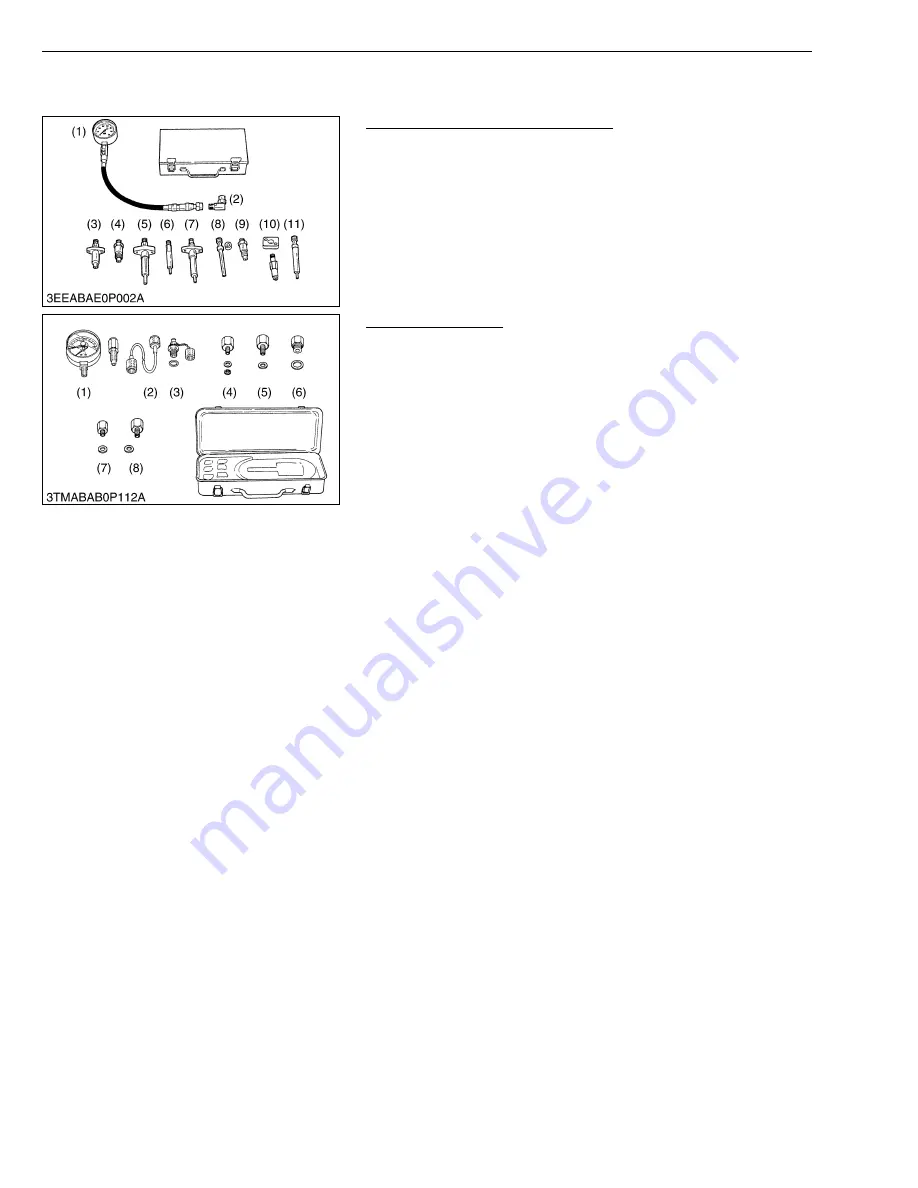
G-28
V3307-DI-T-E2B, WSM
G
GENERAL
5. SPECIAL TOOLS
Diesel Engine Compression Tester
Code No :
07909-30208 (Assembly)
Application :Use to measure diesel engine compression and
diagnostics of need for major overhaul.
W1024200
Oil Pressure Tester
Code No :
07916-32032
Application : Use to measure lubricating oil pressure.
W1024318
(1) Gauge
(2)
L
Joint
(3) Adaptor
A
(4) Adaptor
B
(5) Adaptor
C
(6) Adaptor
E
(7) Adaptor
F
(8) Adaptor
G
(9) Adaptor
H
(10) Adaptor
I
(11) Adaptor
J
(1) Gauge
(2) Cable
(3) Threaded Joint
(4) Adaptor
1
(5) Adaptor
2
(6) Adaptor
3
(7) Adaptor
4
(8) Adaptor
5
KiSC issued 01, 2009 A