025-E and MSW025/030-F
: Standard lift
switches are ON/OFF type. Standard left-side lift
switches are at half speed. The right-side lift switches
are at full speed. Optional proportional lifting switches
are available on the right side. Proportional switches
provide a variable output to regulate the speed of the
lift and lower functions.
All lower switches are proportional type switches
which allow the operator to maintain maximum control
of the load when lowering.
MPB040/45/50-E
: Use only full speed lift and lower
switches.
A Hall effect throttle control is used to provide a direc-
tional/speed signal. The neutral switch verifies the
neutral position during the self check at startup. The
Hall effect throttle control, neutral switch, traction re-
versing switch, horn switch, and creep (turtle) speed
switch are an integral part of the control handle card
and not serviced separately. The switches that control
the hydraulic functions mount into the control handle
and are serviced separately.
The Hall effect throttle control, the proportional
switches and all the ON/OFF switches provide input
signals to the control handle card. The control handle
card uses serial communication to send these signals
to the ZAPI™ motor controller.
The ZAPI™ motor controller contains the system
logic. The motor controller receives the inputs, pro-
cesses the commands, and provides outputs to the
appropriate component to activate them.
The traction motor armature and separately excited
field are powered directly by the motor controller. No
contactors are involved in the traction circuit.
The main contactor opens to remove power from the
truck to disable all traction and lift functions in the
event of an electric failure.
Energizing the brake coil pulls the brake pressure
plate away from the friction disc to disengage the
brake. The controller powers the brake coil based on
signals from the control handle arm proximity switch
and the Directional/Speed Control. The controller also
contains logic to engage the brake regardless of han-
dle position if the truck is stationary.
MSW020/025-E and MSW025/030-F
: The motor
controller energizes the series wound lift pump motor
when either lift function switch is depressed. The ap-
plied voltage to the motor varies to adjust motor RPM
and pump output to the lift function.
MPB040/045/050-E
: The motor controller energizes
the series wound lift pump motor when either lift func-
tion switch is depressed.
MSW020/025-E and MSW025/030-F
: All trucks have
a solenoid operated lowering valve at the pump. The
motor controller activates the solenoid coil to open the
lowering valve. The motor controller varies the voltage
to the lowering solenoid to provide proportional lower-
ing.
MPB040/045/050-E
: All trucks have a solenoid oper-
ated lowering valve at the pump. The motor controller
activates the solenoid coil to open the lowering valve.
2200 YRM 1007
Description of Operation
3
Summary of Contents for MPB040-E
Page 4: ......
Page 10: ...Hydraulic Pump 1900 YRM 1018 Figure 4 Hydraulic Unit 6 ...
Page 19: ......
Page 65: ...Figure 30 Switch Position Mode Chart 2200 YRM 1007 Battery Charger Accusense by DPI 41 ...
Page 79: ......
Page 80: ...2200 YRM 1007 10 16 8 16 1 14 9 13 12 12 7 11 ...
Page 84: ......
Page 93: ......
Page 95: ...Maintenance DC MOTOR MAINTENANCE ALL ELECTRIC LIFT TRUCKS PART NO 524158039 0620 YRM 0294 ...
Page 98: ......
Page 128: ...NOTES 30 ...
Page 129: ......