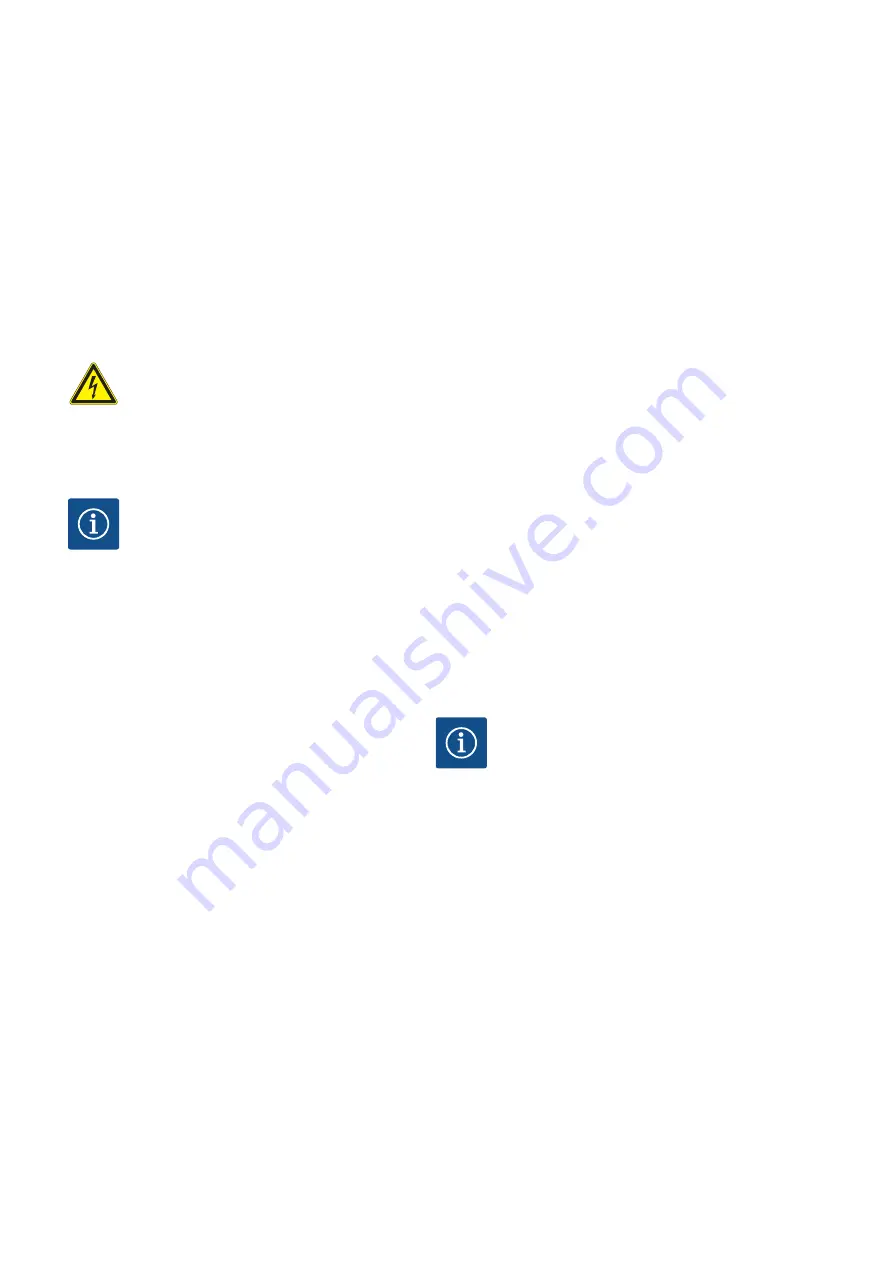
22
WILO SE 04/2021 DIN A4
English COMMISSIONING
9. Install coupling
» see instructions from the
manufacturer
10. Install the coupling guard
-
Place the coupling guard from above over the
coupling on the baseplate and fasten it to the
baseplate with the screws.
-
Insert the floor plate into the coupling guard
from below and fasten it to the coupling guard
with the screws.
