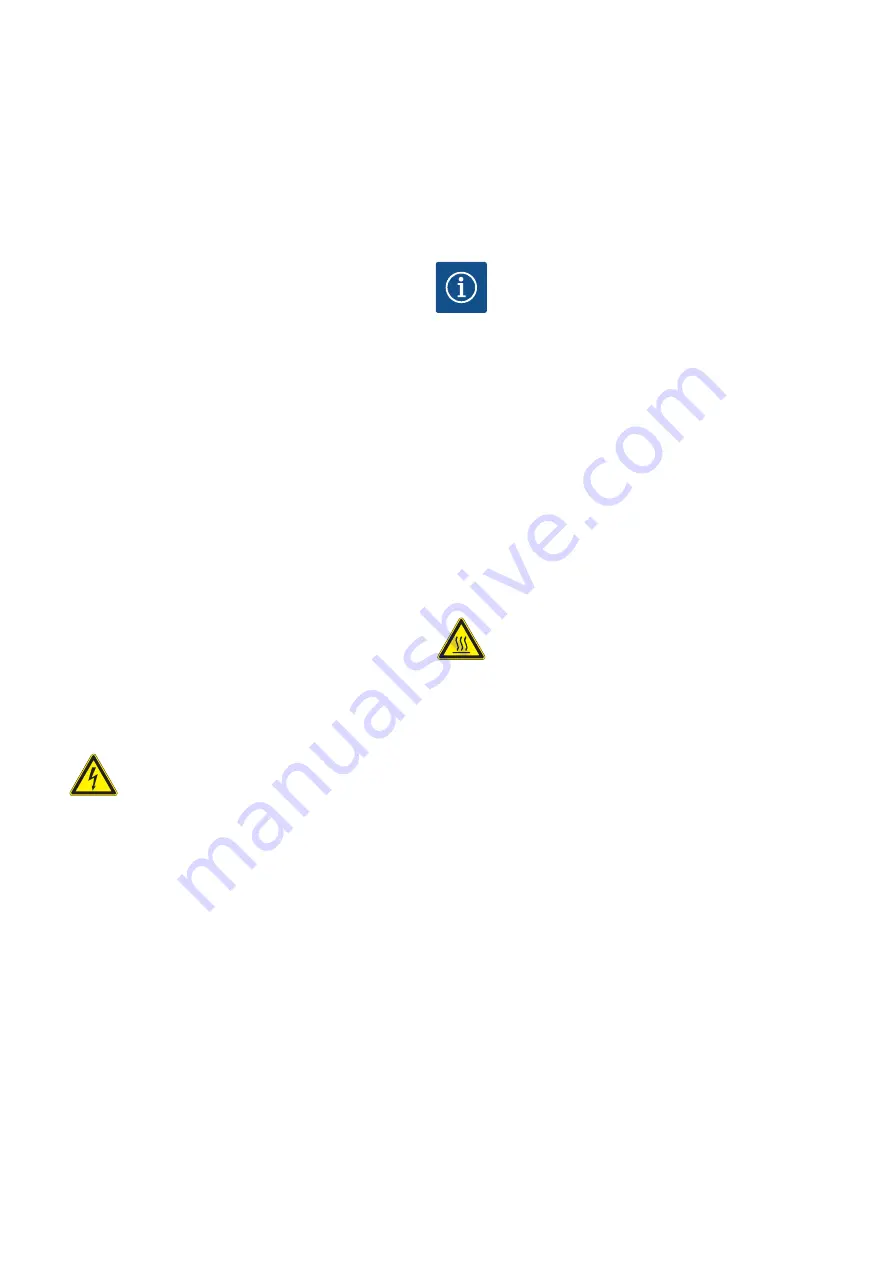
14
WILO SE 04/2021 DIN A4
English SAFETY
•
When welding and/or working with electrical
devices, make sure there is no risk of explosion.
•
Only use lifting gear which is legally designated as
such and officially approved.
•
The lifting gear must be suitable for the condi-
tions of use (weather, hooking unit, load etc.).
•
Mobile equipment for lifting loads should be
used in such a way that it is guaranteed to remain
stable during operation.
•
When using mobile equipment for lifting non-
guided loads, take action to prevent tipping,
shifting, sliding etc.
•
Measures should be taken to ensure that no
person is ever directly beneath a suspended load.
