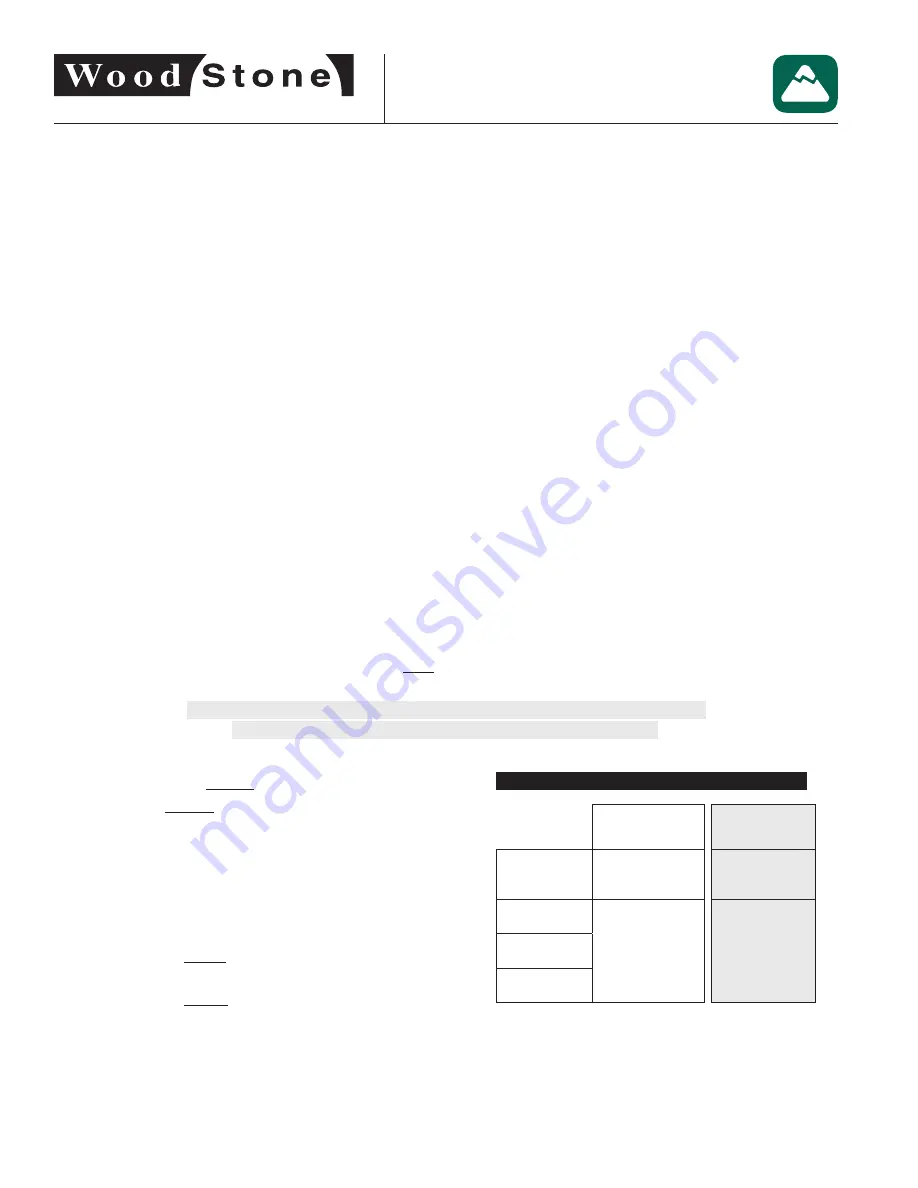
PG
18
OF
48
M0037.09 SEPTEMBER 2019
Mountain Series CE
Installation and Operation Manual
VENTING
Wood Stone ovens should be vented in accordance with pertinent national, regional and local codes concerning such appliances;
check venting plans with the authority having jurisdiction before proceeding with installation�
The above statement taking precedence, Wood Stone Corporation recommends the following two venting options:
1.
This Wood Stone Mountain Series oven can be vented as a Type A appliance (with no flue connection), designed to be installed
under an exhaust hood (canopy)� The hood must be connected to a grease-rated duct system� The venting system must be
designed and installed in accordance with all relevant codes pertaining to grease and smoke producing commercial cooking
appliances� Ovens that utilize solid fuel must be vented separately from any non-solid fuel burning appliances� There may be
requirements for interlocking the oven or its gas supply with the ventilation system� Check with your local code official� Airflow
should be adjusted according to the requirements specified by the hood manufacturer and/or local codes�
OR
2.
The oven is also approved as a Type B
11
appliance, designed to be connected directly to a chimney which is installed in
accordance with all relevant local and national codes� The chimney system must be installed and constructed to the same
requirements as a duct that serves grease and smoke producing commercial cooking appliances� If venting the oven with
this method, the oven must be vented independently of other equipment� A suitable fan should be used at the end of the duct
run to ensure proper draft in all conditions� Wood Stone does not recommend using an in-line type fan� When installed, the
fan speed/air flow should be adjusted to attain the appropriate duct pressure, or airflow rate, at the oven flue collar (see Duct
Pressure section below)�
Model numbers containing a “
-W”
(other than the first letter of the model number) should be vented in accordance with codes
concerning solid fuel appliances� Due to the dangers of creosote buildup and sparks entering the duct, these models should be
vented separately from all other kitchen equipment or in such a manner acceptable to the authority having jurisdiction�
Solid fuel exhaust contains creosote and other substances that accumulate in ducting, creating a risk of fire� The rate of
accumulation will vary with respect to flue gas temperature, wood type and moisture content� Frequent, regularly scheduled,
thorough flue cleaning is the best way to minimize the risk of flue fires�
Wood Stone recommends cleaning and inspection at least monthly on any ventilation system serving solid fuel
equipment.
WOOD STONE RECOMMENDS THAT THE OPERATOR REFER TO THE EXHAUST HOOD
MANUFACTURERS FOR INSPECTION, MAINTENANCE AND CLEANING.
AIRFLOW REQUIREMENTS (DIRECT CONNECT)
Model
RFG-W,
RFG-IR-W, W-IR
RFG, RFG-IR
WS-MS-4-CE
�20 m
3
/sec
(425 cfm)
�19 m
3
/sec
(400 cfm)
WS-MS-5-CE
�24 m
3
/sec
(500 cfm)
�21 m
3
/sec
(450 cfm)
WS-MS-6-CE
WS-MS-7-CE
DUCT PRESSURE
• For gas-fired ovens without solid fuel: 0.25 mbar (0.1"
W.C.
)
• For any oven utilizing solid fuel: 0.35 mbar (0.14"
W.C.
)
This pressure may be checked by inserting the pressure test
probe up through the oven doorway to the point where the
duct is connected to the oven flue collar�
FAN TEMPERATURE RATING
The fan must be of a suitable temperature rating�
For gas-fired ovens without solid fuel, the fan must be rated for a
minimum of 150 °C
(300 °F) continuous�
For gas-fired ovens utilizing solid fuel, the fan must be rated for a
minimum of 232 °C
(450 °F) continuous�
INTERLOCK SYSTEM
There may be requirements for interlocking the oven or its gas
supply with the ventilation system� Check with your local code
official�
Install the venting system in accordance with the
duct manufacturer’s instructions and in accordance
with all local codes� All field built components should
be built to the applicable codes and standards and
are subject to the approval of the authority having
jurisdiction�
3