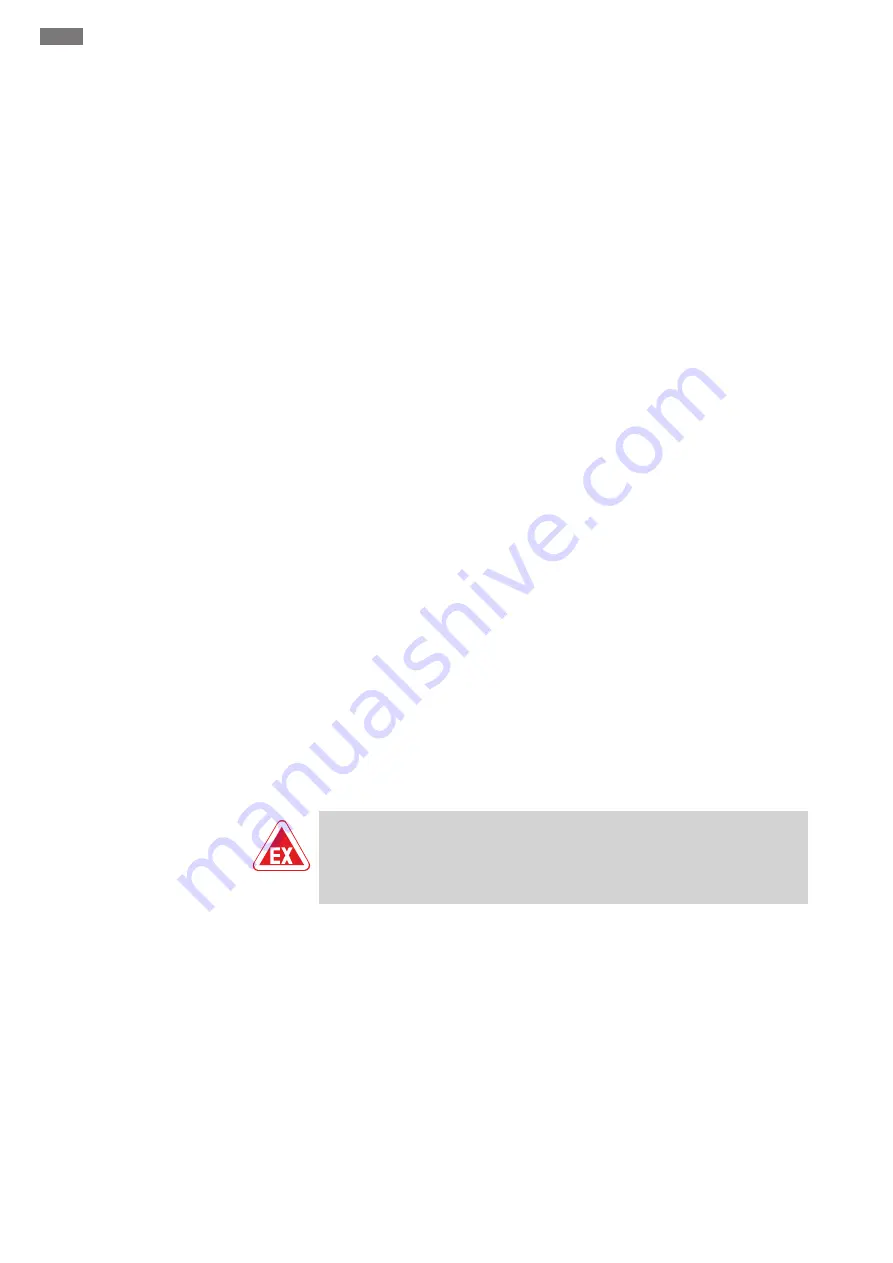
en
Appendix
46
WILO SE 2021-05
Once the trigger temperature for the low temperature is reached, the motor can de-
activate with automatic reactivation. Upon reaching the trigger temperature for the
high temperature limit, the motor must deactivate with manual
anti-reactivation
lock
!
CAUTION! Motor damage due to overheating! In the event of automatic reactiva-
tion, comply with the specifications for the maximum switching frequency and
switching break!
Connection of the thermal motor monitoring
ƒ
Connect the bimetallic strip using an evaluation relay. "CM-MSS" relay is recommen-
ded for this purpose.
Connection values: max. 250 V(AC), 2.5 A, cos φ = 1
ƒ
Connect the PTC sensor via an evaluation relay. "CM-MSS" relay is recommended for
this purpose.
ƒ
If a frequency converter is used, connect the temperature sensor at the Safe Torque
Off (STO). This guarantees that the hardware deactivates the pump.
13.3.4.2 Pre-chamber monitoring (external
electrode)
ƒ
Connect the external pencil electrode via an Ex-rated evaluation relay! Relay
“XR-4…” is recommended for this.
The threshold is 30 kOhm.
ƒ
The connection must be made using an intrinsically safe circuit!
13.3.4.3 Frequency converter operation
ƒ
Converter type: Pulse-width modulation
ƒ
Min./max. frequency during continuous duty:
–
Asynchronous motors: 30 Hz up to rated frequency (50 Hz or 60 Hz)
–
Permanent magnet motors: 30 Hz up to the stated maximum frequency as per
rating plate
NOTICE! The maximum frequency may be below 50 Hz!
ƒ
Min. switching frequency: 4 kHz
ƒ
Max. overvoltage at the terminal board: 1350 V
ƒ
Output current at the frequency converter: max. 1.5 times rated current
ƒ
Max. overload time: 60 s
ƒ
Torque applications: quadratic pump curve or automatic energy optimisation pro-
cedure (e.g. VVC+)
Required speed/torque curves are available on request!
ƒ
Observe additional measures with regard to EMC regulations (choice of frequency
converter, filters, etc.).
ƒ
Do not exceed the rated current or rated speed of the motor.
ƒ
It must be possible to connect the motor’s own temperature monitoring (bimetallic
strip or PTC sensor).
ƒ
If the temperature class is marked as T4/T3, temperature class T3 applies.
13.3.5
Commissioning
DANGER
Risk of explosion when using non-Ex-rated mixers!
Risk of fatal injury due to explosion! Only use mixers which have Ex labelling on the
rating plate within potentially explosive areas.
ƒ
The operator is responsible for defining the potentially explosive area.
ƒ
Only Ex-rated mixers may be used within potentially explosive areas.
ƒ
Mixers with an Ex rating must be labelled as such on the rating plate.
ƒ
Do not exceed the
max. fluid temperature
!
ƒ
According to DIN EN 50495, a safety device with SIL level 1 and hardware fault toler-
ance 0 must be provided for category 2.
13.3.6
Maintenance and repair
ƒ
Carry out maintenance tasks according to the regulations.
ƒ
Only carry out maintenance tasks described in these installation and operating in-
structions.
ƒ
The spark-proof gaps must
only
be repaired according to the manufacturer’s design
specifications. Carrying out repairs according to the values in tables 1 and 2 of DIN
EN 60079-1 is
not
permitted.
ƒ
Only use screws as stipulated by the manufacturer, which at a minimum correspond
to a strength class of 600 N/mm² (38.85 long tons-force/inch²).