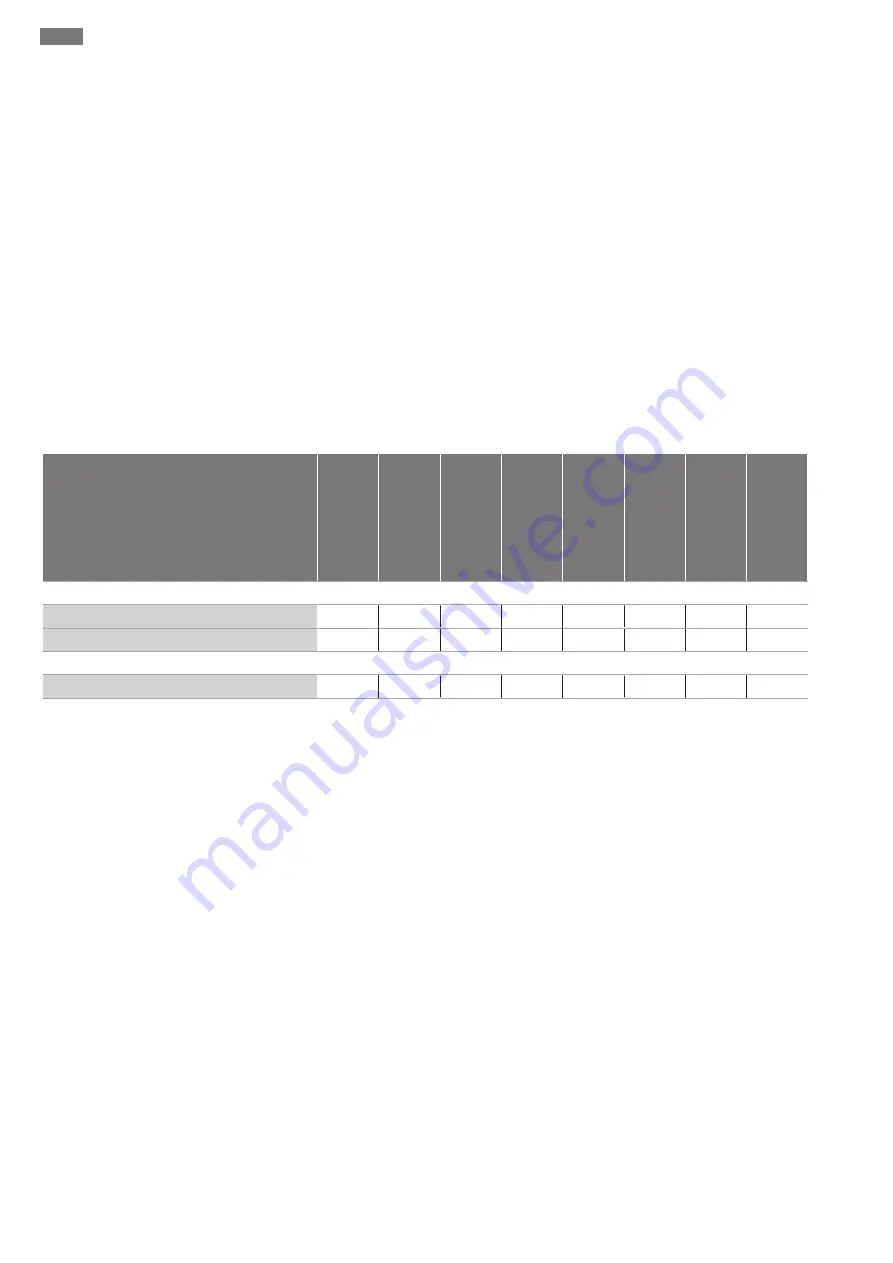
en
Product description
12
WILO SE 2021-05
ƒ
Gear chamber
ƒ
Sealing chamber
Pre-chamber
The high-volume pre-chamber has been filled with gear oil to absorb any leakage at the
seal on the fluid side. A mechanical seal made of solid silicon carbide is used as the seal
on the fluid side. The mechanical seal also features a packing sleeve. The packing sleeve
ensures a permanently corrosion-resistant fit for the mechanical seal. A rotary shaft
seal made of FPM (FKM) seals towards the gear chamber. The pre-chamber can option-
ally be monitored using a pencil electrode.
Gear chamber
The gear chamber has been filled with gear oil to guarantee continuous lubrication of
the planetary gear and the gear bearings. A solid silicon carbide mechanical seal seals
towards the sealing chamber.
Sealing chamber
The high-volume sealing chamber is filled with white oil and absorbs any leakage from
the gear chamber. A rotary shaft seal made of FPM (FKM) seals towards the motor.
4.2
Monitoring devices
Overview of possible monitoring devices:
TR 212...
TR/TRE 216...
TR/TRE 221...
TR/TRE 226-3...
TRE 312...
TR/TRE 316...
TR/TRE 321...
TR/TRE 326-3...
Internal monitoring devices
Motor compartment/sealing chamber*
o
o
o
o
o
o
o
o
Motor winding**
•
•
•
•
•
•
•
•
External monitoring devices
Pre-chamber
o
o
o
o
o
o
o
o
Legend
− = not available/possible, o = optional, • = standard
* In the Ex version, this monitoring is omitted and not substituted!
** A temperature limiter is fitted as standard. The Ex version as per ATEX also features
an installed temperature controller and limiter.
All the monitoring devices fitted must always be connected!
Monitoring the motor compartment and sealing chamber
The motor compartment monitoring protects the motor winding from short-circuits.
Sealing chamber control detects fluid ingress from the gear chamber. In each case, the
humidity is recorded by an electrode in the motor compartment and sealing chamber.
NOTICE! The Ex version does not feature this monitoring unit!
Motor winding monitoring
Thermal motor monitoring protects the motor winding from overheating. A temper-
ature limiter with a bimetallic strip is fitted as standard. Once the activation temper-
ature has been reached, deactivation with reactivation lock must take place.
Optionally, the temperature can also be measured using a PTC sensor. Thermal motor
monitoring can also be designed as temperature control. This allows two temperatures
to be measured. Once the low activation temperature has been reached, an automatic
reactivation can be initiated after the motor has cooled down. The unit is forced to de-
activate with reactivation lock once the high activation temperature has been reached.