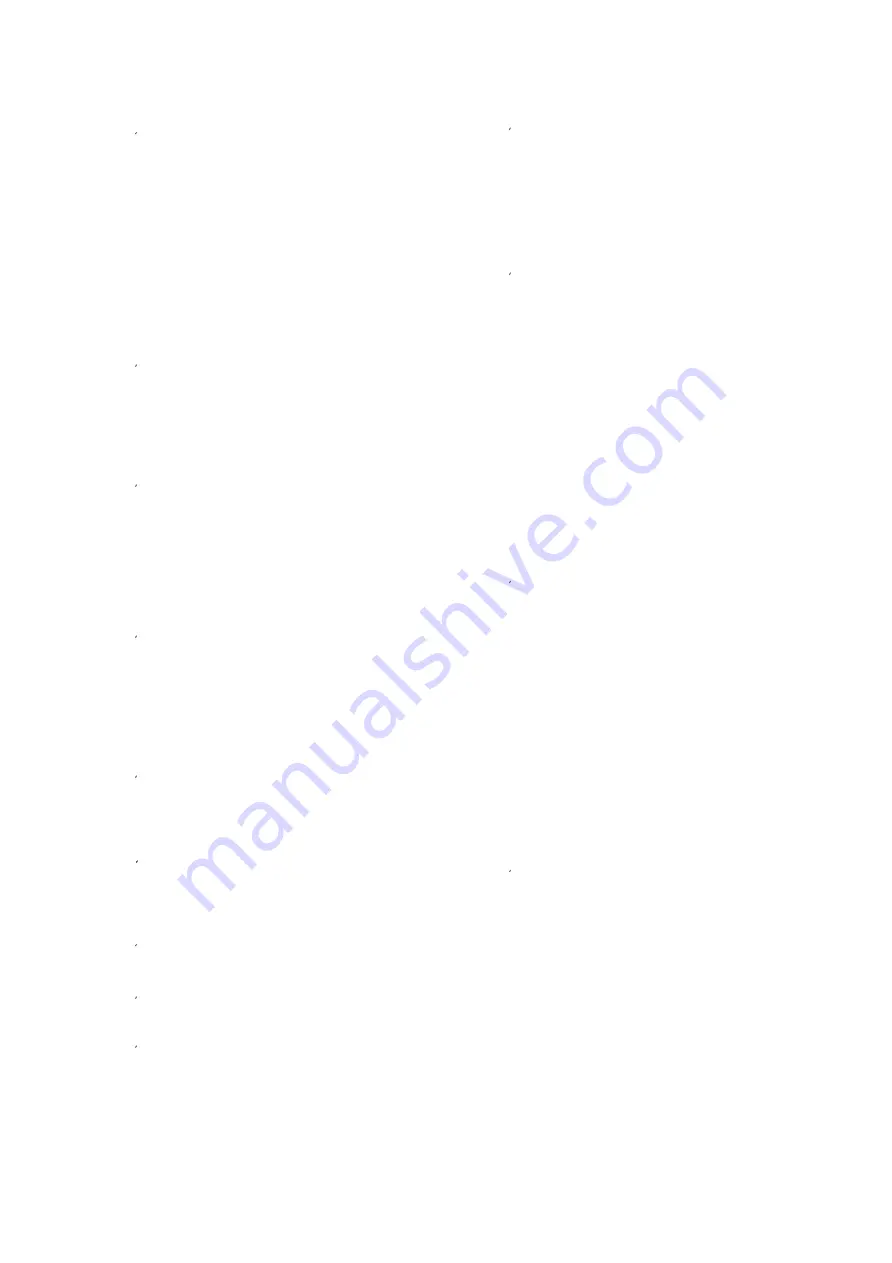
Installation and operating instructions Wilo
–
SCPV pumps
15
7.2.2 Leveling and installing the sole plate
Sole plates have machined surfaces on top and
bottom. Therefore no distortion of the sole plate
can be caused by the weight of the unit when
supported on a leveled surface. But initially the
foundation surface will be rough to key the final
grout and the motor stool could distort if mounted
directly on this uneven surface. To avoid this
distortion and to provide a suitable base for
leveling, steel packing blocks must be positioned at
suitable spacing on the foundation surface, a
minimum requirement being one on each side of
every foundation bolt. Ensure the surface beneath
each packing block is solid by crushing any
protrusion or alternatively each block may be
placed on a thin screed of cement.
