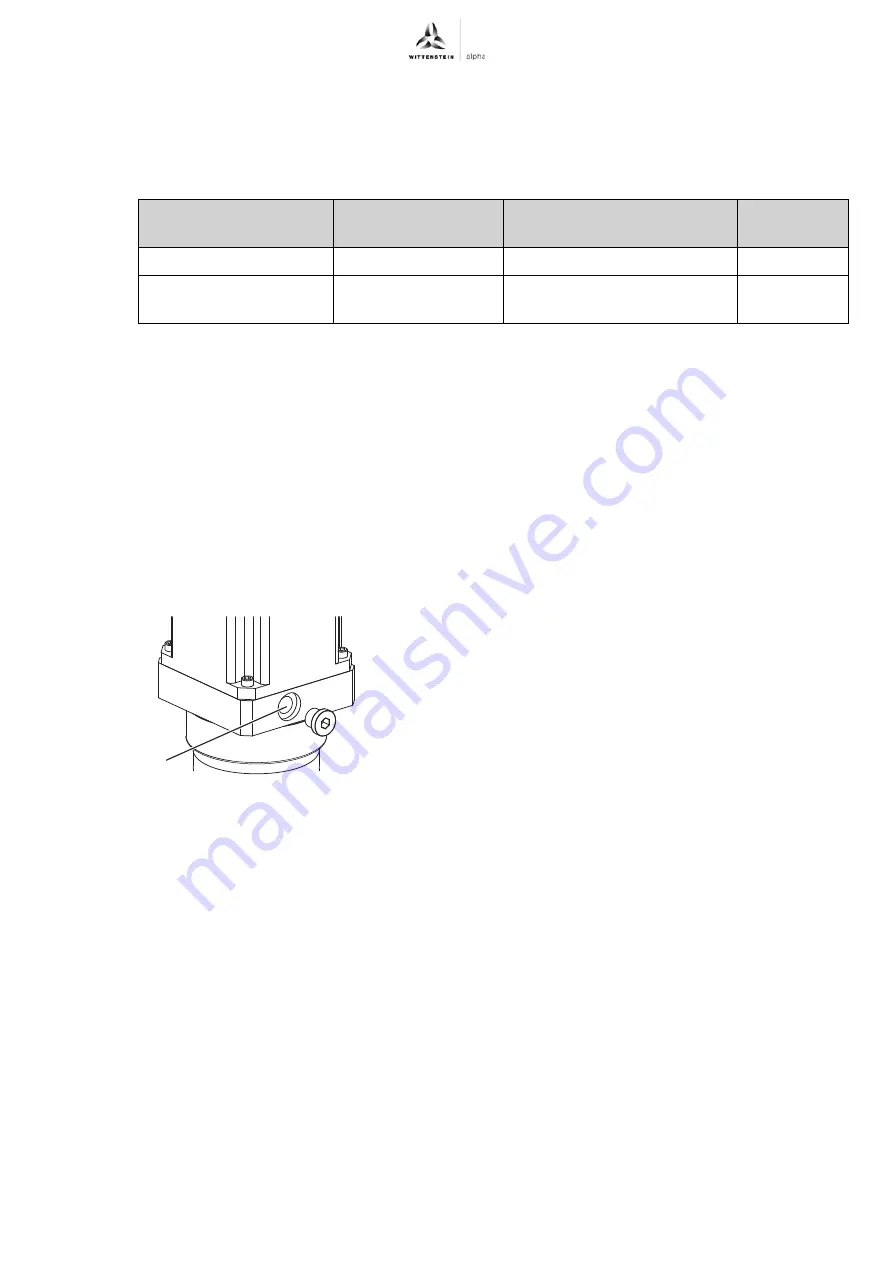
V.. / NV.. / CV..
Maintenance and disposal
Revision: 05
2022-D059517
en-21
7
Maintenance and disposal
Read the general safety instructions before beginning to work (see Chapter 2.5 "General
safety instructions").
7.1
Maintenance schedule
7.2
Maintenance work
7.2.1 Visual inspection
Check the entire gearbox for exterior damage.
Seals are subject to wear. Therefore also check the gearbox for leakage during each visual
inspection.
Check the mounting position to ensure that no foreign medium (e.g. oil) has collected on
the output shaft.
The following only applies for
corrosion-resistant
gearboxes: Check the lacquer layer and
the nickel-plated surfaces for damages and corrosion.
7.2.2 Checking the tightening torques
Screw connections between gearbox and attached component such as motors have to be
calculated, dimensioned, mounted, and tested according to current technological standards. Use
the VDI directives VDI 2862 sheet 2 and VDI 2230 for example.
The tightening torques recommended by us can be found in Chapter 9 "Appendix".
Deviating from the recommendations in Chapter 5 "Assembly", washers may be used if the material
of the screw surface features a too low interface pressure.
The hardness of the washer needs to match the property class of the screw.
Take into account the washer for the screw calculation (joint, additional compression set,
surface pressure under screw head and under washer).
7.3
Startup after maintenance work
Clean the outside of the gearbox.
Attach all safety devices.
Do a trial run before releasing the gearbox again for operation.
7.4
Disposal
Consult our Customer Service department for supplementary information on disassembly and
disposal of the gearbox.
Dispose of the gearbox at the recycling sites intended for this purpose.
Observe the applicable national regulations concerning disposal.
Maintenance work
At startup
For the first time after 500
operating hours or 3 months
Every 3
months
Visual inspection
X
X
X
Checking the
tightening torques
X
Tbl-10: Maintenance schedule
Check the tightening torque of the clamping bolt [H] on the
motor mounting. If, while checking the tightening torque, you
discover that the clamping bolt can be turned further, tighten it
to the prescribed tightening torque.
The value for the tightening torque can also be found in
Chapter 9.1 "Specifications for mounting to a motor".
H