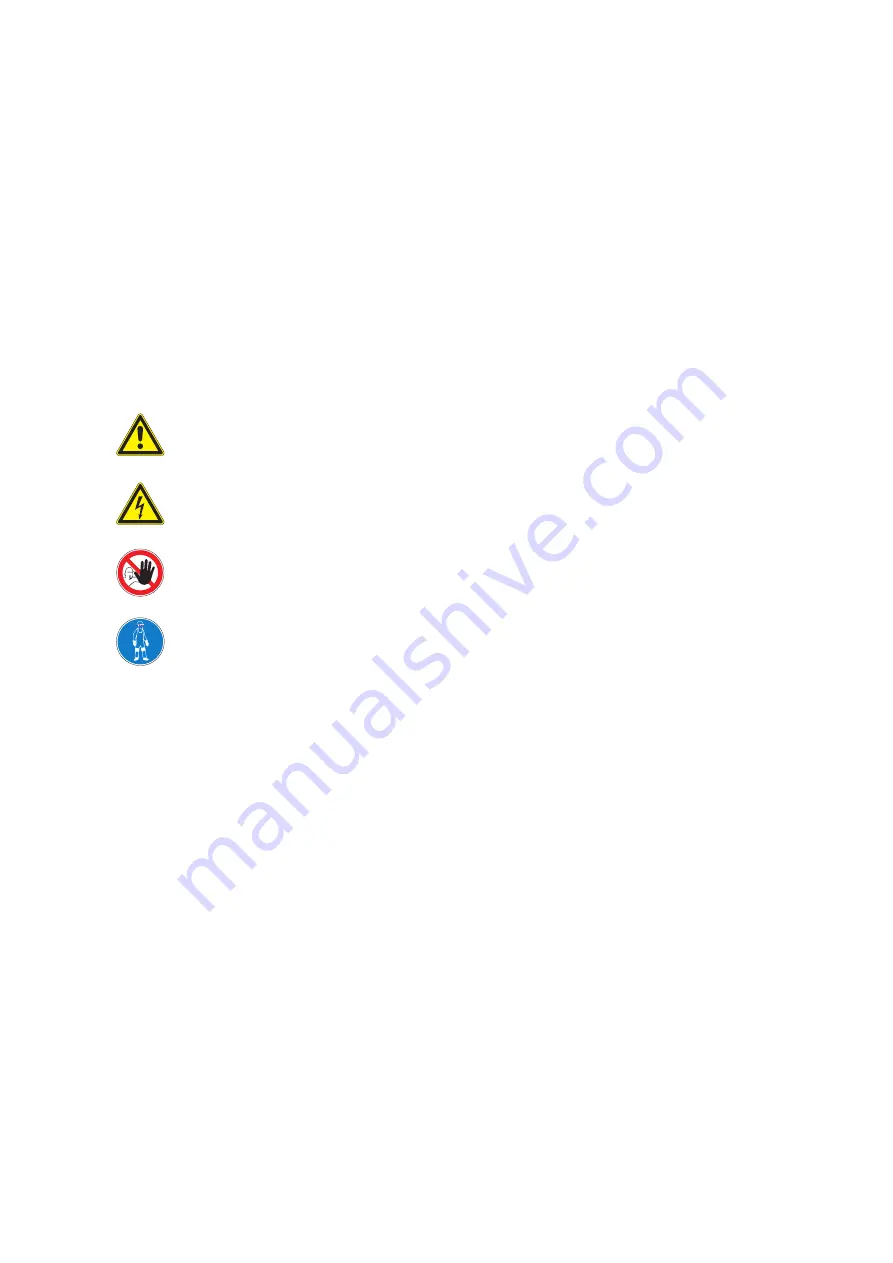
Installation and operating instructions Wilo-Rexa NORM 13
SAFETY English
•
Instructions appear in “bold” and refer directly to
the preceding text or section.
•
Safety instructions are slightly “indented and
bold” and always start with a signal word.
-
Danger
Serious or fatal injuries can occur!
-
Warning
Serious injuries can occur!
-
Caution
Injuries can occur!
-
Caution
(notice without symbol)
Substantial material damage can occur. Irrepara-
ble damage is possible!
