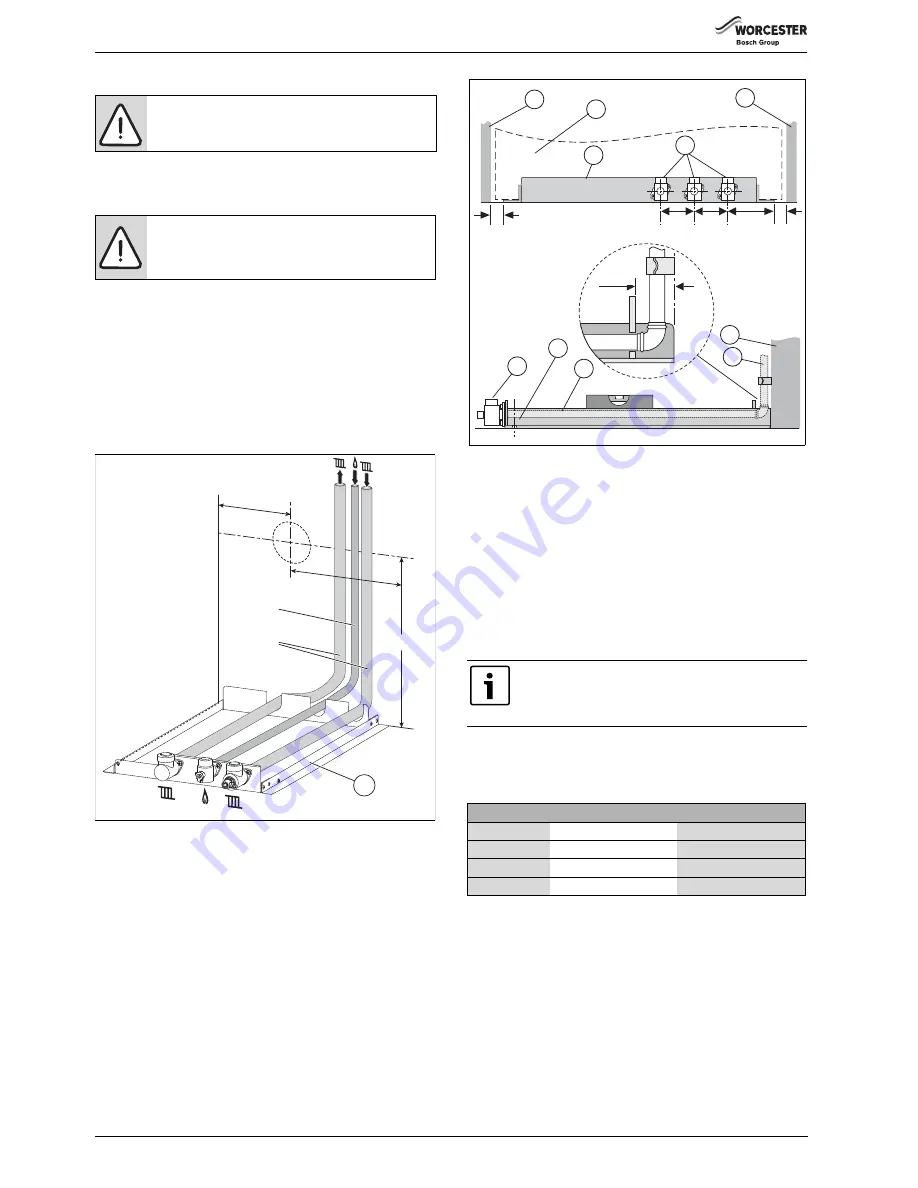
INSTALLATION
Greenstar FS CDi
ErP
6720818079 (2016/04)
20
4.2
Mounting frame fixing and flue opening
Safety
All relevant safety precautions must be undertaken. Protective clothing,
footwear, gloves and safety goggles must be worn as appropriate.
Running pipes behind the boiler:
• The frame should sit against the wall (not the skirting board) with
enough room for the pipe work.
• Do not cross a pipe over another.
• The area around a rear flue outlet must be avoided.
GAS AND WATER CONNECTIONS
▶ Ensure all pipe work is clean and each pipe is in the correct position
as shown opposite.
▶ Push in each pipe in turn and tighten the fitting to secure.
Fig. 19 Rear exit flue centre
[1]
Mounting frame
[A]
CH flow (28mm)
[B]
Gas inlet (22mm)
[C]
CH return (28mm)
Fixing the mounting frame
▶ Position the mounting frame [1] on the floor against the wall with
manifold connections [2] facing away from the wall [4] ensuring
there is enough space for the pipe work [5].
▶ Allow, at least, the minimum space from each side of the frame [1]
for the boiler overhang [6] and minimum service clearance, as
shown.
▶ Ensure the mounting frame is level and mark the fixing points [3].
▶ Secure the mounting frame [1] to the floor using appropriate fittings
(not supplied).
▶ Clear any debris away from the site.
Fig. 20 Positioning
[1]
Mounting frame.
[2]
Manifold connections.
[3]
Mounting frame fixing point.
[4]
Wall.
[5]
Gas and water pipe work (not supplied).
[6]
Boiler.
FLUE OPENING:
▶ Follow the information in figure 21 to mark the centre of the flue
[1 & 2] for rear opening, [2 & 3] for side opening or [1 & 4] for top
opening.
Measurements shown include the minimum service clearances.
▶ Cover the mounting frame manifold assembly [1] to protect the
manifold connections.
▶ Make an opening [X or Z] through the wall using a core drill or similar
at a size relative to the wall thickness as shown below:
Where the flue terminal can only be fitted from inside the building,
increase the opening to 150mmØ to allow the optional weather collar to
fit through the opening for 60/100 flue.
▶ Clear any debris away from the site.
CAUTION:
Ensure there are no pipes, electric cables,
damp proof course or other hazards before drilling.
CAUTION:
ISOLATE THE MAINS GAS SUPPLY BEFORE
STARTING ANY WORK AND OBSERVE ALL RELEVANT
SAFETY PRECAUTIONS.
C
B
A
743mm
123mm
22mm Ø
28mm Ø
247mm
6720648568-20.1W
o
1
All horizontal flue sections must rise away from the boiler
by 52mm per metre to ensure that condensate flows
back into the boiler for safe discharge via the condensate
waste pipe.
Wall thickness Flue opening 60/100 Ø Flue opening 80/125 Ø
150 - 240mm
127mmØ
152mmØ
240 - 330mm
127mmØ
152mmØ
330 - 420mm
127mmØ
162mmØ
420 - 500mm
140mmØ
162mmØ
6720648568-19.1Wo
20
65
65
1
2
20
6
4
4
70.5
38mm
3
2
1
4
5