Furthermore, it is prohibited to move suspended
loads over workplaces where people are present.
•
If mobile equipment is used for lifting loads, a
second person should be present to coordinate
the procedure if required (e.g. if the operator’s
field of vision is blocked).
•
The load to be lifted must be transported so that
no-one will be injured if there is a power failure.
Furthermore, if such work is being performed
outdoors, it must be cancelled if the weather
conditions worsen.
These instructions must be strictly observed.
Non-observance can result in personal injury
and/or substantial material damage.
2.5. Drive
The pump is driven by a standard IEC motor. The
connection between the motor and hydrau-
lics is achieved by means of a coupling. See the
technical data for the performance data (e.g.
size, construction, hydraulic rated power, speed)
needed to select a motor.
2.6. Electrical work
DANGER due to electrical current!
Incorrectly performed electrical work can
result in fatal injury! This work may only be
performed by a qualified electrician.
The motor must be connected in accordance with
the information in the operating and maintenance
manual for the motor. The governing local direc-
tives, standards and regulations (e.g. VDE 0100)
as well as the requirements of the local energy
supply company must be observed.
The person operating the motor must know
where it is supplied with power and how to cut
off the supply. A motor protection switch must
be installed on-site. It is advisable to install a
residual-current device (RCD). If there is a pos-
sibility that people can come into contact with
the motor and the fluid, the connection
must
be equipped with an additional residual-current
device (RCD).
The hydraulics must always be earthed. In a
standard system, the hydraulics are earthed
through the motor’s connection to the mains.
Alternatively, the hydraulics can be earthed
through a separate connection.
2.7. Safety and monitoring devices
CAUTION!
Never operate the pump if the built-on
monitoring devices have been removed or
damaged and/or if they do not work!
NOTICE
Also note all the information in the operating
and maintenance manual for the motor!
•
The hydraulics are not fitted with monitoring
devices as standard.
Optionally, the sealing chamber can be monitored
with an external pencil electrode.
•
In the version as a unit (pump with motor and
coupling mounted on baseplate), a contact guard
is attached to the coupling.
All existing safety and monitoring devices
must be installed, connected and checked to
ensure that they function correctly before
commissioning.
The personnel must be informed about the
installed systems and how they work.
2.8. Conduct during operation
CAUTION! Risk of burns!
The housing parts can heat up to well above
40 °C. There is a risk of burns!
• Never touch parts of the housing with your
bare hands.
• After switching the pump off, let it cool down
to ambient temperature first.
• Wear heat-resistant protective gloves.
During pump operation, always follow the locally
applicable laws and regulations for work safety,
accident prevention and handling electrical
machinery. To help ensure safe working prac-
tice, the responsibilities of employees should be
clearly specified by the operator. All personnel
are responsible for ensuring that regulations are
observed.
During operation, all gate valves in the inlet line
and pressure pipe must be completely open.
If the slide valves on the suction and discharge
sides are closed during operation, the fluid
in the hydraulics housing is heated up by the
pumping movement. This heating creates
strong pressure in the hydraulics housing. The
pressure can result in the pump exploding!
Before switching on the hydraulics, ensure that
all the slide valves are open and open any closed
slide valves if necessary.
2.9.
Pumped fluids
Each fluid differs in respect of composition, cor
-
rosiveness, abrasiveness, dry matter content and
in many other aspects. Generally, the pumps can
Summary of Contents for Wilo-Rexa NORM
Page 2: ...Fig 2 Fig 1 A B 8 9 10 2 4 4 7 5 5 3 1 2 7 1 6 3 6...
Page 3: ...Fig 3B Fig 3A 1...
Page 4: ...Fig 4 8 2 4 7 5 3 1 6 Fig 5 1 Rexa NORM M15 77 2140 1400 370 790 860 370 36 29...
Page 7: ...Fig 7 Fig 6 A A A A 2 4 4 5 5 5 5 5 5 3 1 S1 S1 X X Y Y Z Z Fz Mz My Mx Fy Fx...
Page 8: ...Fig 9 Fig 8 2 3 1 2 4 5 3 1...
Page 9: ...Fig 11 Fig 10 F2 F1 M1 M2...
Page 10: ...Fig 13 Fig 12 D D L...
Page 30: ......
Page 31: ......