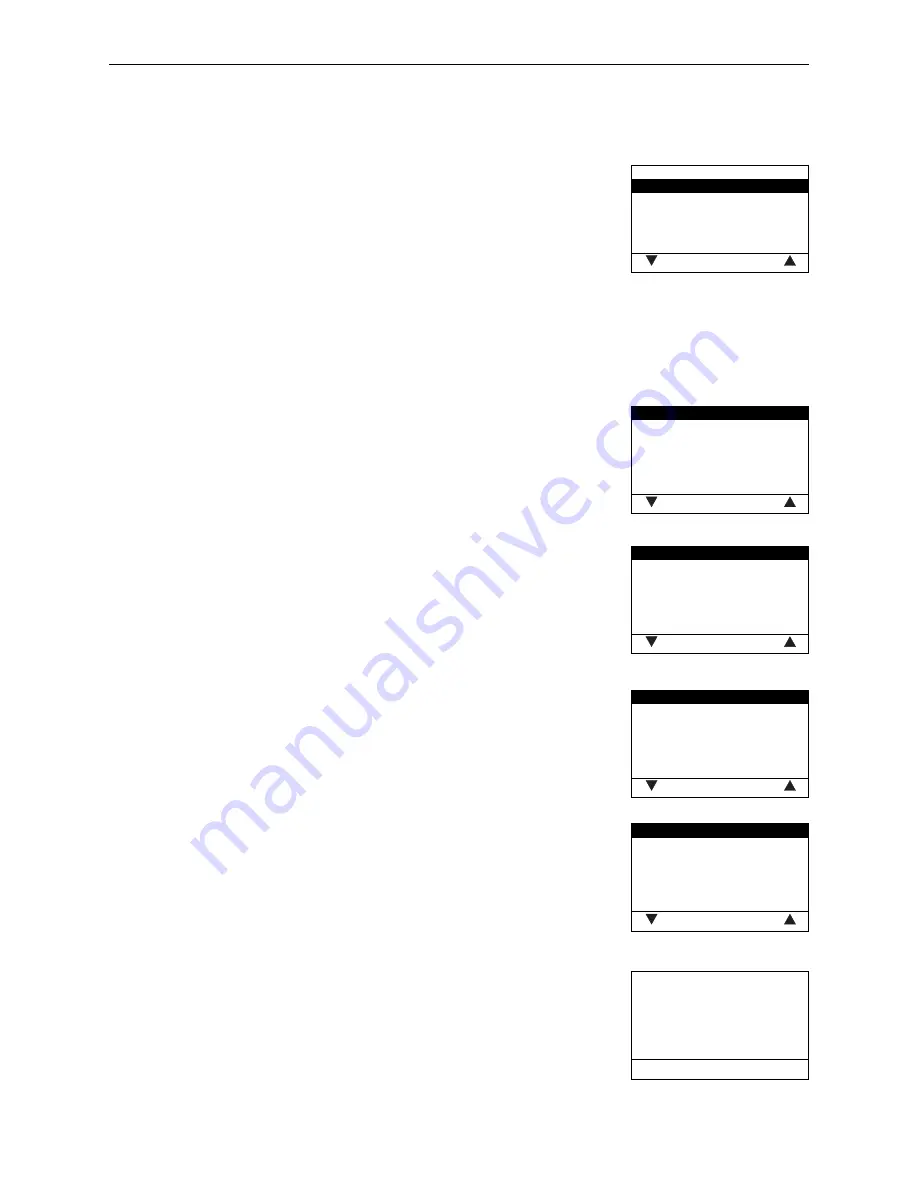
59
4.
For the Service Technician
4.4.2 Start-up
The auger conveyor and the feed can be selected on the Start-up level with the
arrow
buttons, and confirmed
using the
choose
button. A self-test is started at the end of the start-up.
Fig. 138
Start-up
Auger conveyor
Feed
choose
back
Auger conveyor
The auger conveyor can be turned on for 6 minutes.
Feed
Depending on the feed system settings, the feed and probes (including purging)
can be started.
4.4.3 Actuator test
The following actuators can be selected with the
arrow
buttons, then confirmed and started using the
choose
button. The actuators are turned off again after 1 minute. A self-test is started at the end of the actuator test.
Fig. 139
Induced draught fan
Auger conveyor
Ash removal
Ignition element
Ash conveyor
Heating surf. cleaning
choose
back
– Induced draught fan
– Auger conveyor
– Ash removal
– Ignition element
– Ash conveyor
– Heating surf. cleaning
– Suction turbine
– Probe switching
– Boiler pump
Fig. 140
Suction turbine
Probe switching
Boiler pump
choose
back
4.4.4 Settings
This sub-menu contains the following settings:
– Install display module
– Boiler no.
– Language selection
– Temperature format
– Time format
– Date format
– Weight
– Function
Fig. 141
Install display module
Boiler no.
Language selection
Temperature format
Time format
Date format
choose
back
Fig. 142
Weight
Function
choose
back
Install display module
The install display module is not needed for an individual boiler; it only needs to
be used for a cascade system.
Fig. 143
Start installation procedure
Please press LON button on auto-
matic firing device briefly
back