•
Safety instructions that refer to personal injury
appear in black and are always accompanied by a
safety symbol. Danger, prohibition or instruction
symbols are used as safety symbols.
Example:
Danger symbol: general hazard
Danger symbol, e.g. electrical current
Symbol for prohibited action, e.g. “No entry!”
Instruction symbol, e.g. “Wear protective
clothing.”
The safety symbols used conform to the generally
applicable directives and regulations, such as
DIN, ANSI.
•
Safety instructions that only refer to material
damage are printed in grey, without safety sym-
bols.
2.2.
Personnel qualifications
Personnel must:
•
Be instructed about locally applicable regulations
governing accident prevention.
•
Have read and understood the installation and
operating instructions.
•
Personnel must have the following qualifications:
-
Electrical work must be carried out by a quali-
fied electrician (in accordance with EN 50110-
1).
-
Installation/dismantling must be carried out by
a qualified technician who is trained in the use
of the necessary tools and fixation materials.
-
Maintenance work must be carried out by a
technician who is familiar with handling and
disposing of the operating fluids used. In addi
-
tion, the technician must have basic knowledge
of mechanical engineering.
Definition of “qualified electrician”
A qualified electrician is a person with appropriate
technical education, knowledge and experience
who can identify and prevent electrical hazards.
2.3. Operator responsibilities
The operator must:
•
Provide the installation and operating instructions
in a language which the personnel can under-
stand.
•
Make sure that personnel are suitably trained for
the specified work.
•
Ensure that safety and information signs mounted
on the device are always legible.
•
Train personnel with regard to the operating
principles of the system.
•
Eliminate any risk from electrical current.
•
Integrate the pump into the existing safety con-
cept and ensure that the pump can be switched
off in an emergency using the existing safety
shutdowns.
•
Ensure the standard motor is deactivated in the
event of high water. Standard motors are not
overflow-proof! We therefore recommend using
an alarm switchgear to record major leakages. In
the event of a major discharge of fluid (e.g. faulty
piping), the motor can be switched off.
•
Equip hazardous components (extremely cold,
extremely hot, rotating etc.) with a guard to be
provided by the customer.
•
Demarcate and cordon off the hazardous area.
•
Define personnel responsibilities to ensure safe
working practice.
Children and persons younger than 16 years
or with reduced physical, sensory or mental
capacities or limited experience are prohibited
from handling the device! Persons under the
age of 18 must be supervised by a technician!
2.4. General safety information
•
Do not work alone in closed rooms when installing
and/or removing the pump. A second person must
always be present for safety reasons.
•
Sufficient ventilation must be provided when
working in enclosed spaces.
•
The pump must always be switched off before
any work is performed on it (assembly, disman-
tling, maintenance, installation). The drive must
be disconnected from the electrical system and
secured against being switched on again. All
rotating parts must have come to a standstill.
•
The operator must report any faults or irregulari-
ties that occur to a line manager immediately.
•
The operator must shut down the equipment
immediately if defects occur that represent a
safety risk. These include:
-
Failure of the safety and/or monitoring devices
-
Damage to important parts
-
Damage to electrical equipment, cables and
insulation
•
Tools and other objects should only be kept in
their designated places so that safe operation is
ensured.
Summary of Contents for Wilo-Rexa NORM
Page 2: ...Fig 2 Fig 1 A B 8 9 10 2 4 4 7 5 5 3 1 2 7 1 6 3 6...
Page 3: ...Fig 3B Fig 3A 1...
Page 4: ...Fig 4 8 2 4 7 5 3 1 6 Fig 5 1 Rexa NORM M15 77 2140 1400 370 790 860 370 36 29...
Page 7: ...Fig 7 Fig 6 A A A A 2 4 4 5 5 5 5 5 5 3 1 S1 S1 X X Y Y Z Z Fz Mz My Mx Fy Fx...
Page 8: ...Fig 9 Fig 8 2 3 1 2 4 5 3 1...
Page 9: ...Fig 11 Fig 10 F2 F1 M1 M2...
Page 10: ...Fig 13 Fig 12 D D L...
Page 30: ......
Page 31: ......