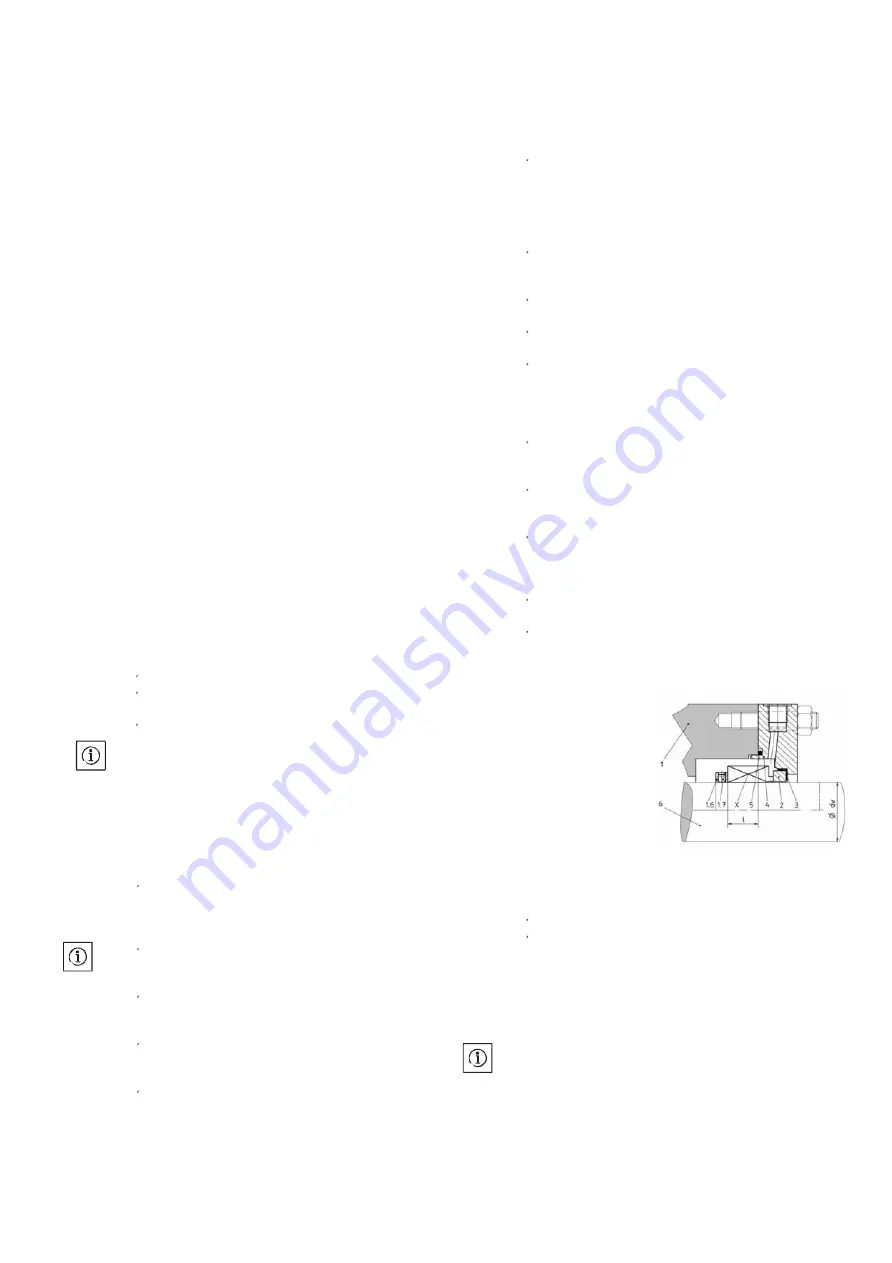
Installation and operating instructions Wilo
–
SCPV pumps
25
until required for replacement or refit on to the
spindle if needed. In case of immediate use,
coating of rust preventive oil is not
necessary.(See Annexure 2)
9.4.6 Stuffing box bush
Check bore of stuffing box bush and compare
with sleeve diameter. If "clearance
”
is
excessive, the bush should be renewed.
9.4.7 Shaft
Check the shaft for trueness. Since sleeves
protect shaft and very little portion is exposed,
no wear is expected. However in case of
aggressive liquid, the exposed portion should
be inspected for corrosion attack
9.4.8 Mechanical seal
Ensure that the sliding face do not have any
scratches or abnormal wear. Verify that the
driving collar is well screwed on the shaft at the
right place . Check that no material block the
spring action
9.5
Reassembling the pump
9.5.1 Reassembly of rotating element
If rotating element has been completely
dismantled, the correct position for the
impeller must be established as marked on the
shaft prior to dismantling. Then commence
reassembly as under.
Fit the Intermediate Shaft Sleeves.
Fit the impeller keys in the keyway of the
spindle.
Fit the Impellers along with Neck rings on
the spindle in correct position.
Note:
While assembling stainless steel component
molybdenum-disulphide
paste should be
applied to prevent galling / seizure and also to
facilitate easy removal in future.
9.5.2 Re-assembly of the pump
(Gland pack version pump)
Ensure that casing is clean, dry and free from
foreign matter. Clean casing neck ring
seating thoroughly and ensure they have no
burrs
Carefully insert the element into the bottom
half casing, with the help of withdrawal gear
trolley / crane.
Fix water throwers, dust covers and outer
end covers to bearing housing by their
setscrews.
Cut a gasket from 0.25 mm thick black joint
paper or similar gasket material and locate on
split flange of bottom half casing.
Position the top half casing by crane / chain
pulley block with respect bottom half casing
so that split faces match. Use withdrawal
gear trolley / crane to support the top of
casing.
Fit the split flange studs. Align dowel holes and fit
dowel pins before tightening the nuts. The nuts
must be tightened evenly in the diagonally opposite
sequence. (Refer Figure: 9)
9.5.3 Reassembly of pump
(Mechanical seal version)
Ensure that casing is clean, dry and free from
foreign matter. Clean casing neck ring seating
thoroughly and ensure they have no burrs
Carefully place the adjusting ring of mechanical
seal at its premarked position
Place the grub screw at its position on the
adjusting ring
The O-ring may be oiled to reduce friction during
installation of the seal. But the EP- rubber O-ring
should not come in contact with oil or grease. In
this casse lubrication with glycrol or water is
recommended
Never cover the sliding faces with lubricants , they
should be assembled completely dry clean and
dust free
When pressuring staionary seal make sure that the
pressure distrubition is unifor. The O-ring must be
fitted using water or glycerolonly
Crowned drive pins must be replaced whenever
the seal is dismantled. During insertion of the
stationary seats, especially those of special carbon,
care must be taken to exert pressure evenly
Now check the distance of seal as shown in the
figure and adjust its value as per values given table
For rest parts follow the above explained
procedure as per gland pack version pump
Location of mechanical seal of shaft
1) Pump casing
2) Stationary seat
3) Stationary seat
4) Gland plate
5) O-ring
6) Shaft
X. Mechanical seal
1.6 Abutment ring
1.7 Abutment ring fixing screw
9.5.4 Final Assembly
Refit and reconnect pump half coupling.
Prime the pump and return it to service
NOTE:
While assembling stainless steel component,
molybdenum-disulphide paste should be applied to
prevent galling / seizure and also to facilitate easy
removal in future.
NOTE:
Change the gasket each time when the pump is
opened.