5.6. Install, remove and align the coupling
All information regarding the coupling can be
found in the manufacturer’s instructions!
5.7. Electrical connection
RISK of fatal injury due to electrical current!
Improper electrical connections can lead to
fatal electric shock. Electrical connections
may only be carried out by a qualified elec
-
trician approved by the local energy supply
company, in accordance with locally applica-
ble regulations.
NOTICE
Also note all the information regarding electrical
connections in the operating and maintenance
manual for the motor!
•
The current and voltage of the mains connection
must be designed in accordance with the infor-
mation in the operating and maintenance manual
for the motor. See also the specifications on the
rating plate for the motor.
•
The power supply cable must be provided by the
customer. The cable cross-section and chosen
routing option must comply with local standards
and requirements.
•
Any available monitoring devices, e.g. sealing
chamber monitoring, must be connected and
tested to ensure that it is working properly.
•
Earth the pump in accordance with instructions.
Earthing is provided by the motor connection.
Alternatively, the pump can be earthed through a
separate connection. The cable cross-section for
the protective earth conductor connection must
comply with local regulations.
5.7.1. Checking the monitoring devices before
connecting
If the measured values deviate from the speci-
fications, the monitoring devices may be faulty.
Consult the Wilo customer service.
Pencil electrode for sealing chamber monitoring
Before the pencil electrode is connected, it must
be checked with an ohmmeter. The following
values must be complied with:
-
This value must approach “infinity”. If the
values are low, there is water in the oil. Please
also observe the instructions of the optional
evaluation relay.
5.7.2. Connecting the monitoring devices
Pencil electrode for sealing chamber monitoring
•
The pencil electrode must be connected via an
evaluation relay. We recommend the “NIV 101/A”
relay for this. The threshold is 30 kOhm. When the
threshold is reached, a warning must be given, or
the unit must be switched off.
CAUTION!
If there is only a warning, the hydraulics could
be irreparably damaged by water ingress. We
always recommend switching the hydraulics
off!
5.7.3. Connecting the standard motor
The information for connecting the motor to
the mains, the information concerning existing
monitoring devices and connecting these devices,
and concerning possible activation types can be
found in the operating and maintenance manual
for the motor!
5.8. Operator responsibilities
5.8.1. Recommended monitoring devices
The pump is driven by a standard motor. Stan-
dard motors are not overflow-proof. We therefore
recommend using an alarm switchgear to record
major leakages. In the event of a major discharge
of fluid (e.g. faulty piping), an alarm may sound,
and the motor can be switched off.
6. Commissioning
NOTICE
Also note all the information regarding com-
missioning in the operating and maintenance
manual for the motor!
The “Commissioning” section contains all of the
important instructions for the operating person-
nel for safe commissioning and operation of the
pump.
The following points must be observed:
•
All work may only be carried out by qualified and
trained personnel.
•
All personnel working on or with the pump must
have received, read and understood this manual.
•
Always keep this manual either at the pump or in
a place specially reserved for it, where it is acces-
sible for all operating personnel at all times.
•
All safety devices and emergency cut-outs are
connected and have been checked to ensure that
they work properly.
Summary of Contents for Wilo-Rexa NORM
Page 2: ...Fig 2 Fig 1 A B 8 9 10 2 4 4 7 5 5 3 1 2 7 1 6 3 6...
Page 3: ...Fig 3B Fig 3A 1...
Page 4: ...Fig 4 8 2 4 7 5 3 1 6 Fig 5 1 Rexa NORM M15 77 2140 1400 370 790 860 370 36 29...
Page 7: ...Fig 7 Fig 6 A A A A 2 4 4 5 5 5 5 5 5 3 1 S1 S1 X X Y Y Z Z Fz Mz My Mx Fy Fx...
Page 8: ...Fig 9 Fig 8 2 3 1 2 4 5 3 1...
Page 9: ...Fig 11 Fig 10 F2 F1 M1 M2...
Page 10: ...Fig 13 Fig 12 D D L...
Page 30: ......
Page 31: ......