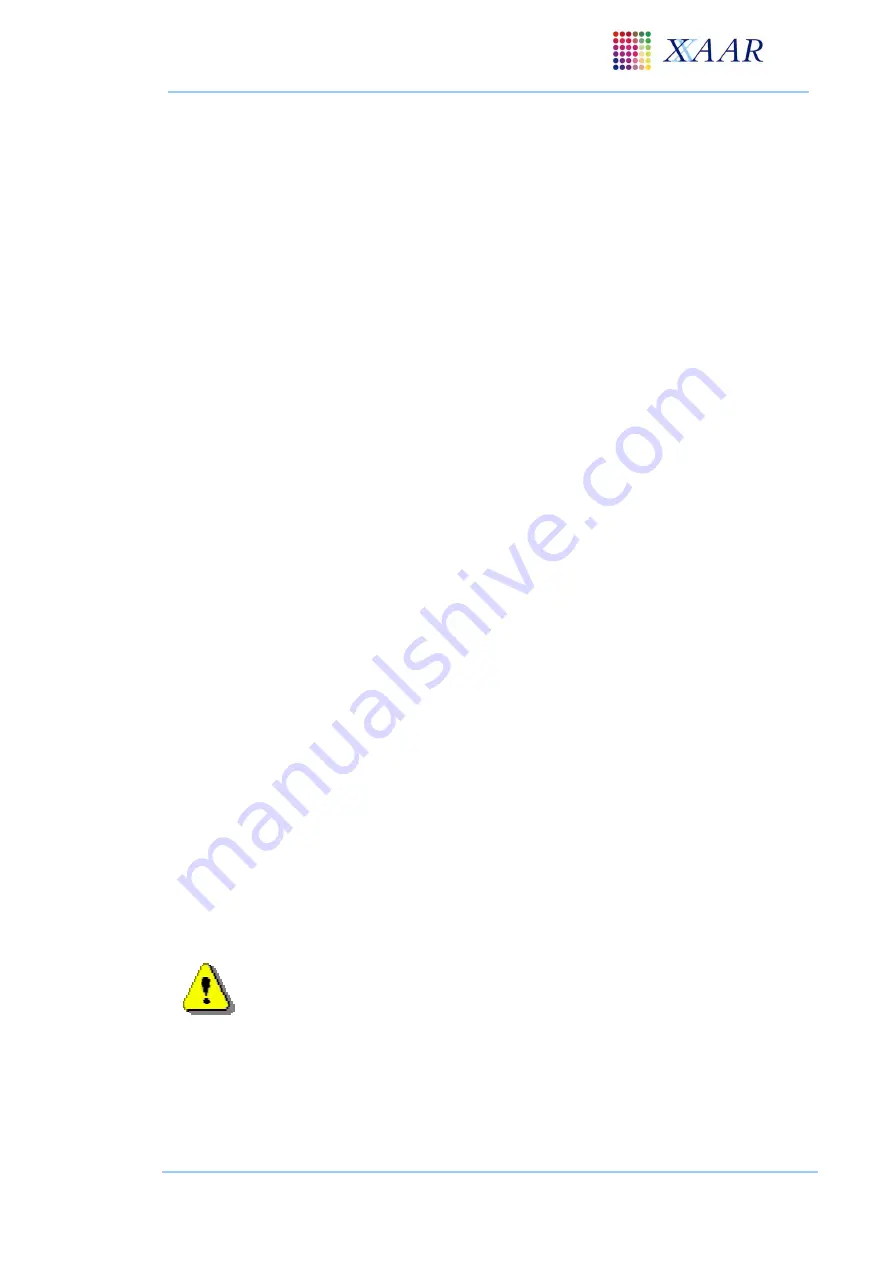
XJ128 and XJ128 Plus Printhead
XJ128 Guide to Operation
Xaar Document no: D031010302 Version A
Page 40
The different forces causing risk of malfunction are Start/Stop accelerations and vibrations from
moving the head. The maximum acceleration/deceleration force specified is 4g during operation.
7.4.1 Small ink reservoir
The design of the small ink reservoir should consider the following:
Position it as close to the printhead as possible to minimise tube length and pressure variations
between the printhead and reservoir.
Keep the ink volume within the small ink reservoir small, to avoid pressure surges through movement
of the reservoir (in the case of a scanning system).
7.4.2 Ink pump system
The ink pump system should be able to respond in such a manner that the ink level in the reservoir is
maintained at as constant level as possible. This will minimise ink pressure variation to the printhead.
It is also recommended that the pump system can detect a low level of ink in the main ink tank to
avoid pumping air into the ink supply system. It is possible for the ink pump to shed particles, so it is
recommended that this be placed before the primary system ink filter.
7.4.3 System filter
The system ink filter must be capable of filtering the ink to an adequate level. In use it is important
the filter does not contain air, this can cause response delays in the ink feedback system.
7.4.4 Ink tubing
All ink tubing lengths should be kept to a minimum. This is most important between the printhead and
the ink reservoir. Tube diameters should be as large as possible to aid ink flow. No tubing less than
3mm ID should be used between the printhead and the
‘
local
’
small ink reservoir. The maximum
length for ink tubing between these components is 0.5m. Details for this are also found in the
appropriate Ink and Printhead User Guide documentation.
7.5 Filling the printhead and supply system
7.5.1 Cleaning the ink supply system
It is recommended that prior to filling the ink supply system, all parts that come into
contact with the ink are cleaned and dried prior to filling with ink.
The following process details how to clean ink supply components that use materials that are
compatibility approved by Xaar.