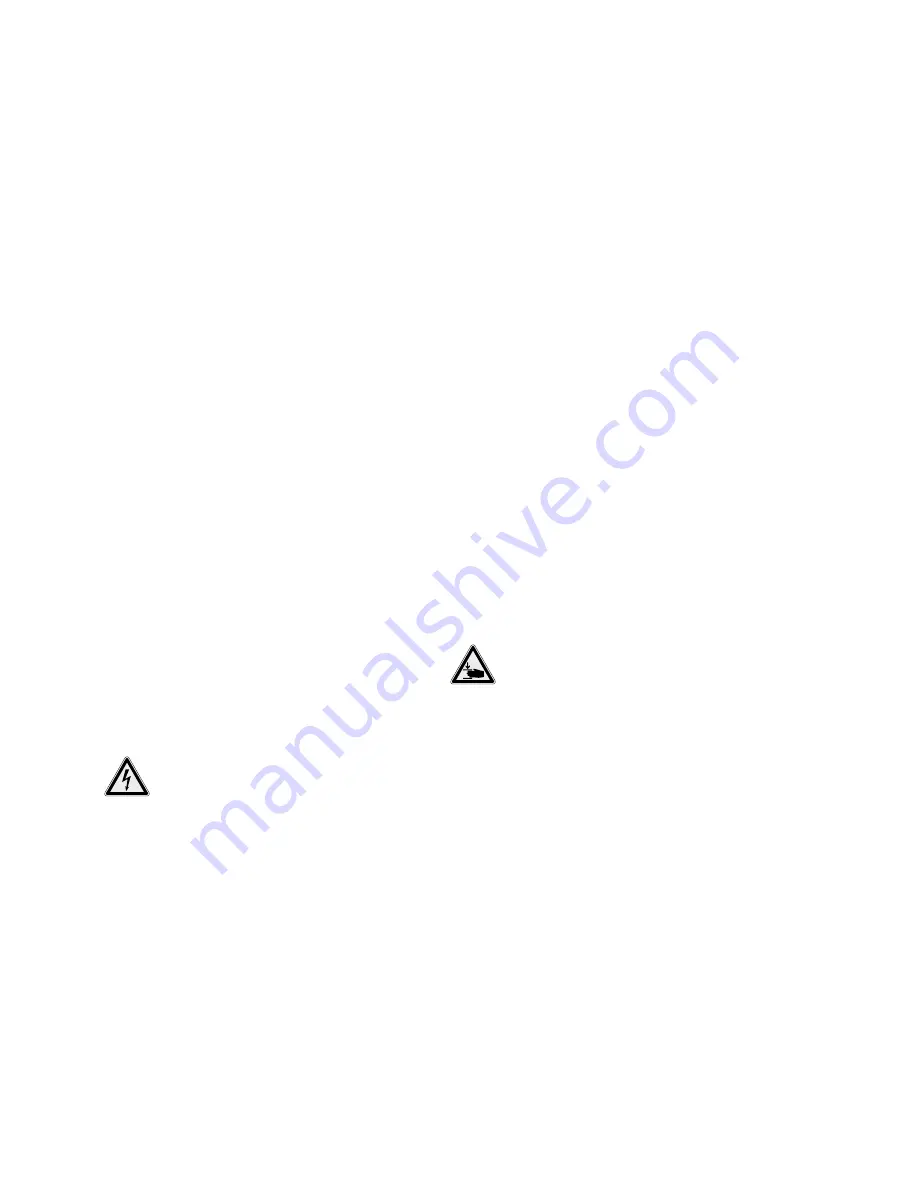
42
WILO SE 10-2014 V05 DIN A4
English
COMMISSIONING
Always keep this manual either by the pump
or in a place specially reserved for it, where it is
accessible for the entire operating personnel at
all times.
In order to prevent damage or serious injury when
commissioning the pump, the following points
must be observed:
• Commissioning of the pump may only be carried
out by qualified and trained personnel in accord
-
ance with the safety instructions.
• All persons working on or with the pump must
have received, read and understood this operating
and maintenance manual.
• All safety devices and emergency cut-outs must
be connected and checked to ensure that they
work properly.
• Electrical engineering and mechanical adjust-
ments must be made by qualified personnel.
•
The pump is suitable for use under the specified
operating conditions.
•
The work area of the pump is not a recreational
area and is to be kept free of people! No persons
are allowed in the work area during start-up or
operation.
•
When working in sumps, a second person must be
present for safety reasons. Adequate ventilation
must be ensured if there is danger of poisonous
gases forming.
6.1. Electrical system
Connect the pump and install the power supply
cables as described in the “Installation” section
and in accordance with the VDE guidelines and
applicable national regulations.
The pump must be properly protected and
grounded.
Observe the direction of rotation. If the direction
of rotation is incorrect, the pump will not perform
as specified and may be damaged.
Make sure all monitoring devices are connected
and have been tested.
ELECTRICAL hazard!
Electrical current can cause fatal injuries if not
handled correctly! All pumps with free cable
ends (i.e. without plugs) must be connected
by a qualified electrician.
6.2. Rotation control
The pump is checked and adjusted in the factory
to ensure that the direction of rotation is correct.
The connection must be made according to the
wiring labels.
A test run must be performed under general op-
erating conditions!
6.2.1. Checking the direction of rotation
The direction of rotation must be checked with
a rotating field tester by a local electrician. For the
correct direction of rotation, a clockwise rotating
field must be available.
The pump is not approved for operation with
a counter-clockwise rotating field!
6.2.2. If the direction of rotation is incorrect
If the direction of rotation is incorrect for direct
start motors, 2 phases must be swapped. In the
case of star-delta motors, the connections of two
windings must be swapped, e.g. U1 with V1 and
U2 with V2.
6.3. Level control
Check the level control device for the following
points:
•
The float switch must be able to move freely!
•
The water level must not fall below the minimum!
•
The maximum switching frequency may not be
exceeded!
When using a separate level control device,
check to ensure it has been installed properly and
inspect the switching points. For the required
information please refer to the installation and
operating instructions for the level control device,
as well as the planning documentation.
6.4. Commissioning
The pump must have been installed properly as
specified in the "Installation" chapter. This must
be checked before the system is switched on.
Minor oil leakage in the mechanical shaft seal on
delivery is no cause for concern. However, it must
be removed prior to submersion in the fluid.
Keep out of the pump's work area. No persons
are allowed in the work area during start-up or
operation.
If the pump falls over, it must be switched off
before setting it up again.
WARNING: Danger of crushing!
In portable installations, the pump can fall
over when it is switched on or during opera-
tion. Make sure that the pump is positioned
on a firm bearing surface and that the pump
foot is mounted correctly.
In the version with a plug, note the plug's IP pro
-
tection class.
6.4.1. Before switching on
•
Check the following, in general:
• Cable guidance – no loops, slightly taut
•
Min./max. temperature of the fluid
•
Max. immersion depth
• Clean the pipe system on the pressure side
(hose, piping) – flush with clean water to pre
-
vent deposits forming clogging.
•
The hydraulics housing must be completely
filled by the fluid and there must be no air in
the housing. It can be vented by suitable vent-
ing devices in the system or, if available, using
vent screws on the pressure port.
• Check switching points of level control and
dry-running protection systems
• Check to ensure all accessories are properly
fitted
•
The following points must also be checked for
wet well installation: