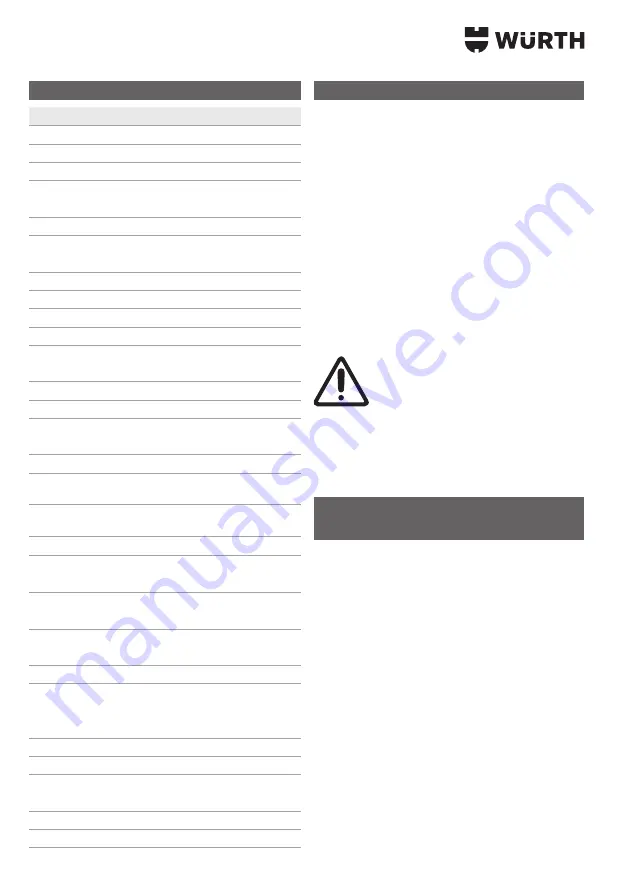
20
Technical Data
Item no.
5952 000 160
Protection class (EN 60529)
IP 23 S
Class of insulation
F
Cooling type
F
Labelling
CE, S
Dimension (LxWxH) in mm
337 x 130 x 211
Weight
5.1 kg
Noise emission dB(A)
< 70
Mains ratings
Mains voltage
230/1∼ V
Frequency
50-60 Hz
Positive mains tolerance
15%
Negative mains tolerance
40%
Power cord
3 x 2.5 mm²
Mains plug
Schuko socket
Current consumption I
1
(100%/40°C)
14.2 A
Current consumption I
1
(60%/40°C)
15.6 A
Current consumption I
1
(max. current)
22.5 A
Mains fuse
16 A
Power factor I
2 max
0.99 cos ϕ
Max. permissible mains impedance
Z
max
according to IEC 61000-3-11/-12
321 mΩ
Power consumption S
1
(100%/40°C)
3.3 kVA
Power consumption S
1
(60%/40°C)
3.6 kVA
Rated power S
1
(max. current)
5.2 kVA
Maximum effective mains current
8.1 I
1eff
/A
Power factor λ at l
2max
0.97
Welding
TIG welding range
(I
2 min
- I
2max
/ U
2 min
- U
2max
)
15 – 160 A /
10.6 – 16.4 V
No-load voltage U
O
=U
S
70-98 V/DC
No-load voltage U
r
(VRD)
13-15 V/DC
Electrode welding range
(I
2 min
- I
2max
/ U
2 min
- U
2max
)
10 – 150 A /
20.4 – 26.0 V
Open circuit voltage max.
< 113 V
Power setting
stepless
Curve characteristic
falling
Welding current at CDF 100%
110 A
Welding current at CDF 60%
120 A
CDF at max. welding current
30 %
Before start-up
Secure the detachable handle (Fig. I)
▸
Click the handle
[1]
in on the welding unit.
Transport
▸
Always remove the mains plug before trans-
porting.
▸
Carry the device using the handle.
Installation
▸
Install the device in a safe place on a horizontal,
dry surface. Ensure that the ventilation slots of the
cooling ribs are always free.
Quick-start guide
▸
Insert the mains plug into the plug socket.
▸
Connect the workpiece lead and electrode holder
to the connecting sockets
[3]
and
[4]
.
Attention
Observe the polarity as specified by
the electrode manufacturer (see also
Electrode welding).
▸
Clamp a stick electrode in the electrode holder.
▸
Switch the system on at the switch
[6]
.
▸
Set the welding current at the rotary controller
[10]
.
3
The system is ready for welding.
Connecting the workpiece lead
(Fig. III)
▸
When selecting the workplace, ensure that the
workpiece lead and ground clamp can be cor-
rectly connected.
▸
The ground clamp must have good electrically
conductive contact with a bare metal part of the
welding bench or workpiece. It must be located
in the immediate vicinity of the welding point so
that the welding current cannot find its own way
back via machine parts, ball bearings or electrical
circuits.
Do not connect the ground clamp to the welding
machine or gas cylinder as otherwise the weld-
ing current will run through the PE conductor
connections and could destroy them.
Fasten the earthing clamp securely to the weld-
ing bench or workpiece.