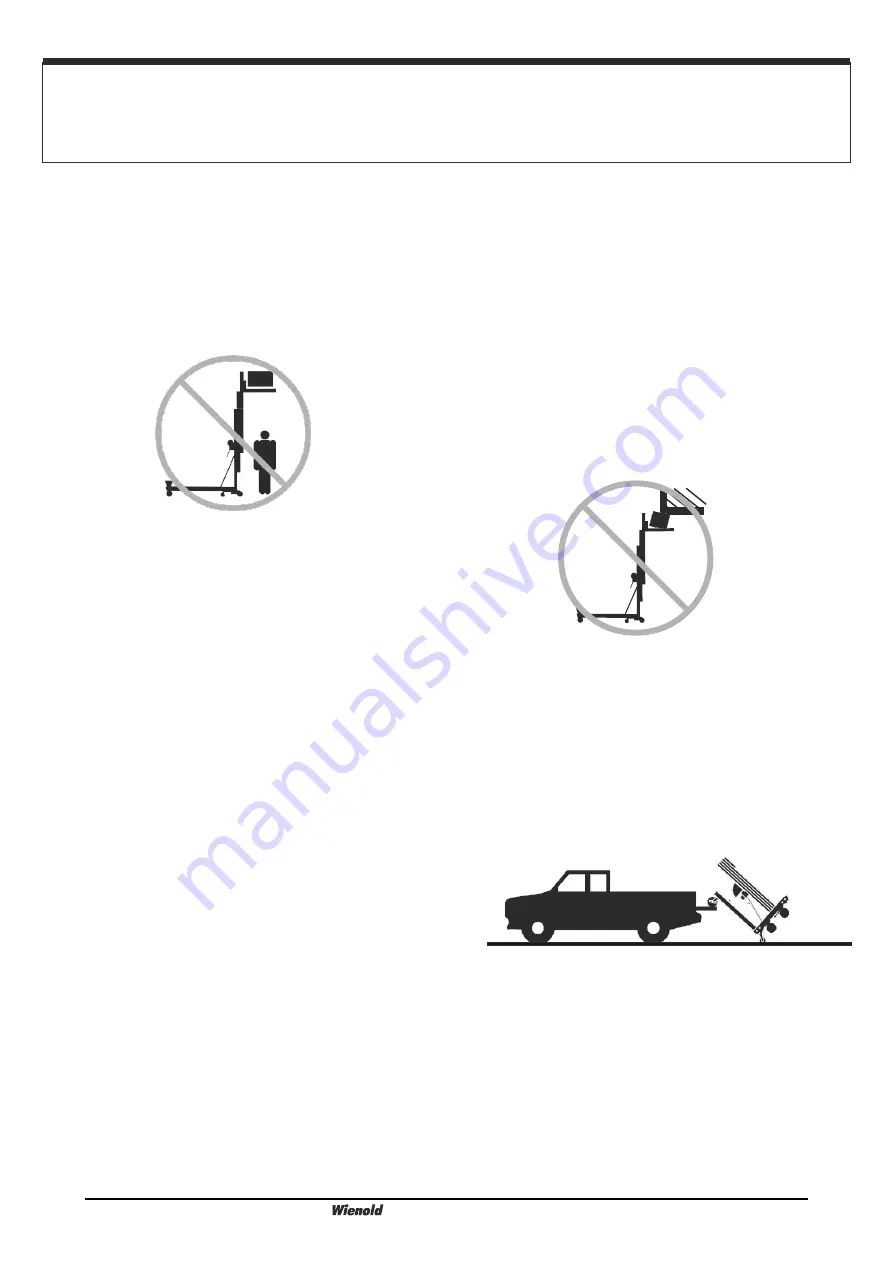
Glass and Material Lift
GML 800+
16
Operating Manual
GML 800+
Safety Instructions
Crushing Hazards
Do not raise if the load is not
1.
correctly centered on the loading accessory.
2.
correctly secured to the loading accessory.
Never stand under the load as it is being raised or lowered
or suspended. Do not allow others to stand in the lifting area
when the unit is being operated.
Standing under the load is prohibited.
The load may fall from between 30 and 91 cm before
the safety brake mechanism activates the locking of
the mast elements.
Do not lower the load unless the area below is clear
of personnel and obstructions.
Keep hands and fingers away from the winch, the folding
outriggers, loading accessories and any other potential
pinch points.
Maintain a firm grip on the loading accessory when the safety
bolt is removed. Otherwise the loading accessory will fall.
Maintain a firm grip on the outrigger when the safety bolt
is removed. Otherwise the outrigger will fall.
Maintain a firm grip on the winch crank handle. The winch
brakes engage automatically when you stop winding.
The crank handle must not move when you stop winding.
Standard Forks
Only use appropriate loading accessories when lifting a
load. Always ensure before loading that the loading accessory
used is suitable for the load and is correctly secured.
Only raise the load when the loading accessory has been
correctly installed and the load has been correctly aligned and
secured. Always take into account the relation between lifting
height and load center.
Collision Hazards
Check the working area for overhead obstructions or other
potential sources of danger.
Always plan your route if transporting a load on site using this unit.
Avoid sharp turns, inclines or voids in the ground. Only move the lift
when in transport position!
Loading
When loading the lift (for transport), always ensure that the lift
and the transport vehicle are on an even ground.
Always use the correct lifting techniques and always use the snap
hook on top of the lift when using a crane or the forklift receptors
when loading with a forklift.