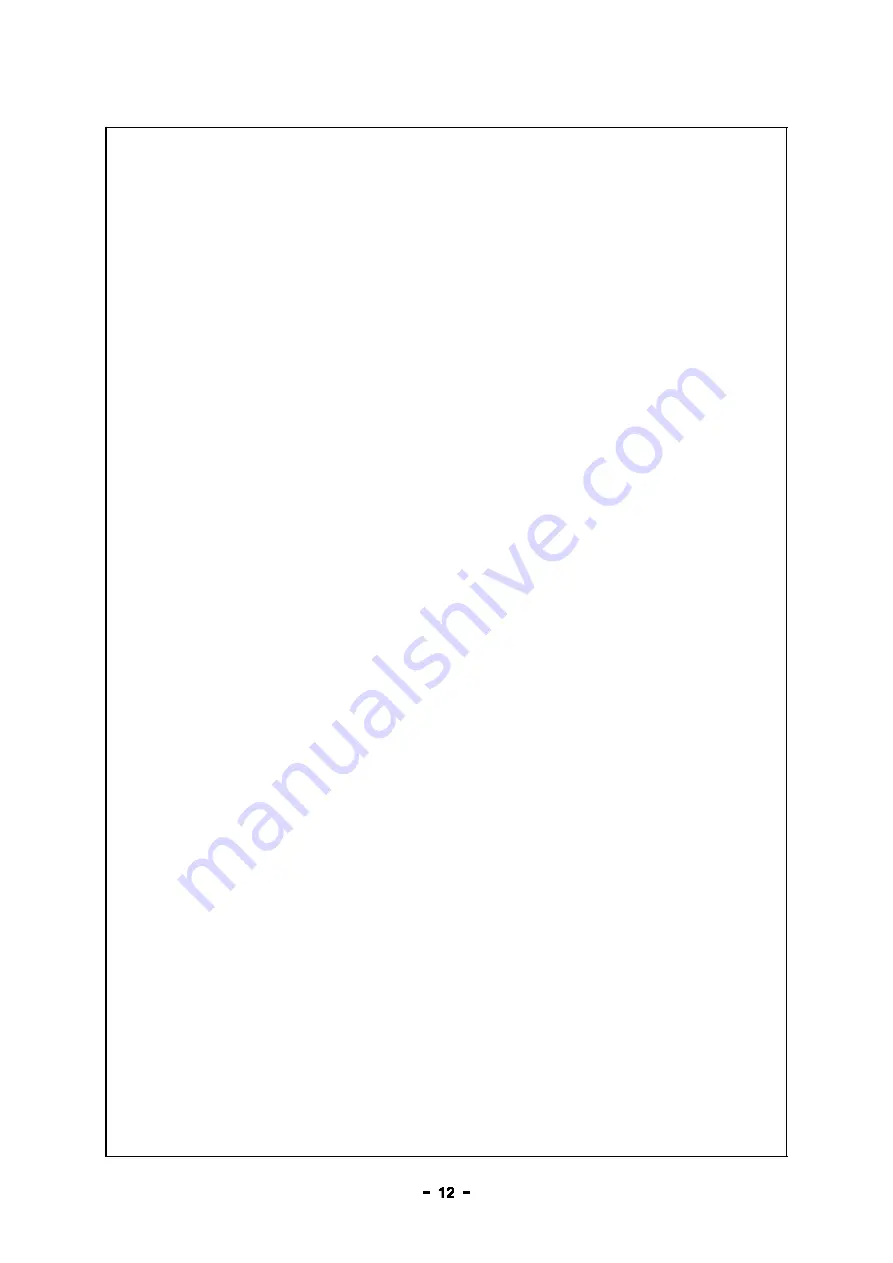
it more than enough)
3-8. 용접조작의 순서
Procedures of welding operation
팁과 모재의 간격을 약 30mm 정도로 하고
⇓
표의 와이어 인칭누름버튼스
위치를 눌러서 와이어를 모재에 접근시킨다. 와이어와 모재 사이의 철솜을
새끼손가락의 손톱정도의 크기로 둥글게 끼우고 이것을 와이어의 끝부분을
조금 찍어 누르는 듯한 정도에 멈춘다.
후럭스 호퍼 밸브를 열어서 후럭스를 와이어의 주위에 산포하면 용접준비
는 완료한다.
1) 용접개시
① 주행방향 교체레버를 전진방향으로 한다.
② 용접 선택 SW, S2, S3를 "ON"으로 한다.
③ PB5(START)을 누른다.
④ 아크가 발생하면 대차(TRAVEL)이 진행한다.
2) 용접 중
① 아크전압조정볼륨 WVC를 가감하여 적당한 아크전압으로 조정한다.
용접전류는 전류조정 누름버튼스위치(CURRENT) PB3(+) PB4(-)를
눌러서 적당한 전류에 맞춘다.
※ 직류용은 볼륨으로 조정한다.
3) 용접 종료
PB6(STOP)을 눌러 용접을 종료한다.
조작순서에 대해서는 다음 그림을 참조하여 주시기 바랍니다.
Set the tip and the parent metal about 30mm apart from each other.
Press the wire inching button switch to move the wire closer to the
parent metal. Stick the iron core in the size of the smallest fingernail
Summary of Contents for Longrun 25CA
Page 1: ...25CT CA Operation Manual...
Page 16: ...5 STOP Press the STOP button...
Page 46: ...8 Wire feeding and carriage motor driving circuit...
Page 47: ......
Page 51: ...9 Component lists 9 1 CARRIAGE MAIN BODY ASS Y...
Page 53: ...9 2 CARRIAGE DRIVING GEAR ASS Y...
Page 55: ...9 3 CARRIAGE CLUTCH ASS Y...
Page 64: ...10 DC AC Welding carriage electric wiring diagram Longrun 25CT...