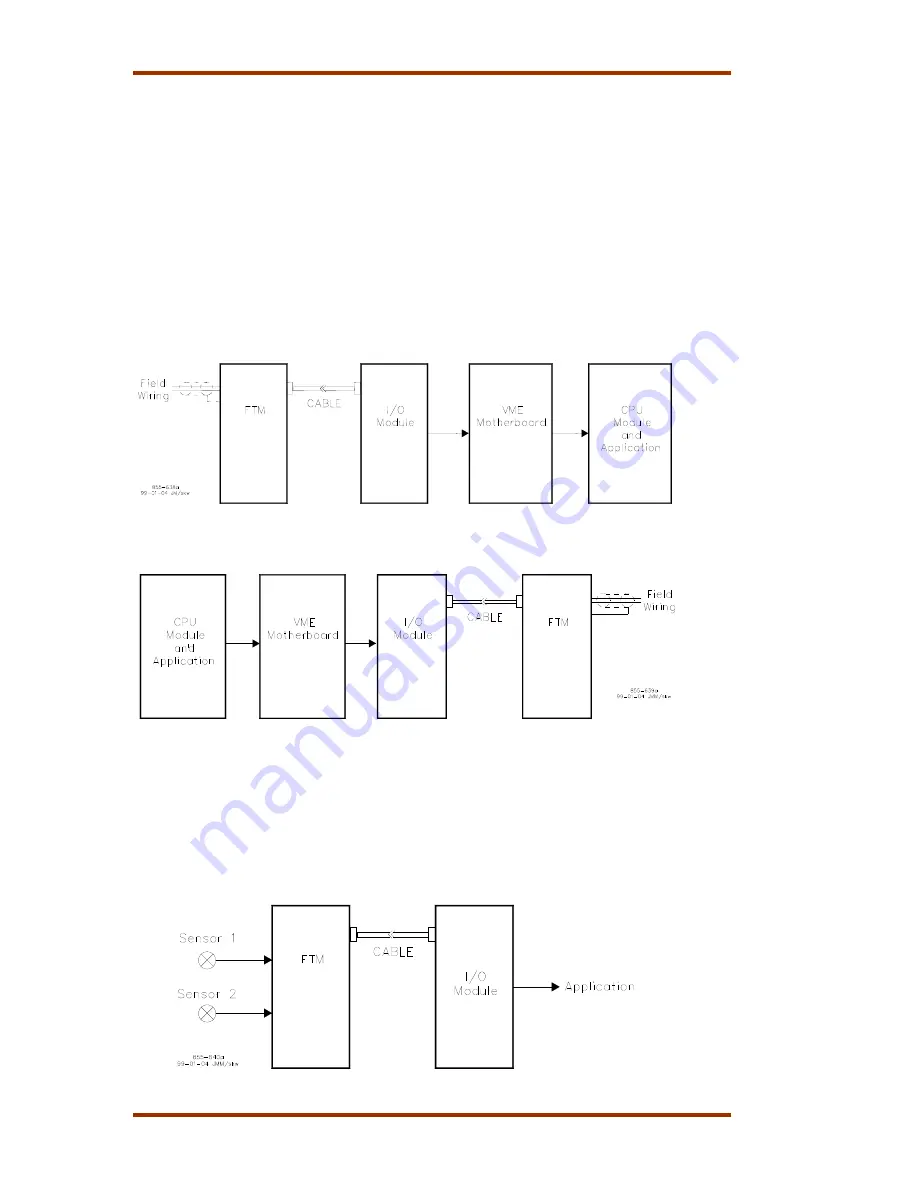
Vertex-Pro Motor-Driven Compressor Control
Manual 26489V1
4
Woodward
2.2.3—Redundant Power Supplies
Two load sharing power supplies provide redundant power to the motherboard,
CPU and I/O modules. The MicroNet Plus power supplies are 2-slot wide each and
are located at each end of the chassis in the designated PS1 and PS2 slots.
2.2.4—Simplex Inputs and Outputs
Each I/O module has connectors on the faceplate. For analog and discrete I/O,
cables connect the module to a Field Terminal module (FTM). The FTM is used to
connect to the field wiring. For communications on the CPU, FTMs are not used.
Cables are connected directly to the faceplate of the communications on the CPU.
The following diagram shows the flow of analog and discrete inputs from the field
to the application.
Figure 2-1—Input Flow
Figure 2-2—Output Flow
2.2.5—Redundant Inputs and Outputs
One level of redundancy is available. This involves wiring two external input
devices to two separate input channels. See Figure 2-3. In the event of a failed
sensor or a failure in the connection from the sensor to the control, a valid input is
still available
Figure 2-3—Redundant Sensors
Summary of Contents for Vertex-Pro
Page 10: ...Vertex Pro Motor Driven Compressor Control Manual 26489V1 viii Woodward ...
Page 103: ...Manual 26489V1 Vertex Pro Motor Driven Compressor Control Woodward 93 Appendix C Declarations ...
Page 104: ...Vertex Pro Motor Driven Compressor Control Manual 26489V1 94 Woodward ...
Page 105: ...Manual 26489V1 Vertex Pro Motor Driven Compressor Control Woodward 95 ...
Page 106: ...Vertex Pro Motor Driven Compressor Control Manual 26489V1 96 Woodward ...
Page 107: ...Manual 26489V1 Vertex Pro Motor Driven Compressor Control Woodward 97 ...
Page 111: ......