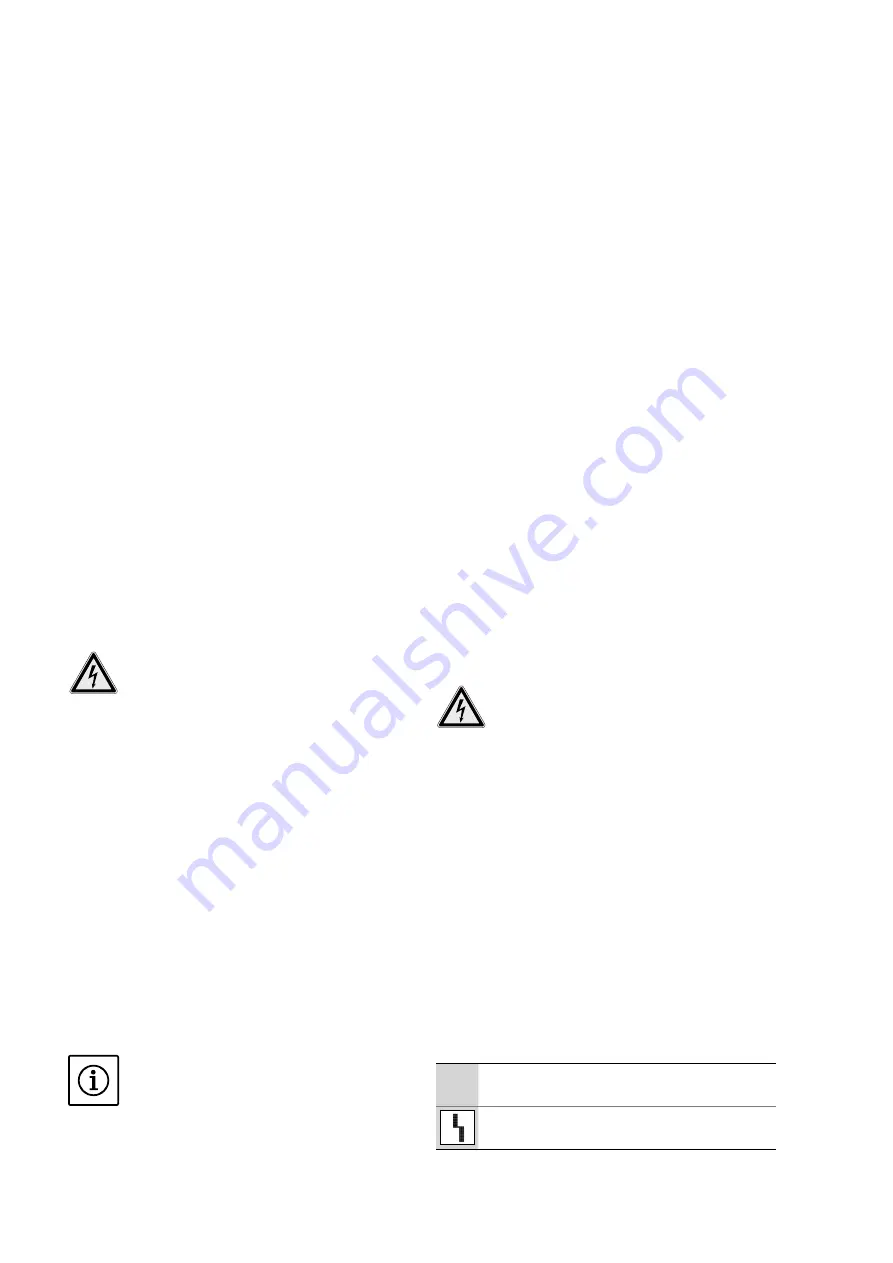
48
WILO SE 05/2016 V05 DIN A4
English
MAINTENANCE AND REPAIR
2. Switch off the entire unit so it is voltage-free and
secure it against accidental activation.
3. If the terminals for SBM, SSM and HW are occu-
pied, the external voltage source present there
must also be switched so it is voltage-free.
4. Disconnect all power supply cables and pull these
out of the threaded cable connections.
5. Connect the ends of the power supply cables so
that no moisture can enter into the cable.
6. Dismount the switchgear by undoing the screws
on the substructure or on the pedestal.
8.3.1. Return delivery/storage
For shipping purposes, the switchgear must be
packaged so it is protected against knocks and
waterproof.
Please also refer to the “Transport and storage”
section.
8.4. Disposal
Proper disposal of this product avoids damage to
the environment and risks to personal health.
• Use the services of public or private waste dis-
posal companies, or consult them for the disposal
of the product or parts thereof.
• For more information on proper disposal, please
contact your local council or waste disposal offi ce
or the supplier from whom you obtained the
product.
9. Maintenance and repair
POTENTIALLY fatal danger due to electrical
voltage!
When performing work on the uncovered
switchgear, there is a risk of fatal electric
shocks occurring. During all work, the switch-
gear must be disconnected from the electric-
ity network and secured against reactivation
without permission. All electrical work must
be carried out by a qualifi ed electrician.
After completing maintenance or repair work,
the switchgear must be connected according to
the “Installation” section and activated as under
“Commissioning”.
Maintenance or repair work and/or con-
structional changes that are not listed in this
operating and maintenance manual may only be
carried out by the manufacturer or by author-
ised service centres.
9.1. Maintenance intervals
To ensure reliable operation, various maintenance
tasks must be carried out regularly.
NOTE
When used in sewage lifting units inside build-
ings or on land plots, the maintenance intervals
and work shown in DIN EN 12056‐4 must be
adhered to.
Before initial commissioning or after a longer
period of storage:
• Clean switchgear
Yearly
• Inspect contactor contacts for melting
9.2. Maintenance tasks
Prior to maintenance work, the switchgear must
be switched off as described under “Temporary
shutdown”. Maintenance work may only be car-
ried out by qualifi ed persons.
9.2.1. Clean switchgear
Use a damp cotton cloth to clean the switchgear.
Do not use any aggressive or scouring cleaners
or fl uids!
9.2.2. Inspect contactor contacts for melting
Have the contacts checked for melting by a quali-
fi ed electrician or Wilo Customer Service.
If more serious combustion is ascertained, have
the affected contacts replaced by a specialist
electrician or Wilo Customer Service.
9.3. Repairs
Prior to repair work, the switchgear must be
switched off as described under “Final shutdown”
and all power supply cables dismantled. Repair
work must be carried out by an authorised service
centre or Wilo Customer Service.
10. Troubleshooting and possible solutions
DANGER due to electrical voltage!
Improper procedures during electrical work
may result in fatal injuries caused by electrical
voltage! This work may only be carried out by
a qualifi ed electrician.
Possible faults are displayed for 30 seconds on
the display using an alphanumeric code. Accord-
ing to the fault shown, the connected pump or
signal transmitter must be checked for correct
operation and replaced if necessary.
Only perform this work if suitably qualifi ed
personnel are available. Electrical work must be
carried out by qualifi ed electricians for instance.
We recommend always having this work carried
out by Wilo Customer Service.
Unsanctioned modifi cations to the switchgear are
made at the operator's own risk and release the
manufacturer from any warranty obligations.
10.1. Fault indication
Overview of symbols:
E06
Error code
Error icon
Faults are displayed in various ways:
Summary of Contents for Control SC-L
Page 2: ...Fig 2B Fig 2A Fig 1 1 2 3 4 1 2 3 3 4 5 6 6 7 1 2 3 3 4 6 5 7...
Page 26: ......
Page 28: ......