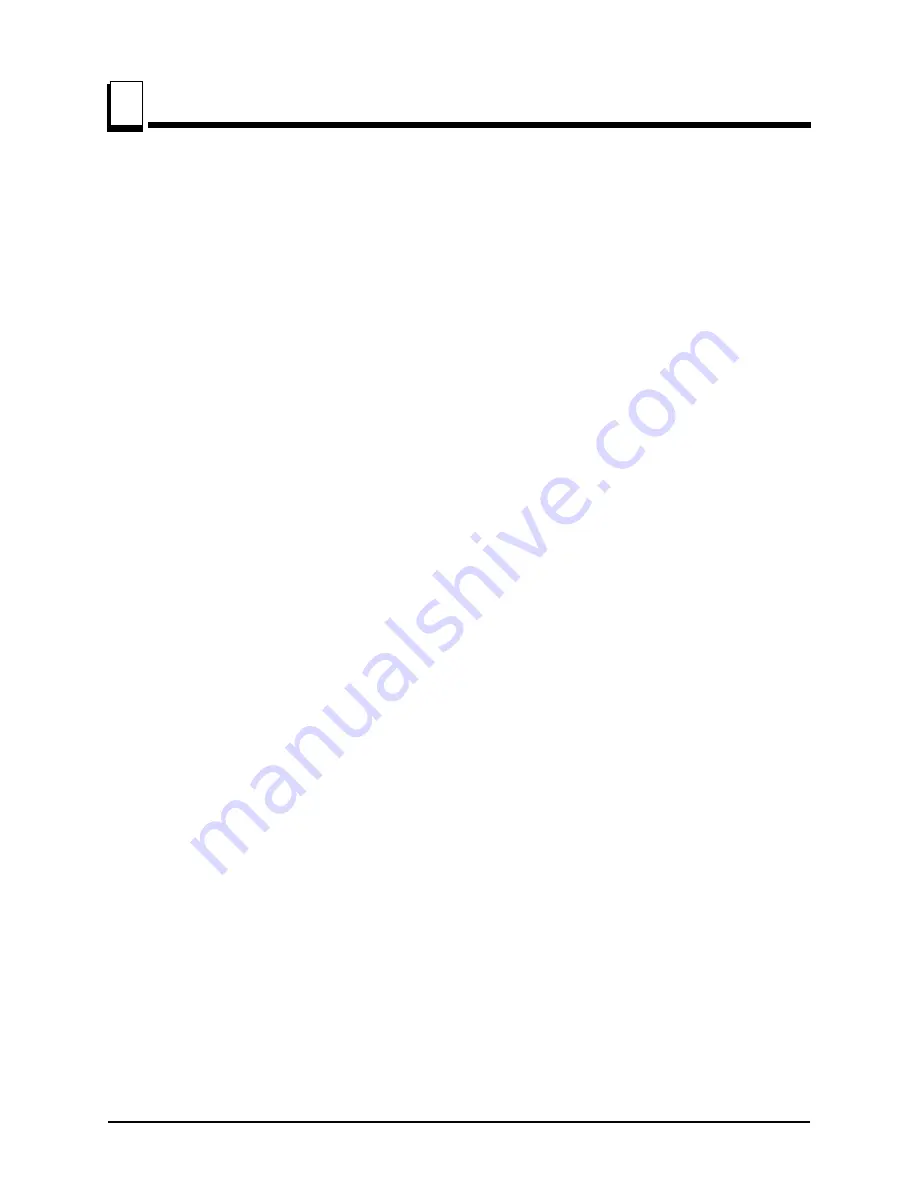
Electrical Lockout Procedures
2
2-6
WMdoc082019
Where established lockout procedures cannot be used (electrical troubleshooting or
mechanical dynamic troubleshooting), alternative effective protective techniques
shall be employed which may require special skills and planning.
Always follow safe operations practices in the workplace.
PLANER LOCKOUT PROCEDURE
Lockout procedures per OSHA regulation 1910.147, appendix A:
GENERAL
The following simple lockout procedure is provided to assist owner/operators in develop-
ing their procedures so they meet the requirements of OSHA regulation 1910.147. When
the energy isolating devices are not lockable, tagout may be used, provided the
owner/operator complies with the provisions of the standard which require additional
training and more rigorous periodic inspections. When tagout is used and the energy iso-
lating devices are lockable, the owner/operator must provide full operator protection (see
OSHA regulation 1910.147, paragraph (c)(3)) and additional training and more rigorous
periodic inspections are required. For more complex systems, more comprehensive pro-
cedures may need to be developed, documented, and utilized.
PURPOSE
This procedure establishes the minimum requirements for the lockout of energy isolating
devices whenever maintenance or servicing is done on machines or equipment. It shall
be used to ensure that the machine or equipment is stopped, isolated from all potentially
hazardous energy sources and locked out before personnel perform any servicing or
maintenance where the unexpected enervation or start-up of the machine or equipment
or release of stored energy could cause injury.
COMPLIANCE WITH THIS PROGRAM
All personnel are required to comply with the restrictions and limitations imposed upon
them during the use of lockout. The authorized personnel are required to perform the
lockout in accordance with this procedure. All operators, upon observing a machine or
piece of equipment which is locked out to perform servicing or maintenance shall not
attempt to start, energize, or use that machine or equipment.
Summary of Contents for SlabMizer MB200
Page 1: ...MB200 Operations Manual...
Page 9: ...Specifications MB200 Dimensions 1 1 6 WMdoc082019 MB200 Dimensions...
Page 31: ...Planer Assembly Install the Feed Chain 3 3 10 WMdoc082019 Planer Assembly...
Page 38: ...Planer Setup Sanding Head 4 4 7 WMdoc082019 Planer Setup...
Page 55: ...Planer Alignment Dust Head 8 8 5 WMdoc082019 Planer Alignment...