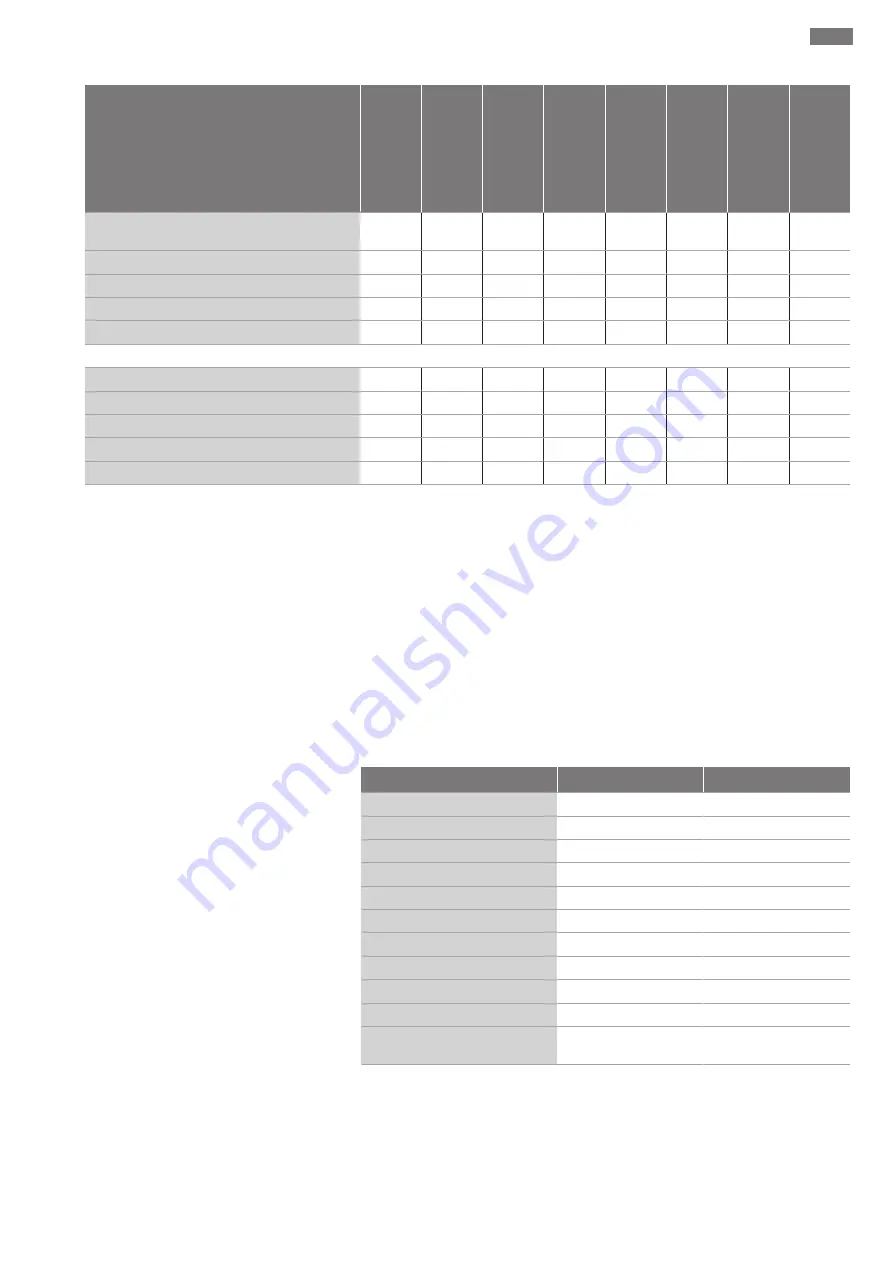
Product description
en
Installation and operating instructions Wilo-EMU TR/TRE 212 ... 326-3
11
TR 212...
TR/E 216...
TR/E 221...
TR/E 226-3...
TRE 312...
TR/E 316...
TR/E 321...
TR/E 326-3...
Nominal diameter in mm (in)
1200
(47)
1600
(63)
2100
(83)
2600
(102)
1200
(47)
1600
(63)
2100
(83)
2600
(102)
Number of blades
2
2
2
2
3
3
3
3
Individual blades
−
•
•
•
•
•
•
•
Propeller pre-assembled
•
−
−
−
•
−
−
−
On-site propeller installation
−
•
•
•
−
•
•
•
Material version
GFK vinyl ester (GFRP vinyl ester)
•
•
•
•
−
•
•
•
PA6G
−
−
−
−
•
−
−
−
High wear-resistant*
•
o
−
−
−
o
−
−
Hub (EN-GJL-250/ASTM A48 Class 35/40B)
•
•
•
•
−
•
•
•
Hub (1.4571/AISI 316TI)
−
−
−
−
•
−
−
−
• = standard, − = not available, o = optional
* = high wear-resistant propeller made of composite PUR/GFK (PUR/GFRP) material
featuring reinforced leading edge.
4.1.2
Gear
Two-stage planetary gear with exchangeable transmissions. Gear bearings have been
dimensioned adequately to absorb resulting stirring forces and not transfer these to the
motor bearing.
4.1.3
Motor
The system is driven by a surface-cooled motor in three-phase current version. The
motor is fitted with maintenance-free, permanently lubricated and appropriately di-
mensioned rolling bearings. The motor is cooled by the fluid around it. Waste heat is
transferred directly to the fluid via the motor housing.
The connection cable is sealed water pressure-tight against the fluid and is sealed lon-
gitudinally watertight. The connection cable has bare cable ends and the standard
length is 10 m (33 ft). Longer cables are available on request.
TR...
TRE...
Fluid temperature
3...40 °C (37...104 °F)**
3...40 °C (37...104 °F)
Protection class
IP68
IP68
Insulation class
H
H
Number of poles
4, 6, 8
4, 6
Max. switching frequency
15/h
15/h
Max. immersion depth
20 m (66 ft)
20 m (66 ft)
Explosion protection
ATEX, FM, CSA
ATEX, FM
Operating mode, immersed
S1
S1
Operating mode, non-immersed
-
-
Motor efficiency class
-
IE3/IE4*
Housing material
EN-GJL-250 (ASTM A48
Class 35/40B)
EN-GJL-250 (ASTM A48
Class 35/40B)
* = motors in efficiency class IE4 have been specified as “E4” in the motor designation.
** = depending on the motor type and motor capacity fluid temperatures up to 60 °C
(140 °F) are possible.
4.1.4
Seal
The system is sealed by a 3-chamber system:
ƒ
Pre-chamber