Lift the sole plate and lower it on the foundation.
Insert the foundation bolts through the holes in the
sole plate and screw a nut on to each bolt until the
bolt protrudes through the nut by a length, which
is sufficient to accommodate a locknut.
Level the sole plate as follows:
Place an engineer
’
s level (sensitive to an error of
0.05 mm per 250 mm) on the machined top
surfaces of the sole plate. The leveling pads if
provided.
NOTE
:
These machined surfaces where level is being
checked must be clean and free from paint, burrs etc
Adjust the level of the sole plate by inserting shims
between the sole plate and the packer plate until
the sole plate is leveled and supported on all the
packing blocks at the height required for the
connection of suction and discharge branches. For
checking the levels across two pads, I-beam type
straight edge should be used extensively in
conjunctions with enginee
r’s
level. Level should be
achieved within 0.05 mm per 250 mm.
When the sole plate is leveled, grout in the
foundation bolts. Care should be taken so as not to
disturb the verticality of foundation bolts. For
grouting use rich mix of 1:1:2 of cement, sand and
gravel.
When the grout has set, gently but firmly tighten
the foundation bolts; then screw on and tighten
the lock nuts. Care must be taken not to distort the
sole plate or loosen the foundation bolts in the
grout by excessive tightening.
Carefully re-check the level of the top surface of
sole plate and make adjustments that are
necessary by fine shimming.
Position the pump on the sole plate. Place the
motor on motor stool, which is fixed to pump
casing previously.
When the sole plate is leveled and the pump and
motor are in proper position, run the final grout
beneath the motor stool. Allow minimum seven
days time for curing before commencing the pipe
work. Grout mix in the proportion specified earlier
for foundation bolt grouting should be used.
7.2.3
Alignment of the pumps and its driving units
When the sole plate is leveled and the satisfactory
alignment is completed, proceed with connection of
suction & delivery piping. Recheck the alignment
after piping and run the final grout beneath the base
plate. Allow minimum seven days time for curing.
Grout mix in the proportion specified earlier for
foundation bolt grouting should be used. It is further
recommend that all hollow pockets in the base plate
shall be filled after curing of earlier grout.
The following procedures outline recommended
practice given in BS-3170 in 1972 (Appendix A) for
checking shaft alignment. This method is
independent of the truth of the coupling or shaft and
is therefore not affected by canted coupling faces or
eccentricity of the outside diameter of the coupling.
Before commencing the alignment, rotate each shaft
independently to check that the bearings run freely
and that the shaft is true to 0.1mm or better. Check
that no damage can be caused when the shaft of the
driven unit is turned. Coupling should be loosely
coupled and the halves must be free to move relative
to each other, otherwise gauge Indicators can be
incorrect. Where, tightly fitting pins or spring prevent
loose coupling, the springs or pins should be
removed, a line scribed across both half couplings
and readings taken only when the two marks are
aligned.
Angular alignment (Refer Figure: 3)
After isolating the driven unit from its power supply,
clamp two dial indicators are dramatically opposite
points on one half coupling or to the shaft behind it
with the plunger resting on the back of the other half
coupling. Rotate the coupling unit the gauges are in
line vertically and set the dial to read zero. Rotate the
coupling by 180° and record the readings on each
gauge. The readings should be identical, though not
necessarily zero. Either positive or negative readings
are acceptable provided they are equally positive or
negative. Adjust the position of one of the units if
necessary. Rotate the couplings unit the gauges are
in the line horizontally and adjust the dial to zero.
Repeat the operation outlined above by rotating the
coupling by 180°. In case where fitment of dial gauge
is not feasible check gap between two coupling half
with the help of filler gauge.
Radial alignment (Refer Figure: 3)
Clamp a dial gauge on one of the couplings or to the
shaft with the plunger resting on the rim of the other
half coupling. Set the dial zero. Rotate the coupling
and note the reading at each quarter revolution. Any
variation in the readings indicates the deviation from
alignment and the position of one of the units must
be adjusted until the readings at each quarter
revolution are identical or within the tolerances given
below.