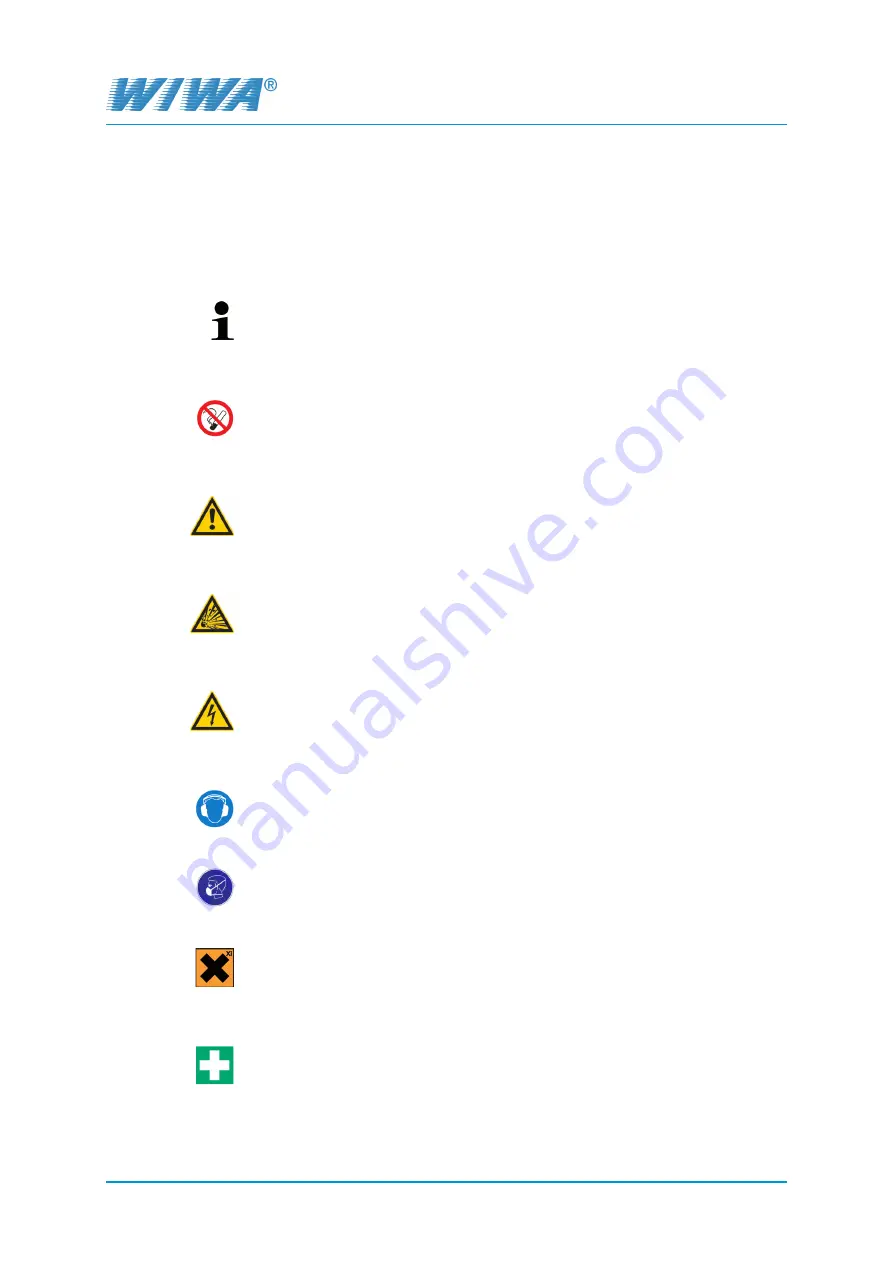
Safety
Original-Betriebsanleitung
HD1+HD2
4
•HD1-2_BAoDB_en_1407•ski
2 Safety
2.1 Description of symbols
The signs and symbols used in this User‘s Handbook have the following
meaning:
NOTE
This marks a section of text which is especially relevant to safety. Special
attention should be paid to this section and the contents strictly observed.
SMOKING PROHIBITED
This marks a situation in which a fire hazard arises through the use of
flammable or explodable solid, fluid or gaseous materials.
WARNING
This marks a situation which could be dangerous. If not observed,death or very
serious injuries could result.
DANGER OF EXPLOSION
This marks a situation, where there is danger of explosion. Observation of this
information is absolutely essential.
ELECTRICAL VOLTAGE
This marks a situation, where there is a danger of explosion through an
electostatic charge. Observation of this information is absolutely essential.
USE EAR PLUGS
For health reasons, it is very important to pay attention to this warning.
USE BREATHING PROTECTION
For health reasons, it is very important to pay attention to this warning.
HEALTH DANGER
This marks materials which are hazardous to your health.
Observation of this information is absolutely essential.
FIRST AID
In case of injuries or accidents, these instructions should be absolutely adhered
to.